Autonomous robots can augment or replace repetitive, manual tasks so workers can focus on higher-level, strategic activities. They are also able to tirelessly perform work at all hours of the day and oftentimes at greater speeds compared to humans
Integrating Robotics and Autonomy into Industrial Environments
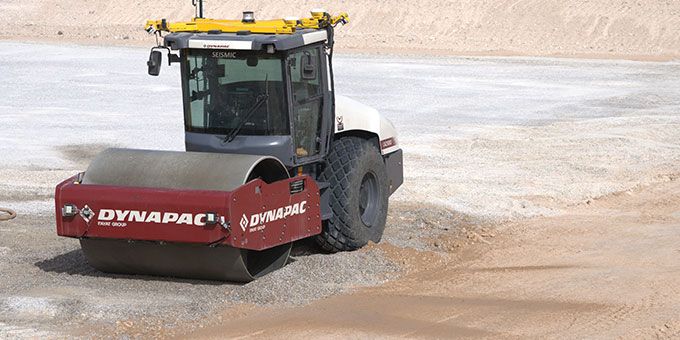
Q&A with Gordon Hain, Product Manager, | Trimble Autonomy
Tell us about yourself and your role with Trimble.
I’m a product manager in Trimble’s Autonomy business. I have undergraduate and graduate degrees in Mechatronics and have been working in and around construction and mining for quite some time. My Trimble journey started with the acquisition of Loadrite when I was the product manager for excavator payload measurement systems. In 2016, I left Trimble and spent several years working with GNSS Aided Inertial Navigation Systems working alongside companies exploring the depths of the ocean to the edge of the atmosphere. In 2022, I returned to Trimble in my current role assisting with the autonomous compactor project and other autonomy related products.
Outside of work, you’ll most likely find me on the side of a soccer field or in a Brazilian Jiu-Jitsu gym with one of my kids.
How are autonomous robotic solutions being integrated into today's industrial environments?
Over the past decade, and more in some applications, we’ve seen significant growth in the use of autonomy and robotics solutions in industries such as agriculture, construction, mining and manufacturing. These are industries with high volume workflows, where productivity and efficiency are key to profitability. They also often involve repetitive tasks that can be monotonous, dangerous, dirty and time consuming. Autonomous robotic solutions offer significant benefits that enable the transformation of traditional workflows.
As an example, agricultural operations are benefiting from autonomous farming equipment such as self-driving tractors, harvesters, planters and sprayers. Coupling these autonomous machines with advanced coverage planning software solutions to optimize field coverage and machine movement increases efficiency, reduces labor requirements and increases yield. Other solutions such as robotic crop monitoring and drone technology enable farmers to monitor soil, crop and weather conditions in near real-time, arming them with the information to make time-critical decisions and efficient resource management.
In mining applications technology such autonomous haulage systems, remote operations centers and robotic drilling are just some of the solutions that:
- improve safety for site personnel,
- increase machine utilization, precision and efficiency,
- reduce operational cost and improve productivity
Autonomous robotic technology is helping these and other industries better understand and optimize workflows, increase efficiency, utilization and productivity while also keeping their employees safer.
What parts of these industries will be most impacted by robotics?
The use of autonomous robots is helping to increase productivity and safety, reduce operational costs and also to address the skilled labor shortage plaguing many of these industries.
Autonomous robots can augment or replace repetitive, manual tasks so workers can focus on higher-level, strategic activities. They are also able to tirelessly perform work at all hours of the day and oftentimes at greater speeds compared to humans, thereby increasing efficiency. This helps optimize workflows across an entire site while also providing data insights from the field into back office systems.
From a safety perspective, autonomous robots can be used to perform more dangerous tasks or work in hazardous environments, reducing the risk of injuries and accidents. Remote operation centers where operators control autonomous machines from a central location is an approach to improve site safety by removing operators from hazardous environments while maximizing equipment utilization and efficiency. The autonomous machines are also equipped with sensors to determine if there is an obstacle in the way they need to avoid or if they are getting off track from their predetermined route. The perception sensors can also provide operators with a 360 degree view of the surrounding environment delivering another layer of situational awareness and site safety.
Operational costs can be driven down using practices such as precision agriculture. Precise positioning with additional sensors such as cameras used in activities like seeding, fertilizing, and spraying enable autonomous robots to precisely apply inputs based on real-time data, optimizing resource utilization and improving crop health.
As older generations retire and younger generations opt for other career paths, autonomous robots can help solve some of the current labor shortage. They can also be used to help train the next generation workforce, introducing autonomy incrementally and slowly increasing the abilities of the machine and thereby upskilling the operator.
Where do you see the biggest opportunity to improve applications / workflows using robotics and big data?
At a basic level, moving a machine from point A to point B is one aspect, but a machine or robot is really there to perform a task, so optimizing the task and workflow is key. For example in agriculture, farmers get one opportunity for a harvest, so any miscalculation or wrong decision could jeopardize their crop. Having a fleet of solutions automated to the highest level is a big driver for advancing these solutions and end users are demanding it. The better autonomous and robotic technology becomes, the better visibility into your daily operations and data you can collect over time can help you make more informed decisions.
Autonomous vehicles equipped with sensors and imaging technologies can collect real-time data on crop health, soil conditions, weather patterns, and other relevant factors. This data can be combined with historical data and analyzed using AI and big data analytics to generate insights and make data-driven decisions. Precision farming enables targeted interventions such as precise irrigation, fertilization, and pest control, leading to optimized resource utilization and increased crop yield.
Another benefit to using this technology is sustainability, which has become a big focus especially in industrial environments where there is immense pressure to reduce their carbon footprint. Autonomy enables this by optimizing your inputs, so for example, farmers could use less fertilizer and chemicals which means less toxic materials flowing into streams. It can also create optimized paths for tractors that reduces the impact on fuel consumption and wear and tear on machines, leading to improved machine life. They can also consistently execute operations with minimal errors, reducing defects and waste.
What are the biggest challenges to integrating autonomy in applications and workflows?
While many people are excited about the potential of autonomous solutions, there are several challenges that impact the greater adoption:
-
Technological complexity, oftentimes interoperability can be a barrier to entry. There are many different technologies such as actuators, compute platforms, AI, sensors, etc. that enable autonomous robots and machines to work and if they are not compatible with one another, they cannot be fully optimized.
-
Adaptation to dynamic environments: Construction and agricultural environments are dynamic with varying conditions, terrain, and weather. Building autonomous solutions that can adapt to these changes and operate effectively is a challenge.
-
Safety and liability concerns: Autonomous systems must be able to operate safely, avoiding collisions with humans, animals, or other objects. Ensuring the reliability and robustness of these systems is crucial to preventing accidents or damage. Liability issues also arise when autonomous systems are involved in incidents, leading to questions of responsibility and accountability.
-
Regulator and Legal frameworks: Existing regulations and standards may not specifically address autonomous technologies, creating uncertainties in terms of compliance and liability. There are several initiatives to establish appropriate frameworks and guidelines to ensure safety, privacy, and ethical use of autonomous systems, but this is a complex and time-consuming task.
-
Upfront cost and return on investment: The implementation of autonomous systems typically involves significant upfront cost. Hence mining has been one of the earliest adopters of autonomous technology due to the significant capital and operation cost of the equipment utilized. Showing an effective return on investment and demonstrating the long-term benefits of autonomy becomes crucial for wider adoption.
-
Workforce acceptance and integration: While there is an awareness of the benefits, operators and workers need to see it in action and understand how it works within their day-to-day workflows. They may be resistant to change and feel the way they have been doing it for years is still the best approach.
Do you have an example you can share with us?
In the construction industry, autonomy is being used in the bid-to-build process to provide better visibility into daily operations. With small margins, construction business owners are focused on where they can make incremental gains. With autonomous robotics, this progression can move from operator assist all the way through to gaining back office visibility into what is happening day-to-day to make more informed decisions.
In the agriculture industry, the overall goal is to have a more consistent product and to operate at peak performance. When applications need to be run in the field, operators are often on a time crunch due to the time of day, weather, etc. Autonomous robots and machines can operate any time of day or night, keeping operations on track and with consistent quality.
Will robots replace the jobs of current employees?
No. Autonomous robotic technology actually helps upskill operators and workers. It is not about removing the operator but, instead, elevating them to focus on more important things. It can actually be a force multiplier that can help you go from running one machine at a time to running two to three.
What does the future hold for robotics and big data?
There is a tremendous opportunity to add value through data collection and analysis. These autonomous robots and machines collect data that can be analyzed and used for predictive purposes and to make incremental productivity gains based on data.
Autonomous technology is still in its infancy. Robotics and big data will continue to evolve, and as people get more comfortable with the technology and see the value first hand, it will grow exponentially in the future.
The content & opinions in this article are the author’s and do not necessarily represent the views of RoboticsTomorrow
Comments (0)
This post does not have any comments. Be the first to leave a comment below.
Featured Product
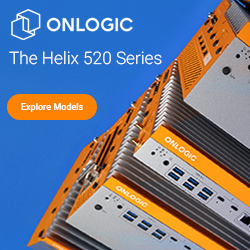