Understanding the truth behind your inventory involves not just cycle counting of stored inventory but also accurate tracking of inventory movement and reconciling it in near real time against your WMS.
What is Inventory Accuracy… And Why Should 3PLs and Brands Care?
KG Ganapathi and Craig Dowley | VIMAAN
Inventory accuracy is a challenge in almost every warehouse we walk into, and the reasons behind the inaccuracies vary. Understanding the truth behind your inventory involves not just cycle counting of stored inventory but also accurate tracking of inventory movement and reconciling it in near real time against your WMS. As we will see below, the failure to ensure accurate tracking of inventory can cost brands and 3PLs millions of dollars every year even within a single warehouse. using handheld barcode readers to track your inventory? Introduced to warehouses over a decade ago, the promise of these handheld devices was to allow for easy and mobile barcode capture. If you have been using handheld barcode readers for a while you may agree that productivity improvements plateaued long ago. Recent studies have shown that handheld barcode readers are problematic for product inventory due to their slow scan speeds, poor network connectivity and short battery lives. Additionally, warehouses can’t get the full picture of their inventory by simply relying on barcodes; there is still a considerable amount of manual inventory inspection that requires costly overhead.
Important Areas in the Warehouse That Require Inventory Accuracy
Inventory Accuracy in Storage Racks
Let’s start with inventory accuracy for inventory stored in racks in typical B2B distribution centers and warehouses. These warehouses typically cover hundreds of thousands of square feet, are 30-40 feet tall, and hold tens of thousands of “bin locations”. Naturally, it is impractical to verify every single location and its contents against the WMS frequently. This is why the “cycle count” was conceived. A cycle count involves audits of parts of the warehouse on a periodic “cycle”, such that the contents of each bin are covered once every month or every quarter. Such an infrequent verification of each bin of course does nothing to ensure the veracity of the WMS for that bin in the time interval between two audits, which can run as much as a whole year!
Walking miles of warehouse aisles counting and recounting stored inventory is one of the least desirable assignments an Associated can receive.
Since cycle counting is a manual process for most warehouses, it is highly dependent on disciplined and precise labor. Walking miles of warehouse aisles counting and recounting stored inventory is one of the least desirable assignments an associate can receive. Couple this tedious task with an increasingly difficult to hire workforce and it’s no wonder that inventory accuracy is an increasingly painful thorn in the side of warehouse operators today.
Cycle counting is not only expensive; it can also be disruptive to day-to-day operations. If a specific shelf and/or aisle is being audited, it becomes unavailable for picking or put away. Now just imagine how disruptive this could be for a 500,000 sq foot warehouse with 40ft high bays; this type of manual and time-consuming auditing brings operations to a grinding halt.
This process includes understanding the increments, decrements, locations, and even the condition of your stored goods. These accuracy rates are typically measured based on auditing conducted by warehouse associates, which is then compared with data found in your WMS. Due to the highly manual process of inventory cycle counting, most warehouses refrain from conducting audits as much as they would like to (at the detriment of their inventory accuracy).
Inventory Tracking Accuracy and Quality Validation for Inventory “Moves”
Two other significant areas of the warehouse that require inventory accuracy are the Inbound and Order Fulfillment workflows. In an inbound verification process, items received are usually scanned to enter into the WMS database and then validated against an ASN, but there is usually no way to verify the condition of the inventory item. Similarly, unless every outgoing order is validated manually, there are multiple opportunities for the order to be:
- Wrongly fulfilled
- Damaged prior to shipment
- Shipped to the wrong customer, because the order it is at the wrong dock door or had an incorrect label applied.
Tracking inventory moves is essential to supporting fast and accurate order fulfillment
What is the Impact of Errors in Inventory Tracking?
Despite dedicating several full-time associates to perform storage cycle counting or to conduct quality audits during order fulfillment, there can still be be a multitude of errors in inventory accuracy in storage, picking, packing and shipping. These inaccuracies and errors directly impact the costs of operating the warehouse – and these can impact a Brand, a 3PL as well the manufacturers. Here below are a few examples of the costs incurred by 3PLs or Brands.
- Lost Picker Productivity: Inventory inaccuracy causes the WMS to send wrong pick instructions to pickers when fulfilling orders. So when a picker (or even a picking robot) arrives at a location to pick a product and does not find it there or finds the quantity to be inadequate, it not only causes lost productivity; it also has the potential to delay a shipment since many customers and retailers want On Time and In Full (OTIF) shipments. Inventory inaccuracy has a direct correspondence with picker productivity: If for example, a warehouse has 95% accuracy, then pickers will, on average, spend 5% of their time “looking” for items in addition to inventory clerks that assist them with the search. In a warehouse with 50 pickers, that translates to at least 3-4 people worth of “unproductive” labor.
- Inventory Shrinkage and Write-offs: The extreme case of inventory inaccuracy is when an item cannot be found and has to be written off. This problem is especially relevant in pharma or the food and beverage supply chain because items have an expiry date, and if they cannot be found within short periods of time, they have to be written off.
- Production Line Stoppages: Sometimes, a storage location is co-located with a manufacturing facility, and may be used to feed the production line with Just In Time (JIT) supplies. If the location does not have the right item, it could cause stoppages in the assembly or production line. Weekly or sometimes even daily stoppages at automotive or other heavy equipment production lines are not uncommon.
- Customer Claims and Chargebacks: Almost every day, warehouses face claims or chargebacks related to the wrong items or wrong quantities, or damaged items being received by their customers. In fact, contracts between 3PLs and their brand customers routinely provide an allowance for 0.2 – 0.5% of the annual shipment value to be “written off” by the brand for mis-shipments or damage to the inventory. As a simple example, if a warehouse makes $1B of shipments annually, that is an allowance of $2-$5M in losses annually for a single warehouse!
How to Improve Inventory Accuracy
Improving the process of inventory capture and relying on more than the “barcode” is key to driving accuracy improvements across the warehouse.
Every WMS depends on the input of inventory data from the moment goods enter the warehouse to the moment it leaves. Today, that input method is to have Associates scan barcodes on inventory or locations into a WMS. But this is woefully inadequate. With the large volume of material flowing in and out of warehouses, all forms of errors can occur:
- Labels could be missing or torn from shipments
- Associates could make errors or miss barcode scans when making entries into the database
- Products entering and leaving the warehouse can be miscounted when attempting to fulfill an order
To improve inventory tracking and reduce the number of errors, two things need to happen.
The process of capturing inventory – both in storage and moves – needs to be automated, so as to reduce the number of human touches
- It would reduce the labor requirements to validate inventory
- Reduce the number of errors while recordng inventory
- Facilitate a more frequent or even 100% verification of every inventory move, rather than just an “audit” of a small percentage of moves.
Inventory needs to be represented by much more than barcode. Today with just a barcode, there is no way to know:
1. The serial number of a product
2. The expiry date
3. Quantities inside a carton
4. The condition of an item simply by scanning a barcode
There needs to be a better way to “represent” the inventory item – which in turn will lead to more effective ways of managing inventory and reducing losses or quality related errors.
Automating the processes of inventory counting, inspections and validations has become the most reliable solution for improving accuracy and has also proven to be a more cost-effective option than unpredictable labor resources. This automation comes in the form of strategically placed and configured computer vision and sensors throughout the warehouse. These inventory tracking systems deliver THE TRUTH to a warehouse WMS in near real-time, ensuring that warehouses operate from the most accurate and up to date inventory data possible. You can now create a vision layer, or a true “digital twin”, reconciling the systematic movement of goods with their physical movement.
Greater Accuracy Across the Warehouse
Some of the industry’s top 3PLs and most well-known global brands have been using Vimaan solutions throughout their warehouses to improve accuracy at every stage.
- DockTRACK – Both large pallets and small packages are scanned as they enter and leave the warehouse. DockTRACK captures not just barcodes, but all human readable label text, counts quantities, performs dimensioning, and even inspects for damage.
- PickTRACK – as goods are put away or picked for order fulfillment using material handling equipment like forklifts, PickTRACK validates put away locations, verifies accurate order fulfillment, tracks increment and decrements of inventory at locations, and reports back to the WMS in near real-time.
- StorTRACK – Inventory auditing and cycle counting are faster, more accurate, and more frequent with the use of this versatile system. Along with dramatically improving overall accuracy, many warehouses have reported a more than 40% decrease in cycle count and auditing related labor.
- PackVIEW – Validates items at the moment of packing, reconciles against the order, and provides digital photographic archives for historical purposes and potential customer dispute resolutions.
All of these solutions provide warehouses with a more exact view of their inventory accuracy than any other practice today. Each provide the truth based on their current real-time view of warehouse inventory. These automated solutions require less headcount to operate and provide greater levels of accuracy than manual process. As a simple example, current customers are now able to cycle count more than once a week with no impact on day-to-day operations. Unlike other warehouse automation solutions that deliver ROI in years, Vimaan delivers ROI in months.
The content & opinions in this article are the author’s and do not necessarily represent the views of RoboticsTomorrow
Comments (0)
This post does not have any comments. Be the first to leave a comment below.
Featured Product
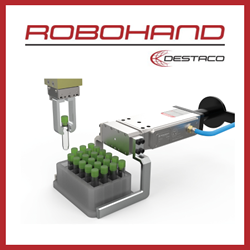