Mid-South Automation’s team was challenged to find a cost-effective way to make a 34 station modular system, making each module (or section) self-powered.
Case Study: Glide-Line’s Zero Contact Zoned Conveyor For Integrator, Mid-South Industrial Automation
Case Study from | Glide-Line
Mid-South Industrial Automation, an integrator of specialized process equipment, designs and provides cost-effective automation solutions to their manufacturing clients. Mid-South has the ability to work with any conveyor manufacturer able to help them accomplish their clients’ goals on capabilities, price, throughput, and space; they want the most value for their dollar. Their applications and design engineers apply their knowledge of process and assembly design to any industry requiring specialized equipment.
They’ve partnered with Glide-Line recently for clients who require flexible, innovative solutions in automated conveyor systems. Glide-Line manufactures and builds conveyors to fit systems like those designed by Mid-South Automation, and frequently provides creative solutions alongside integrator engineers to solve challenging process requirements.
The Challenge
Mid-South Automation’s client had approved the design of the conveyor line. It was designed to assemble a small electrical component for vehicles. Mid-South Automation’s team was challenged to find a cost-effective way to make a 34 station modular system, making each module (or section) self-powered. Their client’s goal is to be able to add or subtract sections of the line in the future. Mid-South Automation designed the conveyor in a U-shape since floor space was available only at a premium. They needed to provide access to the inside of the U-shaped line, and also needed to convey the pallets back to the beginning of the line once they had reached the end. They had looked at other pallet-type conveyor manufacturers, but ultimately looked into Glide-Line at the specific request of their customer to:
-
Find cost-effective solution
-
Individually power each conveyor section
-
Add/subtract conveyor sections modularly
Why Glide-Line
Jason Flynn, applications engineer and account manager at MidSouth Industrial Automation, gave us insights into today’s integrator customers. “Today things are at a faster pace than they were 10 or 15 years ago,” Jason said. “The customer is now designing the product at the same time they’re kicking off equipment. Because of this, the lead time we have to get equipment built is shorter. Sometimes, there are also more iterations because as the customer finds issues or needs to tweak or change their product, that can affect their equipment design.” Glide-Line has built its business on quickly creating standard custom solutions for applications engineers like Jason to integrate in today’s rapidly evolving manufacturing market. Jason notes, “Glide-Line was able to customize our solution to our customer’s needs. One of the things we really like about Glide-Line is they were able to customize our solution better and faster than other pallet-type conveyor suppliers.” Customization. Flexibility. Speed. For these three reasons, MidSouth Automation chose Glide-Line for their customer’s conveyor automation system.
“One of the things we really like about Glide-Line is they were able to customize our solution better and faster than other pallet-type conveyor suppliers.”
- Jason Flynn, applications engineer and account manager at Mid-South Industrial Automation
Solution from Glide-Line
Using Glide-Line’s in-context configurator software, IMPACT!, MidSouth’s team was able to design their ideal conveyor automation system and know the price for their system immediately. This was invaluable during the design and quoting phase. Its ease of use was a huge timesaver for Mid-South, adds Jason. “It was a big deal to be able to access what they needed in a short amount of time, and to have that come into SOLIDWORKS in native format, and then be able to configure it and make further changes.”
“It was a big deal to be able to access what they needed in a short amount of time, and to have that come into SOLIDWORKS in native format, and then be able to configure it and make further changes.”
- Jason Flynn, Mid-South Industrial Automation
To meet the client’s needs, Mid-South used vertical lift and transfer units and Glide-Line’s Zero Contact Zoned Conveyor. “Glide-Line had a cost-effective way to individually power the sections of conveyor, which is the exact customized solution our customer needed,” Jason said. This highly configurable lift and transfer pallet conveyor uses individual DC-powered motors for each section of the conveyor.
In the final design, a pallet makes its way around the U-shaped conveyor line, then lifts up three meters in the air along another conveyor, then back down to the beginning. It is a bridge for the pallets to go over. This both saved space for the client’s process and provided access to the center of the U shape. This enabled operator access and space for tow-motors and for other components being delivered inside the line.
Results
“Glide-Line had a cost-effective way to individually power the sections of conveyor, which is the exact customized solution our customer needed.”
- Jason Flynn, Mid-South Industrial Automation
Mid-South Industrial Automation used the Glide-Line Zero Contact Zoned Conveyor for each of the their client’s conveyor’s individually-powered 34 sections, which meant they could add or remove sections as needed.
Pricing
Glide-Line comes in at a very competitive price point. This helped Mid-South keep its promise of costeffectiveness to their customers. IMPACT! also provides an incredibly accurate quote quickly, which limits changes to pricing down the road.
Superior Options
Choosing Glide-Line instead of common competitors, Mid-South got a comparable product that was more flexible, easier to use, had faster lead time, and even better pricing. With a different manufacturer, Jason adds, “The cost would have been higher. The vertical lift unit we had to use would have been more difficult. Other conveyor manufacturers’ motors are a lot larger, and for the individual motorized sections, the Glide-Line solution is cleaner, smaller, and more streamlined. The pancake motor from Glide-Line provided better equipment accessibility.”
-
Mid-South selected a Glide-Line Zero Contact Zoned Conveyor to overcome their client’s challenging process.
-
They used IMPACT! to design and quote the project with accuracy.
-
The final design was unique and saved space while remaining cost effective.
Assembly & Corrective Measures
Glide-Line’s conveyors, once delivered to the customer, went together quickly and were easy to set up. Mid-South’s team appreciated the additional space savings available from the easily accessible maintenance areas. For example, the conveyors can be placed close together and require minimal clearance to change the belt. And when issues came up, as in any project, “Glide-Line quickly replaced the parts; their customer service is really good,” Jason said.
“The Glide-Line solution is cleaner, smaller, and more streamlined.”
- Jason Flynn, Mid-South Industrial Automation
About Glide-Line
Glide-Line offers the most versatile multi-strand pallet and panel-handling solution available for the assembly automation industry. We are the future of conveyor system manufacturing. We pride ourselves on making our integrator clients’ automation layout design process as easy as possible. “Glide-Line is based on innovation, excellent customer service, high quality and real speed,” said Kevin Mauger, President of Glide-Line. For more information on the Glide-Line Zero Contact Zoned Conveyor and other solutions, visit glide-line.com.
The content & opinions in this article are the author’s and do not necessarily represent the views of RoboticsTomorrow
Comments (0)
This post does not have any comments. Be the first to leave a comment below.
Featured Product
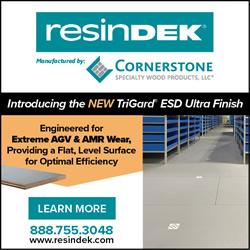