If you build machines, you probably work with actuators and positioning stages every day. But do you truly get the best performance or lowest cost of ownership from these motion devices? The answer may not be what you expect.
An Introduction To Plug-and-Play Motion Subsystems
Mike Everman, CTO, | Bell-Everman
If you build machines, you probably work with actuators and positioning stages every day. But do you truly get the best performance or lowest cost of ownership from these motion devices? The answer may not be what you expect.
All too often, engineers think of stages or actuators as just another item on the bill of materials. As long as the motion device nominally meets the desired positioning, force, payload, speed and cost requirements, it’s good to go.
With simple motion requirements, this approach to stage or actuator selection may yield acceptable results. However, machines with complex mechanical motion requirements will benefit from an embedded motion design strategy. Rather than a collection of electromechanical components, which may or may not work well together, embedded motion systems function as true plug-and-play machine subsystems.
Embedded motion systems are engineered to fit within a predefined physical space on a machine and tie into the machine’s motion control system, ready to accept commands from a top-level computer interface, control card or PLC. At their simplest, embedded motion systems may consist of little more than a stage or actuator that has been connectorized to make the drop-in installation easier. At their most complex, these motion subsystems extend from pinout to payload. They encompass not only the motion device itself but also everything it carries.
ServoBelt Rotary stages are typically used for precision positioning applications, but they are also an ideal motion platform for a novel CNC machine.
Compared to a component-by-component approach to machine movement, embedded motion offers some compelling advantages:
Mechanical Performance
Even when they use the same stage or actuator, embedded motion systems will typically outperform component-built motion systems. The reason why comes down to application and assembly expertise. A good embedded motion vendor will have years of experience solving difficult positioning problems and a collection of proven motion building blocks that can be customized for the task at hand. They will have an intimate understanding of how the stage dynamics, the motion control architecture and the operating environment will affect positioning requirements.
As for assembly, many machine builders lack the skilled technicians, specialized fixtures, laser interferometers and other metrology systems needed to align the most precise multi-axis stages—which often have axis-to-axis alignment tolerances measured in microns.
Controls Expertise
Embedded motion systems may or may not ship with motion controls, depending on the customer requirements. But a control strategy should always be part of the embedded motion equation. A good embedded motion vendor will have an extensive knowledge of how different motion control platforms and their kinematic capabilities will interact with the mechanical motion systems. This knowledge can allow us to push the envelope on what’s possible in terms of dynamic capabilities, such as acceptable inertia mismatch ratios.
Based on ServoBelt linear actuators, this multi-axis stage is assembled and fully tested as a single unit prior to integration into a larger semiconductor manufacturing machine.
Reliability
When commissioning a new motion system, some of the most common problems occur because individual, seemingly minor components fail to work properly—or fail to work properly with one another. For instance, a single faulty connector or the wrong wire can leave even the best motion stage motionless. Embedded motion systems avoid this type of failure because they are assembled and tested as a system before integration on the production machine. With motion systems composed of individual components, small failures and incompatibilities can go undetected until the production machine comes together.
Cost Reduction
Embedded motion systems typically cost 25 to 50% less than their component-based counterparts. In part, this savings comes from the ability to reduce parts count—for instance, by designing in brackets, connectors and other components. The cost reduction can skyrocket well above 50% when you factor in all the hidden cost components associated with building and installing a motion system. These include costs related to design engineering, inventory, time-to-market and more.
Many types of applications can reap the benefits of embedded motion. We have implemented this approach on dozens of semiconductor, wet bench, laser cutting, packaging and lab automation machines. The case studies that follow highlight two applications whose performance and cost requirements would have been impossible to meet without an embedded motion solution. One is a linear embedded motion system for a precision semiconductor singulation operation. The other is a rotary motion subsystem we created for a unique type of CNC machine.
Linear Stage For Semiconductor Operation
Stacked stages of any kind can suffer from alignment and control issues when you design and build them as a collection of individual axes. If that stacked stage has to meet challenging positioning accuracy or speed requirements, it’s crucial that stage function as an integrated system. We recently delivered just such a stage for a semiconductor singulation operation.
This multi-axis stage required a linear drive system versatile enough to make two very different types of moves. One was a long travel move at 400 mm/sec. The other was a short, high-speed move of 13 mm that must settle to 10 microns in 150 milliseconds. The moving mass seen by the lowest axis in the system was 38 Kg with a bi-directional accuracy goal of ± 5 microns based on the positioning reference from a 1-micron Renishaw optical linear encoder.
The Hidden Costs Of Motion Systems
Component-built motion systems have a number of hidden costs that can be eliminated by the embedded motion approach, including:
-
Time-To-Market Costs. Embedded motion systems, which inherently support concurrent engineering, can shave weeks or even months off the development time of a complex machine.
-
Program, Production and Materials Management Costs. Embedded motion systems ship as a single bill-of-materials item, eliminating hundreds of parts to be ordered, inventoried and assembled.
-
Production Costs. Precision motion systems require skilled assembly technicians and specialized production equipment that can be difficult to cost justify at less than full utilization.
-
Warranty and Failure Costs. A good embedded motion vendor will warranty their systems against failure and stand behind their work, which reduces the OEM’s risk.
The customer first tried to use an existing XY ballscrew stage design. By a wide margin, it simply failed to make the desired moves and meet the customer’s throughput requirements. It was possible, in theory, to come up with a ballscrew-based design that would meet the motion requirements. Such a design, however, would require expensive zero-backlash ballscrews and encoders that would exceed the project’s cost targets.
The customer next turned to linear motors. While capable of making the desired moves, linear motors for this application would have been large and expensive due to the long motor coil needed to meet the application’s 300 N continuous force requirements. The length of the coil would have required sweeping changes to the overall machine design. And the cost of the linear motor would have been more than 50% higher than the customer’s cost targets.
Ultimately, the customer went with an embedded motion system based on our ServoBelt Linear drives and a counterintuitive control strategy that rejected dual-loop control in favor of single-loop control using only the linear encoder.
The ServoBelt motion system beat out the more expensive linear motor by providing:
-
A zero backlash solution. The only way to achieve the fast index moves in this application was to close the servo loops using the linear encoder, which requires a true backlash-free drive line from motor to payload. ServoBelt has no backlash, which proved essential when tuning a control system that would meet the dynamic requirements.
-
Inherent damping. ServoBelt inherently offers excellent mechanical damping, which allows for very high tuning gains—typically 4 times the velocity and positional gains— which translates into extremely low settling times. Linear motors, by contrast, must simulate this damping in the servo amplifier electronics, which inherently reduces the possible positional gain.
-
A compact, plug-and-play system. The stage was designed, assembled and delivered as a single unit. We handle the crucial alignment, functional testing and burn in work. Problems are identified on our shop floor, not our customers’ machine. Designing the stage as an embedded motion system also allowed us to meet predefined physical space requirements.
Most CNC milling machines rely on linear motion components. Rotary motion, however, allows the machine to meet stringent surface finish requirements.
Rotary Motion Improves Machining Surface Finish
Three-axis CNC milling machines usually rely on linear motion systems to position the cutting tool. We went down a different path with an embedded CNC platform that we recently developed for the milling of medical ceramics.
In place of a traditional three-axis linear motion system, this new desktop-sized machine combines rotary and linear positioning devices. The rotary devices, two of our ServoBelt 100 units, face each other. One of the rotary devices carries a 150,000 RPM air-driven spindle. The other rotary holds the workpiece and can spin it 180 degrees to allow for two-sided machining. The linear axis, driven by our ServoNut actuator, allows the rotary device with the cutting heads to translate axially relative to the workpiece-holding rotary.
All three devices move in sync during machining operations. The linear axis handles the Z-axis positioning, bringing the cutting tool to the face of the workpiece. The two ServoBelts rotate relative to one another, so that the cutting tool can reach any point on the surface of the workpiece in a volume of 40x40x40 mm.
The rotary design offered important technical advantages. For one, the rotary stages exhibit an extremely high stiffness, which is crucial in order to meet the application’s machining tolerances. For another, the rotaries are lubed-for-life, saving maintenance costs and reducing the possibility of contamination. And finally, the rotary stages provided a simple sealing solution that protects the motion components from cutting fluid and flying ceramic dust. Both rotary stages extend through simple rotary seals in the wall of the cutting chamber. An XYZ motion system, by contrast, would have required less elegant sealing scenarios, such as bellows and armadillo covers.
The coordinated motion on this system required a rethinking of CNC kinematics—in large part because the rotary positioning of the cutting tool and workpiece requires the use of polar coordinates rather than Cartesian. The controller still takes in XYZ G-code commands but converts them to polar coordinates in real time, which is no easy task.
So why go through the effort? Rotary motion has an inherent advantage over linear in producing a smooth surface finish on the ceramic parts. The reason boils down to the “rumble” that even the best linear bearings and ballscrews can exhibit as the balls recirculate in and out of a loaded state between bearing grooves. This ball rumble would have reverberated through the motion system and transferred to the part as periodic variations in surface quality. With their large diameter rotary bearings, ServoBelt Rotary stages inherently avoid the ball rumble problem altogether.
This nontraditional CNC machine has all the hallmarks of an ideal embedded motion application. It required:
-
Both controls and mechanical expertise. Marrying the mechanical system with the controls and amplifiers that support the complex kinematics for polar motion required a systems approach and months of testing. We also had to develop a suite of alignment techniques and tools to build this new CNC system.
-
Compact design, easy integration. Space was at a premium on this desktop-sized CNC machine. ServoBelt Rotary’s design, which features a large unobstructed through hole, allowed us to use the available space efficiently. The 100-mm through holes made it easy to bring the air supply right to the spindle, embed a material indexer on the workpiece side and make all the required power connections.
-
Cost containment. One interesting aspect of this embedded motion system is that it is no more complex than it needs to be. The main functional requirement involved surface finish, not positioning accuracy. The positioning needs are actually quite modest, at least by our standards. So we were able to forego direct reading encoders and run the entire system in open-loop mode. That saved our customer thousands of dollars per machine.
ServoBeltTM Linear comes in two different carriage styles. The Standard carriage is more compact and uses our dual-belt drive technology. This carriage style is suitable for most applications. The LoopTrack carriage is a design in which the upper drive belt loops continuously within the carriage itself. It prevents the possibility of belt sag in inverted or cantilevered applications.
Getting Started With Embedded Motion
The jump from component-by-component motion systems to embedded motion systems may seem like a leap of faith. You will, after all, be outsourcing the motion control to a vendor.
If you pick the right vendor, though, the outsourcing will pay off with improved performance and reliability. Costs will fall too as motion subsystems arrive at your plant fully-tested, warrantied and ready to drop into your machine.
The content & opinions in this article are the author’s and do not necessarily represent the views of RoboticsTomorrow
Comments (0)
This post does not have any comments. Be the first to leave a comment below.
Featured Product
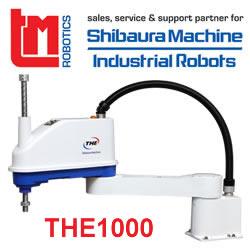