ZF, a global technology company from Germany, uses the MIRAI AI-vision software to automate a challenging pick-and-place task.
ZF Pick and place
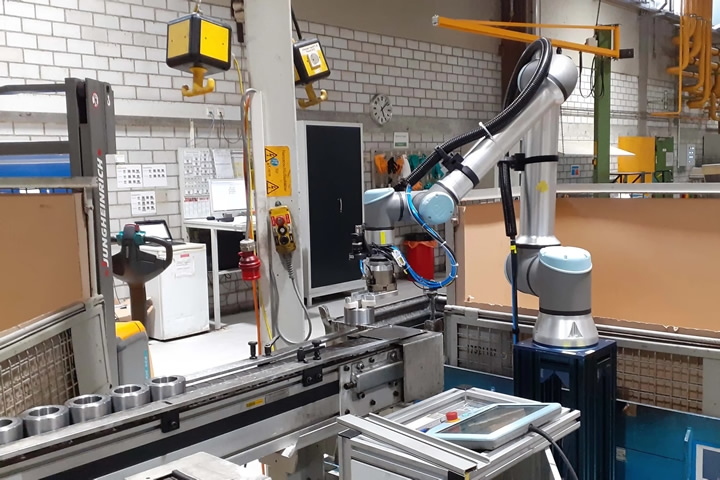
Case Study from | Micropsi Industries
Challenge
ZF wanted to automate the process of picking metal rings from a crate and placing them on a conveyor belt. Variance in the position and appearance of the rings, among other complexities, made automating this task with conventional automation solutions unreliable.
Outcome
ZF partnered with Micropsi Industries to train a MIRAI-powered robot to perform the task, overcoming variance in position, appearance, and lighting. The MIRAI system performs the tasks significantly faster and more reliably than conventional solutions.
At its headquarters in Friedrichshafen, Germany, ZF, a global supplier of automotive and industrial solutions, wanted to automate machine tending at a high-volume milling station where gears are manufactured. The process involves picking metal rings from a crate and placing them on a conveyor belt. The metal rings are the raw parts that will become gears in subsequent manufacturing steps. The pick-and-place task presents several challenges:
The rings in the crate shift during transportation, making their positions unpredictable.
The position of the crate, once delivered and facing the robot, can vary 20–30 mm in all directions.
The form of the crate can vary. Sometimes its sides are not straight. They can be pressed inward, with a deviation of 20–30 mm.
In the spring and autumn, the workspace gets direct sunlight. Although a crate’s inside walls are covered with carton paper, one-third of the rings are still directly exposed to sunlight.
Bubble foil on the inside of the crate covers some parts of the rings.
The surface of the rings can have oil and rust. This creates variance in their visual representation from the robot’s perspective.
The variance in the process made automation with standard solutions unviable.
Reliable automation 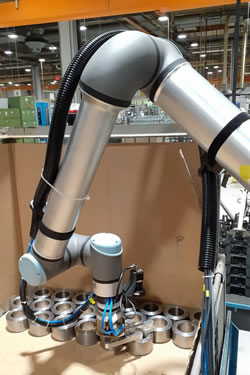
ZF partnered with Micropsi Industries to train a MIRAI-powered robot to successfully complete the task. Today, a robot from Universal Robots performs the pick-and-place task, overcoming the variance in the position of the crate and rings and the different appearance of the rings thanks to MIRAI. Even changing lighting conditions do not affect the system's performance.
During the process, the metal rings in the crate arrive in layered beds, with the workpieces lying close together on their flat sides. Using its native controller, the UR robot has been programmed to move over individual rings in the crate. Once the robot is over a ring, the MIRAI system takes control: it moves the robot to the next ring and brings the gripper into gripping position. Once this position is reached, the robot's native system regains control; the robot picks up the ring, moves it to the conveyor, and places it on the conveyor. Training the MIRAI-powered robot to perform its part of the solution process took only four days. The MIRAI system performs the tasks much faster and more reliably than conventional solutions.
The content & opinions in this article are the author’s and do not necessarily represent the views of RoboticsTomorrow
Comments (0)
This post does not have any comments. Be the first to leave a comment below.
Featured Product
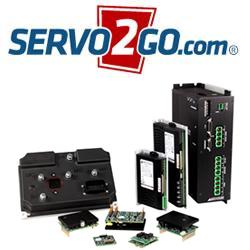