Pixus Technologies Announces New Overview Brochures
Pixus Technologies, a provider of embedded computing and enclosure solutions, has released a new overview brochure that highlights the companies capabilities and core product lines.
Pixus Technologies, a provider of embedded computing and enclosure solutions, has released a new overview brochure that highlights the companies capabilities and core product lines.
The new Pixus overview brochure features a brief history of the company, details on the 4 main product lines, and notes on its customization, ruggedization, and simulation/analysis capabilities. The main product lines includes Chassis Platforms, Backplanes, Instrumentation Cases, and Components. As OpenVPX is a core product line for the company, the architecture is the primary focus of the brochure. Other standards included are cPCI Serial, AdvancedTCA, MicroTCA, and legacy VME/64x and CompactPCI.
The brochure will be posted on the companies literature page at http://www.pixustechnologies.com/about-pixus-technologies/literature. For more information on Pixus products and services, contact the company at info@pixustechnologies.com or call one of the local offices listed on the Web site.
About Pixus Technologies
Leveraging over 25 years of innovative standard products, the Pixus team is comprised of industry experts in electronics packaging. Founded in 2009 by senior management from Kaparel Corporation, a Rittal company, Pixus Technologies' embedded backplanes and systems are focused primarily on ATCA, OpenVPX, MicroTCA, and custom designs. Pixus also has an extensive offering of VME-based and cPCI-based solutions. In May 2011, Pixus Technologies became the sole authorized North and South American supplier of the electronic packaging products previously offered by Kaparel Corporation and Rittal.
Featured Product
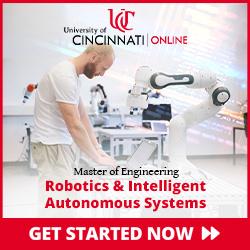
Online Master of Engineering in Robotics & Intelligent Autonomous Systems
The Robotics and Intelligent Autonomous Systems program at the University of Cincinnati Online offers a cutting-edge curriculum that equips students with the skills to design, develop, and implement advanced robotic systems. Through a combination of theoretical knowledge and top-ranked faculty, students gain expertise in artificial intelligence, machine learning, and robotics, preparing them for impactful careers in the rapidly evolving field of autonomous systems. Explore now!