End users are looking to machine builders to provide innovative solutions that improve upon the speed and accuracy of manual-based applications while maintaining the same level of flexibility.
Improving Materials Processing With Robotics
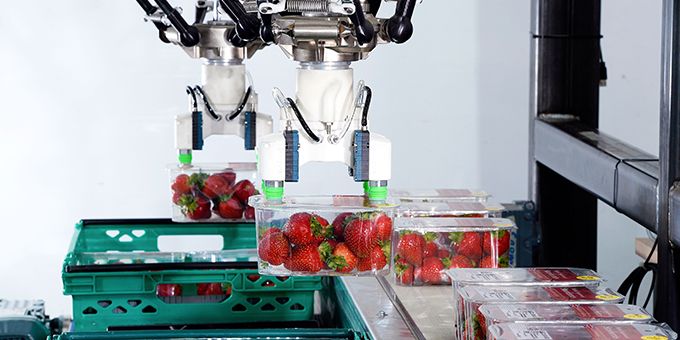
Alex Bonaire, Product Manager - Robotic | Omron Automation
Operations in industries like food and commodity, waste processing, and agriculture often involve processing and/or packaging materials at extremely fast rates. End users are looking to machine builders to provide innovative solutions that improve upon the speed and accuracy of manual-based applications while maintaining the same level of flexibility. For solutions using fixed machinery, speed and accuracy may not be as pressing an issue, but flexibility often leaves much to be desired.
Robots can readily address these concerns. That being true, many professionals in these industries hold on to beliefs that robots are difficult to use, overly expensive relative to their ROI, and unable to address complicated and/or unstructured applications. However, today’s robotic technology makes the above assertions no longer valid.
Typical challenges in pick-and-place applications
Today’s high-speed pick-and-place applications often have parts or product coming by on a conveyor belt that never stops moving. In some cases, such as is commonly the case in food and beverage packaging, there may be multiple product types that need to be packaged together into the same box in varying assortments. The configuration of these assortments may change daily depending on the number of varieties offered by the manufacturer, and new ones are often needed to adapt to market pressures.
When fixed machinery is used, the system might not adapt well to any changes to a product or assortment. Oftentimes, separate machines are required to process the full range of products, a costly strategy both in terms of financial expenses and floor space. Frequently, when a particular product configuration is being processed, the machinery used for the other varieties will lie dormant. When machinery does offer flexibility, it is typically a very complex mechanical system that has numerous failure points and requires an extended changeover period while operators swap out parts and adjust it to run the next variant.
In situations that use manual sorting instead of fixed machinery, a pick-and-place application would involve a (potentially quite large) team of people standing next to the conveyor belts, picking things off the line, and sorting them into boxes. Since this type of work is quite mind-numbing and has some potential for repetitive motion injuries, it leads to low employee satisfaction and high turnover. Given today’s labor shortage, the pressures of keeping these applications fully staffed become too high.
Robots’ flexibility, speed, and accuracy makes them ideal for fast-paced pick-and-place
The benefits of robots in and of themselves are significant by their ability to integrate seamlessly with a variety of other automation technologies. As compared with having employees perform pick-and-place tasks manually, robots have significant advantages in terms of speed, accuracy, and the ability to work round-the-clock. When a conveyor is going at high speeds, human workers may have difficulty keeping up, and may begin to make mistakes as a result.
Furthermore, the monotony of a particular task — or its unsavory aspects, such as handling dirty or otherwise unsavory material (like unwashed produce, greasy or sharp components, and even waste items) — matters little to a robot, whereas human workers would see this as a reason to start looking for a new job immediately. Many robots are also designed to be immune to harsh environments that would be quite difficult — and potentially hazardous — for people to work in. Overall, robots provide labor-related benefits such as nonstop operation, reduced labor turnover, and the reduction or elimination of work related injuries.
Robots can easily adapt to a new product design or configuration with very simple, quick programming changes. For example, once the robot system is set up, users can easily switch from one program to another with the touch of a button, and the robot automatically switches from processing variant “A” to variant “F.” When a new variant is needed, the modular process architecture of the software lets users quickly reconfigure the entire pick-and-place process without writing code or creating new programs.
Robots have unique capabilities when integrated with other automation technologies
Robots by themselves are highly flexible additions to any production line. However, when paired with other technologies, their benefits are compounded. Ultimately, robots can function as part of a fully integrated, factory-wide solution that incorporates machine vision, traceability, servo motion, and safety.
Perhaps the most obvious technology to pair with a robot is a vision system. Powerful machine vision allows robots to quickly recognize and categorize products. In tandem with pick-and place, a vision system not only enables the robot to locate a part in space (even while in motion) without the need for a fixed location, but it can also perform inspections to detect any product defects and prompt the robot to place faulty items in a discard bin.
Vision systems can also take care of traceability needs by capturing the barcodes placed on individual products and making sure that all components of an assortment are present. Additionally, in dynamic applications like those when robots need to pick from moving conveyors, vision systems can help the robot maximize its pick rate by indicating which parts are most optimally positioned to pick next.
Robots are capable of high-speed motion with very fast cycle times, but some applications have such high throughput requirements that even the fastest robot would not be able to keep up. Such applications can benefit from multiple robots working together to share the load. If a combo box-packing application is designed to have such high throughput that a single robot cannot manage all the items, a second robot can capture the items missed by the first one. More robots mean that more items can be processed in your application and strategic positioning of the robots can be implemented to optimize the pick process and/or increase flexibility. Furthermore, robots can share information between themselves to not only to ensure that all items are picked but can also balance the workload so that each robot is processing an equal number of items.
Integrate Parallel robot with the rest of the factory automation technologies and controlled altogether on a single programmable logic controller (PLC) provides several advantages. For instance, if the conveyor is controlled by the same PLC, the robots can dynamically adjust conveyor speed to adapt to product flow and/or stop the conveyor if the need arises to ensure all items are picked. If the conveyor is servo driven, its motion can be synced in real time with the robots so that these technologies dynamically adjust their own motion based on changes to throughput and with micrometer precision.
End users looking to move beyond manual or fixed-machinery solutions for high-speed pick and-place can benefit greatly from the speed, precision, and flexibility of robots, especially from robots that are designed to achieve exceptionally high speeds with high levels of stability. When integrated with other automation technologies as part of a connected factory, today’s most advanced robotic solutions can communicate directly with vision systems, conveyors, and other devices to autonomously respond to changing throughput and configuration needs.
The content & opinions in this article are the author’s and do not necessarily represent the views of RoboticsTomorrow
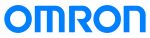
Omron Automation
Omron is an industrial automation partner that creates, sells and services fully integrated automation solutions that include robotics, sensing, motion, logic, safety, and more for manufacturers in the automotive, semiconductor, food and beverage packaging and other industries. Established in 1933, Omron helps businesses solve problems with creativity worldwide, with more than 37,000 employees serving over 110 countries. Adept Technologies is now a valued part of the Omron family.
Other Articles
Advancing Machine Design with the Power of Collaboration and AI
Preparing Your Facility for Mobile Robots: Key Considerations for Seamless Integration
Transforming Manufacturing Processes with AMRs: Boosting Efficiency and Adaptability
More about Omron Automation
Comments (0)
This post does not have any comments. Be the first to leave a comment below.
Featured Product
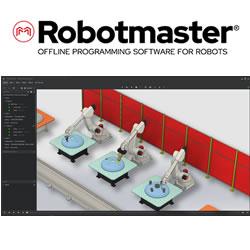