The Deus Robotics’ all-in-one warehouse automation solution offers AI-powered robots and an AI brain to manage any type of warehouse robots from a single platform."
The Robot Driven Logistics Industry
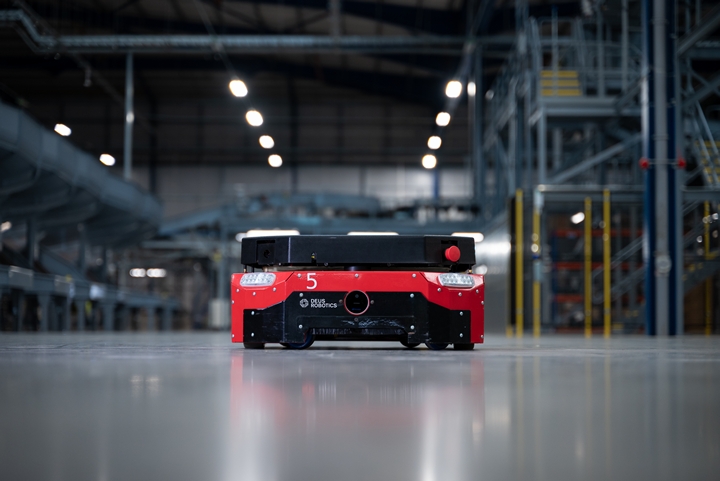
Q&A with Pavlo Pikulin,Founder and CEO | Deus Robotics
Tell us about yourself and why you decided to found a robotics company?
It all began with my dad, a huge tech enthusiast, who bought me a computer before I was born. In 1989, having a personal computer was rare in my hometown, so it was a big deal.
I wrote my first computer program at age five. At seven, I sold my first website for $20 and moved on to building and selling computers. At thirteen, I created a program to bypass captchas in games. This later became an automatic number-plate recognition solution.
By fifteen, I knew the future would be robot-driven. This solidified my goal to work in robotics and AI.
But there was one small hiccup. At that age, I lacked the resources to start a robotics company myself. So, at nineteen, I launched a game studio. It went great! We skyrocketed from 2 to 700 employees in several years. Now, the company has over 60 million users worldwide, while our games topped download charts in the US.
Meanwhile, I kept thinking about robotics. I always believed robots could make the world a better place, a belief only a few people in my life shared. But I just knew robots could handle physically hard, mundane, or dangerous tasks for us. This would free us, humans, to do more rewarding work. Well, to do anything we want.
By late 2018, I accumulated enough money to start my own robotics company. I did some research and started Deus Robotics in 2019.
What makes Deus Robotics different from other warehouse robotics companies?
Unlike other warehouse robotics companies, we've created the most crucial part of robots. It's their brain. This AI-powered brain can connect with robots from any manufacturer, including ours. It’s a unique capability in the industry.
This interoperability is essential. Warehouses need various types of robots for different tasks, often from multiple manufacturers. Managing these robots centrally is challenging since they can't synchronize. This also makes scaling automation impossible.
That's where our solution can help. Warehouses can use it to optimally operate as many robots as needed through a single system.
What’s more, ours is an all-in-one solution containing two key ingredients. These are the robots addressing 90% of logistics use cases (and counting) and the AI platform to manage them.
Do you agree with the statement: “Robotic automation will add more work to my plate”? Why/why not?
I think it would be right to define two groups of people working in warehouses.
The first one is warehouse operators. They are directly involved in transporting goods. For them, robotic automation significantly reduces physically demanding, monotonous, and often gruelling work. In fact, some people think that “automation and robotization might be necessary to save the cost to human physical and mental health”. It’s so spot on. Enhanced by robots, warehouse operators no longer need to walk 10 kilometers daily. Instead, robots bring the goods to them.
Additionally, warehouse operators enhance their warehouse expertise with robot operations skills. This way, they can get higher salaries while doing less physical work.
As for warehouse leaders, they can do more with less. It’s no secret that, in the warehouse industry, people massively leave their jobs. For example, the employee turnover rate reached 49% in the US in 2022. People leaving means constant hiring and training, which is very time-consuming and costly. With robots, warehouse leaders can maintain the same throughput with even fewer employees. Plus, robots need to get onboarded only once and never quit. And they can work as long as you need them to.
Why is connectivity important in warehouse robotic automation?
My short answer is: No more compromises!
Usually, robots from a single manufacturer cover only a portion of a warehouse's automation needs. This means warehouse leaders have no choice but to partner with several manufacturers to cover all their needs. But here’s the catch. Robots from different manufacturers cannot synchronize in one warehouse zone because different systems operate them. For example, if you need to transport a shelf and then pick items from it, you can’t do it efficiently. Usually, you need two robots from different manufacturers for this.
So, warehouse leaders are forced to compromise. They have no choice but to choose what processes to automate. Correction: Had no choice. Because that’s exactly where our solution jumps in. It is a single system that integrates seamlessly with any robot, including ours, and maximizes efficiency. Warehouses need to integrate with our system just once. After that, we take care of integrating with (or replacing) and centrally managing any number of warehouse robots now and in the future.
How can warehouse leaders know when to start using robots for automation?
1,000 operations per day is the minimum threshold that justifies robotic automation.
However, there is a more complex approach.
First, you need to assess how many different types of operations occur in the warehouse. Second, you should identify the operation involving the most personnel. Third, you need to calculate the return on investment for automating this process. This can vary, as robots are more efficient in warehouses operating 24/7. For such warehouses, the quantity of goods required for automation is lower. The reason for this is that robots can work non-stop.
No worries, though. Your provider should be able to calculate the robotic automation ROI easily.
What are some of the biggest hurdles warehouse leaders face in implementing robots for automation and how can these be overcome?
From what I’ve seen, the biggest challenge is figuring out how to use robots with maximum efficiency. At Deus Robotics, we use a three-step process to find the right approach:
-
First, we create a digital twin of the warehouse. It emulates all processes including people, robots, and goods.
-
Secondly, our specialists suggest various robotic automation strategies based on the client’s needs.
-
Thirdly, we test these strategies for a month to find the optimal solution.
The second challenge is integrating the warehouse and robot management systems. This process always takes time. Especially when you have two or three different robot management systems. It's also hard when you need to switch from one robot manufacturer to another. In this case, you have to go through the entire integration process again. This is expensive and takes at least six months. Usually, no one does that as it’s too difficult. Instead, warehouse leaders opt for just one robot manufacturer.
The third challenge is training personnel. The remedy here is regular workshops and training sessions. You should also enforce safety protocols.
How do you envision the future of the robot-driven logistics industry?
I believe that with the adoption of robotics, the cost per operation will decrease. This will provide a significant boost to the logistics industry. We will also see a growing number of robot-driven warehouses which will be easier to scale. Setting up such a warehouse will take just a week.
Warehouse logistics will integrate with external robotic logistics. This will include delivery via autonomous trucks, vehicles, robots, and drones. The entire journey of a product or package, from manufacturer to recipient, will become fully automated.
So, in a nutshell, robots will make our future so much better.
The content & opinions in this article are the author’s and do not necessarily represent the views of RoboticsTomorrow
Comments (0)
This post does not have any comments. Be the first to leave a comment below.
Featured Product
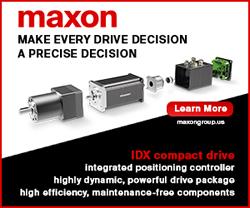