By partnering with Roboworld since their first Cobot rolled off the line on Day 1, all of Vectis’ robotic welding systems and teach pendants have included Robosuits® and Pendant Armor®.
A Cut Above: Adding Next-level Protection for Next-generation Welding
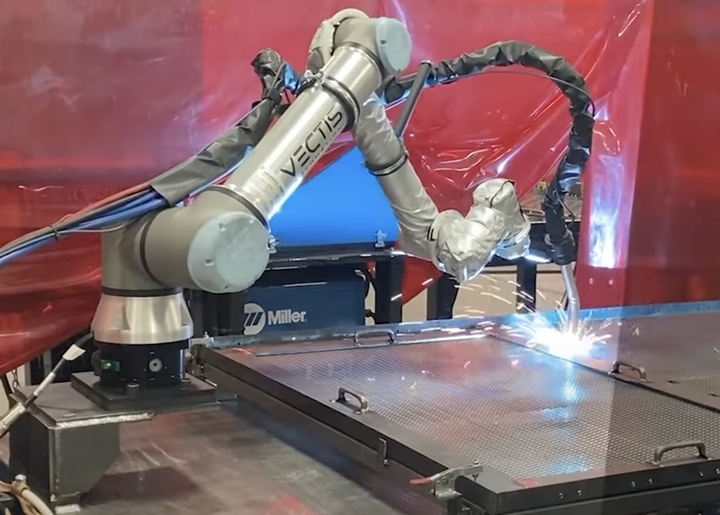
Case Study from | Roboworld
OVERVIEW
Project Goal: Provide best-in-class protection for all Cobot welding stations
Protection Parameters: Airborne spatter from carbon arc gouging, sparks from nearby manual angle-grinding stations, and arc UV emissions
Facility Type: Indoor Fabrication Facilities, with welding and plasma torches that heat up to +3,000 ºF
Companies Involved: Vectis Automation, Roboworld
Location: Loveland, CO, USA
Timing: January 2019 to present
BACKGROUND
Since their founding in early 2019, Vectis Automation has been a champion of best-in-class Cobot technology for a variety of welding applications, including arc welding and plasma cutting. With their smaller footprint and mobile flexibility, Cobots have progressed from an industry niche to a manufacturing necessity in less than five years.
With the talent pool of skilled welders dwindling, the need for automated robotic welding has steadily grown, creating a highly competitive industry. To stand out from their competitors, Vectis positioned themselves as the solution provider that delivers exceptional, durable performance. In fact, their stated goal is to provide robotic systems that reliably perform for 10 to 15 years. To achieve this, they identified a way to provide an additional layer of protection that made a meaningful difference with the help of Roboworld.
CHALLENGE
Vectis Cobots are purposely designed to have less gadgetry to ensure that they will always be durable welding workhorses. “It’s not enough to have our systems work, we want to make sure that hey never break,” says Vectis Founding Partner, Josh Pawley. This is especially important when it’s factored in that one hour of downtime can cost a manufacturer thousands of dollars in lost productivity.
There are three primary hazards that Vectis Cobots must be able to withstand in order to maintain their standard of durability:
- Being in close proximity to manual welding stations where angle grinders or similar cutting tools disperse molten metal sparks.
- Carbon arc or plasma gouging utilizes superheated torches (which can be hotter than the surface of the sun) that use compressed air to dig out the metal, which can spatter unpredictably.
- Welding arcs give off a tremendous amount of ultraviolet (UV) light which over time can degrade plastic components and also cause the colors of the rubber insulation on wires to fade.
In addition, Vectis realized that the teach pendants for each system were vulnerable to damage, not just from the molten drops of metal but also from human error (we’ve all dropped our phone more than once, now imagine if your phone was three times larger and five times heavier). And if a pendant goes offline, the entire system does as well, which means lost operational capacity and less revenue for every hour it’s down.
They explored different ways to safeguard their robots and teach pendants to maximize their uptime, which could be as much as six days a week, 20 hours a day. At the end of their search, Roboworld was the only partner who could deliver that extra level of protection for both.
SOLUTION
By partnering with Roboworld since their first Cobot rolled off the line on Day 1, all of Vectis’ robotic welding systems and teach pendants have included Robosuits® and Pendant Armor®.
Each Robosuit provides a shield from all three potential hazards with no movement restrictions or limitations. If an incident does occur and the Robosuit ever needs to be replaced, it can be done on site, often in as little as 10 minutes. In addition, Pendant Armor provides a perfectly sized, shock-absorbing and chemical-resistant bumper that helps keep the teach pendant safe and sound, even in the harshest environments.
RESULTS
Robosuits and Pendant Armor provide Vectis Automation a visible way to show how they provide a higher level of protection that their customers are seeking, even without asking for it. Combined with Vectis’ reputation for rugged dependability, the peace of mind that comes with every Vectis Cobot system has resulted in their biggest sales funnel being repeat customers who know exactly what they are getting—from both Vectis and Roboworld—from Day 1 through Year 15.
The content & opinions in this article are the author’s and do not necessarily represent the views of RoboticsTomorrow
Comments (0)
This post does not have any comments. Be the first to leave a comment below.
Featured Product
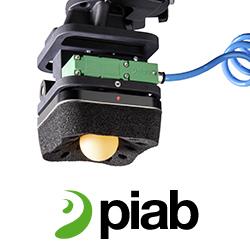