Smart manufacturers run highly productive operations by focusing on efficiency and increasing uptime. Doing this means implementing strategies to educate robot operators as much as possible on topics such as inspection, parts and service, preventive maintenance and more.
5 Ways to Prevent Robotic Automation Downtime
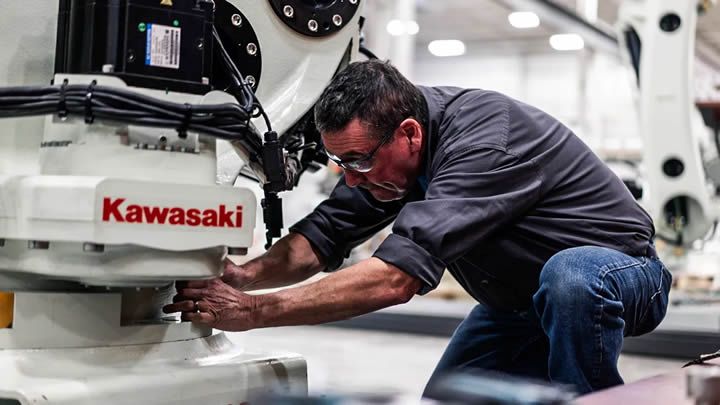
Mike Dawson, Service and Operations Manager | Kawasaki Robotics
Smart manufacturers run highly productive operations by focusing on efficiency and increasing uptime. For their robotic automation departments, successfully doing this means implementing strategies to educate robot operators as much as possible on topics such as inspection, parts and service, preventive maintenance, programming and more. By following these five simple suggestions from Kawasaki Robotics, minimizing robotic automation downtime is attainable for any size facility.
1. Understand the maintenance manual
It sounds obvious, but having a maintenancemanual on hand is helpful on several levels. Not only does it provide a quick glance at the maintenance, parts and service for a product line in order to educate operators, but it helps them make decisions about choosing proper maintenance procedures. For example, it calls out the specific preventive maintenance timing, grease replacement information, belt tension, vibration checks and other maintenance items. Maintenance manuals are available for free via download on the Kawasaki Robotics website, or one can be ordered through our 24-hour hotline.
2. Utilize tools to predict maintenance cycles
Scheduling regular preventive maintenance saves time and operating costs by avoiding more time-consuming and expensive repairs that occur as a result of fixing broken equipment instead of focusing on prevention. Kawasaki Robotics offers three PM options for customers:
- Scheduling on a 5,000-hour cycle. This PM cycle commonly equates to an annual or biannual service, depending on the robot usage. It is the most economical and easiest option.
- Grease analysis. This method consists of testing a grease sample from robot joints on equipment that measures metal particulates in the sample. The analysis enables the robot provider to determine whether to increase the PM cycle based on the amount of metal present in the lubricant.
- Failure prediction software. Kawasaki Robotics’ TREND Manager automatically and continuously analyzes status data from a robot to detect signs of wear, predict impending malfunctions and the need for inspection—without even inspecting the robot. The external PC-based software can read up to 20 robots’ feedback data while the equipment runs. It logs fault codes, peak current, brake voltage and more. Then, the data can be combined with robot backup data to generate highly accurate information. Overall equipment efficiency (OEE) can also be determined.
If you use Kawasaki robots and need to start or adjust your PM program, get in touch with your representative to make the change.
3. Be observant
Operators of the robot cells and the machines where robots are integrated should do regular walk-throughs as they begin daily production. If unusual noises or other abnormal symptoms are detected and cannot be diagnosed by the operator, Kawasaki Robotics is available 24/7 for service calls. A quick call can avert a catastrophic failure, preventing unnecessary downtime and expense.
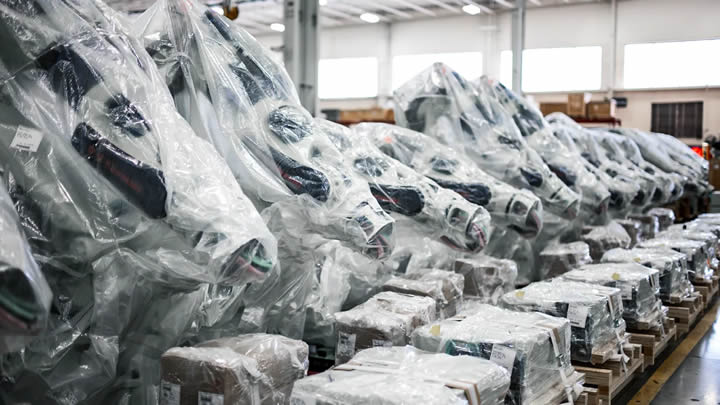
4. Stock spare parts
Being prepared for maintenance by stocking spare parts in-house can drastically decrease automation downtime. When a part must be ordered, it might take a day or longer to have it shipped. By having the part readily available, remote support can quickly help with a repair or replacement.
5. Hire a skilled programmer
Programming that has not been optimized is a common problem and one that causes inefficiency. A skilled programmer on staff who is comfortable creating a fluid program not only ensures a smoothly operating robot, but also extends its life cycle and lowers operating costs.
The content & opinions in this article are the author’s and do not necessarily represent the views of RoboticsTomorrow
Comments (0)
This post does not have any comments. Be the first to leave a comment below.
Featured Product
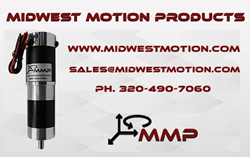