The vision system performs three key tasks: scanning in 3D the raw white vessels; analyzing the 3D scans to establish the vessels’ size, shape, position; and communicating the results to the cobot so it can accurately reach the teacups as they move along the production line.
Tazza! A 3D-Based Robot Pick-and-Place Vision System
Case Study from | Matrox Imaging
A luxury porcelain manufacturer based outside Florence, Italy has been a leader in handcrafted, elegantly designed tableware going back to the 18th century. Porcelain, otherwise referred to as fine china, it is renowned for its strength, durability, and pristine white color.
Yet, it is precisely that immaculate white color which poses numerous manufacturing challenges. For a robot arm to accurately locate raw white teacups on the production line and accurately place them in rows, a 2D vision system was not up to the task of distinguishing the different sizes, shapes, and positioning of the product. To overcome these challenges, this luxury manufacturer sought the expertise of AuTech and Fortek, two Italian companies renowned for providing automation solutions, to help develop a vision-guided robot pick-and-place system that could locate teacups randomly placed by human operators. “Seeing the manufacturing process, we thought that the only way to solve this problem was through the use of a 3D-based vision system, and we found Matrox® Imaging’s vision systems and software perfect for this purpose,” said software developer Marco Goracci, of AuTech.
Vision is our cup of tea
The 3D vision system that AuTech and Fortek designed comprises a Matrox AltiZ 3D profile sensor connected to a Matrox 4Sight EV6 vision controller running Matrox Design Assistant® X vision software. A collaborative robot (i.e., a “cobot”) from Universal Robots completes the installation. The cobot is entirely vision guided; the software directs its movements and requires no operator interaction with either the cobot arm or the vision system.
The vision system performs three key tasks: scanning in 3D the raw white vessels; analyzing the 3D scans to establish the vessels’ size, shape, and position; and communicating the results to the cobot so it can accurately reach the teacups as they move along the production line. A human operator placed the raw white teacups on the production line earlier in the process. “We needed a robust solution for a pick-and-place application. Matrox Imaging products were the best in term of ease of use, programmability, and price-to-quality ratio,” noted Goracci.
The Matrox AltiZ is connected to, and actually powered by, the Matrox 4Sight EV6 through a Gigabit Ethernet cable. The Matrox AltiZ mounted at the end of the cobot arm, moves above the vessels, performing a 3D scan of each teacup. The unique algorithms running inside the profile sensor automatically generates reliable 3D data, by smartly selecting or combining the pixel data from the two integrated image sensors, and outputting the 3D data through the GigE Vision interface.
Mounted on the cobot arm, the Matrox AltiZ 3D profile sensor provides high-resolution scans of the pristine white teacups.
Matrox Design Assistant X vision software provides easy-to-use steps for image acquisition and analysis, while also enabling users to design a graphical web-based operator view.
Rotation and positioning data from Matrox Design Assistant X software is communicated to the cobot, directing it to pick and place each teacup.
Lining it up
The manufacturer produces teacups in a wide variety of shapes, sizes, and heights. Thanks to the flexible flowchart development within Matrox Design Assistant X, the team at AuTech was able to create a single project that addressed all possible product variations. This eliminated the need to implement and switch between different recipes, and streamlined the deployment procedure. The vision system was brought online within one month with the involvement of a software engineer and a vision consultant. The major challenge concerned the variety of porcelain products to be analyzed by the application; with the help and support of Matrox Imaging’s technical support team, engineers from both AuTech and Fortek successfully fine-tuned the software analysis performed by the vision system. Implementation of the Matrox Imaging-based vision technology means a single-sourced vision system now allows the porcelain manufacturer to manage their entire production line.
“Our experience designing and deploying this project demonstrated how effective Matrox Imaging’s products are for use in a vision-guided robot pick-and-place installation. We knew that a normal 2D vision system wouldn’t suffice, and the 3D vision capabilities Matrox Imaging afforded were ideal for our needs,” said Goracci. “Our customers were very pleased with the outcome, so much so we are exploring plans to extend this application to other products they manufacture.”
Conclusion
The content & opinions in this article are the author’s and do not necessarily represent the views of RoboticsTomorrow
Comments (0)
This post does not have any comments. Be the first to leave a comment below.
Featured Product
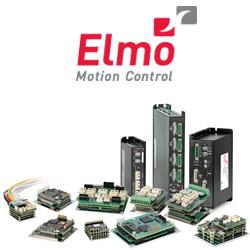