Fiber optics transmit data as pulses of light through strands of fiber made of glass or plastic. When bundled with hundreds of other strands, the resulting fiber optic cable will transmit more data at faster speeds and over longer distances than high-grade copper cables.
CoaXPress over Fiber
Q&A with Donal Waide, Director of Sales | BitFlow, Inc.
What is CoaXPress over Fiber?
The latest version of the CoaXPress interface (Revision 2.1) features an add-on designed to let the CoaXPress protocol run unmodified over a standard Ethernet connection, including fiber optics. This add-on is dubbed “CoaXPress over Fiber” (CoF). Basically, it takes virtually all the advantages of CoaXPress and combines them with the performance benefits of fiber optic cabling.
The key to CoF is that it uses Ethernet Layer 1; that is, the layer where data is physically moved across a network interface. Layer 1 technologies are at the very lowest level of a network. As such, it is responsible for the encoding and signaling functions that transform data from bits that reside within a device into signals that can be transmitted over the network.
Importantly, Layer 1 defines hardware specifications, such as cables, connectors, and network interface cards. Therefore, whenever an upgrade comes to a Layer 1 component, it will directly benefit CoF, whether that upgrade translates into more bandwidth or lower prices. Compared with machine vision, Ethernet-based computer networking has huge sales volumes, which has driven its component prices down. These more economical components, such as cables and connectors, can lower the overall price of a CoF vision system.
What are the data rates supported by a CoF system?
CoF’s net bandwidth is the same as CXP-12—approximately 40 Gbps. However, instead of requiring four CXP-12 links and four coaxial connections to achieve this, CoF transmits 40 Gbps on a single QSFP+ (Quad Small Form Factor Pluggable) transceiver module and a single fiber optic cable.
By comparison, USB3 Vision has data rates up to 5.0 Gbps, and Camera Link has data rates up to 6.8 Gbps
What is the benefit of having Fiber in machine vision solutions?
Fiber optics transmit data as pulses of light through strands of fiber made of glass or plastic. When bundled with hundreds of other strands, the resulting fiber optic cable will transmit more data at faster speeds and over much longer distances than high-grade copper cables. Also, fiber optics are electrically isolated. Accordingly, it does not radiate, and it is not susceptible to electromagnetic interference (EMI) that can slow transmission speeds or create crosstalk. Fiber optic cable isolation eliminates problems associated with grounding as well.
From the installer’s perspective, fiber optic cables offer several advantages. For one, fiber optic cables do not represent a fire hazard as heat is not dissipated. Second, the cables can withstand significant pull forces without suffering breakage over long runs compared to copper cabling. Third, fiber optic cables are not damaged by inclement weather, moisture, or temperature extremes to the same extent as coaxial or Ethernet cables. Finally, being lighter and smaller in diameter than other cable types, fiber optic cables can be easily threaded on machines, robots, aircraft, and ground vehicles.
How easy is it to upgrade my existing CXP solution to a CoF solution?
As an extension of the CoaXPress protocol, CoF provides the generic Gen|Cam programming interface for hardware and software, plus is independent of any operating system, making it simple to upgrade from coaxial to fiber optics. Upgrading will require CoF-compliant cameras and frame grabbers, as well as fiber optic cabling, transceivers, and connectors.
A CoF frame grabber will have a fiber transceiver slot supporting QFSP+ compatible fiber cable assemblies. The assembly will provide up to four connections to support one quad link camera, two dual link cameras, or four single link cameras. CoF frame grabbers use the same half-Size x8 PCI Express Gen 3.0 platform as CXP frame grabbers, making it simple to swap out in the host PC. The optical transceiver module consists of a receiving end and a transmitting end. The receiving part realizes a photoelectric conversion, and the transmitting part realizes an electro-optical conversion.
A single fiber optic cable can achieve speeds of 40 Gbps. This means that fewer cables are required to transmit data, reducing the complexity of the cable run, lowering system costs, and minimizing potential failure points, especially if fiber extenders were previously required.
What are the use cases for CoF?
The first applications to take advantage of CoF have been in situations requiring exceptionally long cabling such as Intelligent Transportation Systems or ballistics testing, or when electrical isolation is required between the camera and the PC as is the case in noisy industrial sites and sensitive medical environments.
In addition, as mentioned, economics will play a role in the pace at which CoF is adopted. CoF has cost benefits over traditional coax because of its ability to use Ethernet networking components, especially as this applies to cable costs. For example, a 30M quad CXP-12 coaxial cable costs over $600, while a 30M QSFP+ AOC (Active optical cable) costs about $125. Combined with its other advantages, this cost effectiveness might be enough to convince system integrators to migrate to CoF.
The content & opinions in this article are the author’s and do not necessarily represent the views of RoboticsTomorrow
Comments (0)
This post does not have any comments. Be the first to leave a comment below.
Featured Product
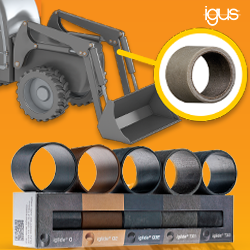