The popularity of machine vision for quality assurance (QA) is increasing, but conventional systems lack the flexibility that most manufacturers need.
Achieving End-to-end Automation With Autonomous Machine Vision
Yonatan Hyatt, CTO | Inspekto
Inspekto, the pioneer of Autonomous Machine Vision, has created off-the-shelf, flexible machine vision systems that can now be integrated into automated production lines, either specifically engineered or in standardised automation cells, to achieve end-to-end automation. Here Yonatan Hyatt, the company’s CTO, explains the benefits of this innovative automation setup.
An increasingly competitive landscape and evolving consumers’ demands have changed manufacturing, which has become more focused on automating production lines, increasingly using standardised automation cells, and on producing solutions for high-mix-low-volume manufacturing.
These manufacturing models require extremely versatile equipment that can be adapted to the frequently changing needs of the production line. At the same time, components have to fit into standardised automation cells like building blocks, each contributing to automating one step of the production process.
Currently, there is a wide range of components for automation cells on the market, such as cobots, grippers, handlers, controllers and more, which automate a huge variety of processes. However, all of this is almost pointless if the quality of the processed product cannot be reliably established. The final link in automation is missing when visual inspection is still performed manually or with complex, case-specific solutions, reducing its versatility and increasing the total cost of ownership (TCO).
Machine vision is essential to maintain quality on every stage of production and to replace unreliable manual inspection. However, the development of the sector has historically been stifled by the case-specific complexity, cost and long lead times of traditional machine vision solutions. To meet the changing needs of manufacturers and fit into standardised automation cells, industrial quality inspection has to evolve from traditional, to autonomous machine vision.
Visual inspection made easy
Traditionally, machine vision systems for industrial QA are deployed to inspect a single type of product at a specific location along the production line. This means that most systems are suitable for only one use case at a time. Each use case constitutes a project, which involves building a customised machine vision solution to detect defects that typically happen when producing that particular item. Building, integrating, training and testing the solution is a complex, expensive and time-consuming process that traditionally requires the help of a machine vision expert. For multi-product inspection, where different products are inspected on the same QA station, the process is even more costly and complicated. Moreover, when a solution is customised, the customer needs to rely on the promises of a machine vision expert and has no control on how the final solution is developed and implemented.
Another disadvantage is that the resulting machine vision solution will only be able to detect defects that were defined in advance, when the system was trained to recognise them. New defects appearing on the line or unforeseen defects will not be detected, and any changes on the production lines will require a new project to update the machine vision solution to cope with the new appearance of the part or the new defects on it.
These typical constraints of machine vision solutions can be overcome with Autonomous Machine Vision (AMV), a technological breakthrough that powers systems that are versatile, easy and quick to deploy or to adjust to dynamic production lines. In this way, AMV completes the circle of automating every step of production, from the initial phases to ensuring the quality of the final product.
Autonomous Machine Vision AI
The technology that made this type of solutions possible is known as Autonomous Machine Vision AI (AMV-AI). It uses specifically developed AI for every stage of the inspection process to offer systems that are completely autonomous, from self-adjusting the electro-optics settings and the patent-pending anti-reflection illumination, to autonomously determining how many samples are needed in order to learn the characteristics of the inspected part. AMV-AI powers end-to-end devices that integrate software and hardware for optimal autonomous visual inspection. These devices can be easily installed and set to inspect a variety of use cases in countless scenarios, from a single product manually presented to the system, to multiple products on a conveyor belt. AMV systems can also be moved to a different location if needed.
Unlike traditional machine vision solutions, which must be tailored for a specific project and assembled by an expert, AMV systems are pre-trained, off-the-shelf products that can be set up in a short time, without any previous expertise in machine vision. The user can simply unbox the product, trace the outline of the item to inspect with a regular mouse, present 20 to 30 good sample items to the system, and start inspecting and detecting any kind of defect, foreseen or unforeseen.
The same simple process can be repeated any time the manufacturer wants to inspect a new product, which makes AMV ideal for any production line, especially dynamic ones.
Joining forces
As AI and robotics become increasingly involved in every aspect of production, AMV combines these technologies to maximise performance and quality. AMV systems can be integrated on a manufacturing line in a variety of ways. For example, the flexibility of AMV systems can be further enhanced by integrating them with other technologies, such as cobots, to create automation cells where all processes are automated, including quality assurance. Inspekto has recently tested this new possibility by integrating the only AMV system currently on the market, the INSPEKTO S70, with a robotic arm that presents different items to be inspected one after the other.
This has been recently implemented by one of the world’s leading developers of integrated automation solutions, who deploys one of its cobots to present a variety of components to the INSPEKTO S70 inspection system.
However, the combination of machine vision and cobots can also work the other way around, with the INSPEKTO S70 mounted on a robotic arm that allows it to move from one product to the other, performing accurate and reliable inspection of a variety of items.
This set up is only possible because the INSPEKTO S70 dynamically adjusts its electro-optics settings without human intervention, adapting them to the characteristics of each product to be inspected and the environmental conditions at hand, such as lighting, contrast and depth of field. Its Recognition AI engine allows the system to detect any part from the very first sample shown to it. Additionally, its pre-trained, self-supervised Inspection AI engine allows it to adapt to the variance and tolerance of the produced items, and to detect any defect without having to see example of the expected defects.
Achieving end-to-end automation
AMV systems can be integrated with practically any cobot on the market. The combination of machine vision and flexible robotic solutions allows manufacturers to achieve unprecedented flexibility, and to adapt their QA processes to the needs of rapidly changing production and assembly lines.
This cutting-edge QA setup is ideal for new automated lines which need to be built with shorter-than-usual cycle times. It is also ideal for high-mix-low-volume manufacturing, customized batch manufacturing, and agile production methods such as additive manufacturing (AM). In these scenarios, investing in a traditional machine vision solution may not be convenient, because the cost, lead times and complexity of these projects conflict with the inherent agility of the production methods.
Instead, a combination of AMV systems and cobots might be the ideal solution to implement reliable, versatile, automated QA without slowing down production. Additionally, the combined cost of an AMV system and a low-cost cobot can be drastically lower than that of a traditional, cumbersome machine vision solution, making this combo ideal also for small and medium manufacturing lines looking for a quick return on investment (ROI) and to move employees to a more important tasks.
AMV systems, specifically the INSPEKTO S70, represent the only wide-applicable machine vision solution currently available, and their flexibility complements that of automation solutions recently developed by a wide variety of automation companies and start-ups. Integrating these solutions to automate the entire production process will allow manufacturers to reach end-to-end automation, giving them a huge competitive advantage and ensuring their business is future proofed.
For more information on Autonomous Machine Vision Solution, get in touch with the Inspekto team.
The content & opinions in this article are the author’s and do not necessarily represent the views of RoboticsTomorrow
Comments (0)
This post does not have any comments. Be the first to leave a comment below.
Featured Product
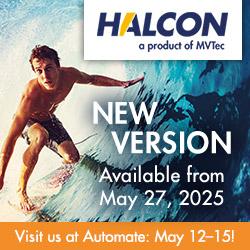