Key Factors for Ball Screw Applications
In recent years, the need for a mini ball screws has become more evident through conversations with our customers and feedback from the marketplace. Specifically, the rising demand is for high-quality ball screws that are made in the U.S and available from stock.
5 Advantages of Buying vs Making an Embedded Conveyor for OEM Applications
By outsourcing this essential component of their projects, businesses can gain a competitive edge, save valuable time, reduce costs, and benefit from the expertise of conveyor system manufacturers.
Elevating Precision Motion and Control with Magnetic Levitation to New Heights
What sets magnetic levitation apart is the ability to create a contactless, ultra-high-precision virtual bearing within our control system". Dr. Christian Rudolf provides a glimpse into the exciting development journey of PI's magnetic levitation solutions.
Designing High-ratio Drives for Precision Applications
Virtual Testing Helps Precision Gear Start-up Increase Understanding of Design Performance and Reduce Costly and Time‑intensive Physical Prototyping
Why Rotary Encoders Might Be the Best Fit for Your Industrial Robotics Design
Encoders make industrial robots accurate enough to perform positionally accurate machining and handling tasks on large components. Let's talk about how.
Optimizing Servo System Performance: A Comprehensive Guide to Eliminating Electrical Noise and Enhancing Noise Immunity
This whitepaper will delve into the steps and techniques necessary for mitigating electrical noise in servo systems, ensuring optimal performance and reliability for high-precision applications.
Drives for Speed in Intralogistics
Competitive intralogistics requires extensive automation, something that is inconceivable without micromotors. Drive systems from FAULHABER prove their ability to perform here during sorting, transporting and with robotics solutions.
ElectroCraft's MPW Wheel Drives Offer Best-in-Class Mobile Robot Solutions
If the OEM uses well-designed, proven components, the mobile platform will provide many years of service, handling cumbersome, heavy loads efficiently with minimal downtime for maintenance.
Connecting Robot Accessories to Any Industrial Network
Robots need accessories to work efficiently. But what's the easiest way to connect the accessories to factory networks? The easiest way is to use HMS Networks' ready-made Anybus products, as RSP found out.
MiniMACS6 Stabilizes the Furuta Pendulum
A classic problem in engineering is the rotational inverted pendulum. It is used to demonstrate and examine movement patterns and control algorithms in control and electrical engineering as well as in mechanical engineering. These help to control robots and other machines.
An Introduction To Plug-and-Play Motion Subsystems
If you build machines, you probably work with actuators and positioning stages every day. But do you truly get the best performance or lowest cost of ownership from these motion devices? The answer may not be what you expect.
Ways to Improve Your IMU Performance
Despite massive performance improvements, MEMS IMUs still have unique characteristics users should be aware of. By accounting for these in your system and following good IMU data practices, you can be assured the best performance for your application.
Enabling Peak Servo Performance with Thermal Protection
Motion control systems with brushless DC, voice coil or three-phase direct drive actuators use a position servo controller that dynamically changes the current in each motor phase.
Q&A with Cortona3D
Cortona3D is a well-established provider of technical documentation software. The flagship product of Cortona3D is RapidAuthor, an advanced authoring suite that enables companies to create professional and high-quality technical documentation with ease.
Mapping the Stars, Galaxies and Black Holes in the Universe, Thanks to Precision of Faulhaber Motors & Systems
Their force is transferred to the robot mechanics by means of suitable planetary gearheads. The robot mechanics used here were developed and constructed by MPS. Integrated encoders report the rotary position of the motors to the controller.
Records 1 to 15 of 63
Featured Product
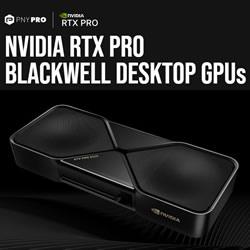
NVIDIA RTX PRO™ BLACKWELL DESKTOP GPUs
NVIDIA RTX PRO™ - Built for Professionals - NVIDIA RTX PRO Blackwell Desktop GPUs feature the latest breakthroughs in AI, ray tracing, and neural rendering technology to power the most innovative workflows in design, engineering, and beyond.