Tesla’s automation strategy has shifted over the last five years. By investigating where Tesla made mistakes and where it excelled, the reader will benefit from Tesla’s hard-earned lessons and gain an understanding of how to build an automation strategy.
2022 Top Article - How Tesla Used Robotics to Survive "Production Hell" and Became the World's Most Advanced Car Manufacturer
Article from | The Robot Remix
Jack Pearson is the Commercial Director and Co-Founder of Remix Robotics - an automation design agency that builds custom robotic systems for companies including DHL, Mercedes F1 & the Small Robot Company. Subscribe to The Robot Remix Newsletter to learn more.
Introduction
In 2018 Tesla was on the brink of bankruptcy. They had invested billions into a new factory filled with robots that hardly worked and couldn’t meet production quotas. Today Tesla is the 6th most valuable company in the world and its heavily automated production process is ten years ahead of competitors. How did they build themselves back from the brink and turn robotics from strategic failure to success?
This article will review how Tesla’s automation strategy has shifted over the last five years.
The Context
A detailed introduction of Tesla and its famous/infamous founder Elon Musk shouldn't really be required. Tesla is one of the best known car manufacturers and basically kicked off the electric vehicle revolution.
When Tesla was still a start-up they published a “Top Secret” plan for making electric vehicles the industry standard -
-
Build a sports car
-
Use that money to build an affordable car
-
Use that money to build an even more affordable car
-
While doing the above, also provide zero-emission electric power generation options [1]
This approach worked successfully for Step 1 of the secret plan. The earlier models - Roadster, Model S, and Model X are all luxury vehicles produced at lower volumes with the ability to use manual labour to ensure high quality was maintained. Sidestepping many of the challenges of automotive mass production.
The Tesla line-up - Models S, 3, X, Y & R
In 2016 Tesla decided it was time to move to Step 2 and develop a more affordable, high volume car, bringing itself into the “real car company” club. They launched a wildly successful presale for its sedan style Model 3, generating 325,000 orders ($11.4 billion). To meet these orders, Tesla was promising to produce 5000 cars/week by 2018[3]. Putting this into perspective, this was a commitment to build a new and relatively untested car filled with innovative features at a rate of 1 car every 2 minutes. To complicate matters, Musk was also set on completely changing how these cars were being made - which is where automation comes in.
Tesla’s 2016 Automation Strategy
Tesla’s production strategy for the Model 3 can be broken up into two core facets -
1) The “Alien Dreadnaught”
“Our internal code name for the factory, the machine that builds the machine, is the alien dreadnought, when our factory looks like an alien dreadnought, then we know it’s probably right.”
To meet Tesla’s uncompromising production goals, Musk settled on an equally uncompromising production strategy - full automation, no ifs, ands or buts. The goal was to remove every single human operator and only stop when the facility looked like an alien spaceship. The logic was that increasing the volume and velocity of vehicle production required moving from “people speed to robot speed”. Using First Principles, Musk reasoned that if mechanisms can undertake tasks faster, more consistently and more accurately - then Tesla should aim for as much automation as possible and do so as quickly.
2) Build Hardware Like Software
Musk came up as a software entrepreneur and his approach to hardware is heavily influenced by agile software development. Silicon Valley essentially runs on the Lean Startup approach, rather than building something alone in a dark basement, the goal is to get a product into customers’ hands as quickly as possible to understand their needs through tangible experience and iterate your product to meet these needs. This is ideal for software as it’s quick and easy to update a product and redistribute it without costs or friction. Reid Hoffman, the founder of LinkedIn & Musk’s colleague at PayPal, epitomised this approach by saying -
“If you are not embarrassed by the first version of your product, you’ve launched too late”.
For Tesla, following this approach meant shortening development cycles, forgoing trial production runs and diving straight into full-scale production. That is, full-scale production of a cutting edge product at the edge of feasibility, at volumes 100X higher than they had experienced, using a new and untested production approach. Unfortunately, they don’t call it hardware for nothing... the same rules do not apply.
https://xkcd.com/1428/ & https://thedesignteam.io/if-screen-product-designers-designed-physical-products-10cdd3ac4fdc
The Result - ‘Production Hell’
In late 2016 Musk set about converting an old GM / Toyota factory in Fremont, California, into his Alien Dreadnaught. Tesla gave the Model 3 engineers free rein to redesign the site for mass production. They invested in developing in-house robotics capabilities by acquiring two automation companies, Grohmann & Perbix.
With the vision of creating an alien spaceship firmly set, Tesla set about automating everything in sight. They purchased over 1,000 robots including 6-axis arms from Kuka and Fanuc and automated vehicles from Omron. They applied them across the process tackling relatively routine tasks such as welding or painting through to entirely novel tasks like wire harness assembly.
By April 2018, everything was not going to plan. The company was far behind schedule, only producing an average of 2000 cars/week and haemorrhaging $100 million dollars a week. Amid mass resignations, health and safety incidents and general public ridicule, Musk dubbed the period “Production Hell”.
The robots were not panning out as hoped. They struggled to achieve the required throughputs and weren't hitting quality requirements. Small inefficiencies compounded and resulted in substantial delays. As a stop-gap, Tesla hired 100s of temporary workers to pick up the slack.
Why Did This Happen?
Much of Tesla’s production hell was blamed on excessive automation but what caused such a significant deviation between expectations and reality? Why did their automation strategy fail?
Tesla tried to do everything all at once. They had a new product being made by a new process at a new site. At each level, Tesla was pushing the boundaries and going against orthodoxy.
New Site
The first constraint that Tesla faced was the site itself. They did not have a blank canvas in Fremont. The facility was initially opened in 1962 and required a complete overhaul to convert it into the hyper-automated electric vehicle production machine of Musk's dreams. Tesla had the budget for this redesign but due to its presale promises, it did not have the time.
New Product
The Model 3 was jam-packed with features that were new for Tesla and unique for the overall industry. They were doing this at a lower price than any of their other models.
The level of innovation resulted in updates and changes. Due to the tight deadlines, these occured during the production ramp-up. In such a complex process, tiny changes create minor variances, which over many steps can compound and have huge impacts on upstream operations.
A prominent example includes the battery cells which were updated from the Model S. The cells had improved capacity which resulted in a slight increase in size over the standard 18650 cells used in previous Models. An automated process had been designed to pack cells into their trays, 50% faster than human operators could[4]. Unfortunately, the change in cell size had not been accounted for and resulted in increased error rates, requiring manual operators to take over the system before it was redesigned.
New Process
In many ways, the factory design was as innovative as the product design. Automation was being relied on for everything from incredibly precise and dexterous tasks like wire harness assembly to heavy-duty tasks like lifting entire vehicles. The Fremont site replaced the original gantry systems with 10 of the largest robots available and in typical Tesla style, named them after X-men characters.
The "Iceman" robots - https://www.businessinsider.in/meet-iceman-and-wolverine-the-two-coolest-robots-in-teslas-factory/articleshow/49149310.cms
The innovation across both the product & the process was not given enough time and testing to ensure reliability and repeatability. The frequent changes & variability could not be accounted for and attempts to make the automation generalisable with machine vision and other intelligent technologies were unsuccessful.
As Bill Gates stated in his first & second rule of technology -
Rule 1: Automation applied to an efficient operation will magnify efficiencies
Rule 2: Automation applied to an inefficient operation will magnify the inefficiency
Meeting the appropriate quality levels required a finely tuned production system but -
-
Innovation and uncertainty across the production process,
-
Ridiculous production targets and an extreme ramp-up,
-
An unmanageable number of new and insufficiently tested robots
made it impossible to find enough hours to refine each robot cell and ensure it met its required speed and quality.
Tesla’s Updated Automation Strategy
“Based on every measurable metric, Model 3 is already the highest quality vehicle we have ever produced, and this is unquestionably due in large part to automation” - Elon Musk
During the Model 3’s production, Tesla’s future seemed in question. With bankruptcy a real possibility, automation appeared to be one of the major culprits. Today things are a little different - Tesla did not go out of business and successfully reached its production targets. More than just scraping through to survival, Tesla is now thriving - the Model 3 is regarded as one of the best cars ever made[6], Tesla became the 6th company to reach a trillion dollars and as of April 2022, Musk is the richest man on earth.
Patient customers and goodwill from deep-pocketed investors played a factor, but in the end, self-imposed constraints and challenges led to innovations in production that have paid off 100X. Sandy Munro, a manufacturing consultant (famously not a good news consultant) who had previously been critical of Tesla’s design, changed his option after completing a teardown of the new car -
“I said in the past that Tesla with the Model 3 was probably five to eight years ahead of everybody else,” he said. “And now, in some cases, I think that in some areas of the car, Tesla is 10 years ahead, especially when it comes to the manufacturing.” - Sandy Munro
Rather than lose faith in robotics after all the friction and integration challenges, Tesla has subtly reshaped their approach while doubling down on automation.
To learn how Tesla changed their automation strategy and the 3 tenants of its new approach – Check out the full article at The Robot Remix.
This article was originally published in The Robot Remix. Subscribe for strategic insight into the robotics and automation industry.
References
[1] https://www.tesla.com/blog/secret-tesla-motors-master-plan-just-between-you-and-me
[2] https://jamesclear.com/first-principles
[3] https://www.theguardian.com/technology/2016/apr/04/tesla-motors-sells-10bn-model-3-two-days
[4] https://www.teslarati.com/tesla-factory-upgrade-facts-figures/
[6] https://www.youtube.com/watch?v=t705r8ICkRw&feature=emb_title&ab_channel=EverydayAstronaut
The content & opinions in this article are the author’s and do not necessarily represent the views of RoboticsTomorrow
Comments (0)
This post does not have any comments. Be the first to leave a comment below.
Featured Product
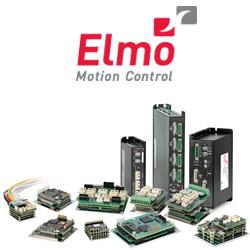