Improved Tails Provide Greater Access for Better Cleanings on Dorner's New AquaGard 7350 V2 Sanitary Conveyor Platform
The AquaGard 7350 V2 with tip-up tails provide ample access to the inside of the conveyor for effective, fast cleanings, and easy maintenance. Tails can be tipped up in just a few seconds with no tools, and then retracted and locked back into place with the same minimal effort.
HARTLAND, Wis., (December 11, 2018) — Perhaps the most important feature of a sanitary belt conveyor is the ability for it to be thoroughly cleaned. The new AquaGard 7350 V2 Series with tip-up tails checks off that box…and then some.
Tip-up tails are standard on the AquaGard 7350 V2 straight-belt models, and also available on straight-running modular belt units. They come with improved strength in the tail for more rigidity and no flexing, as well as supporting the belt/chain closer to the tail for improved performance.
Debuting at PACK EXPO 2018, the AquaGard 7350 V2 is built for numerous sanitary applications within baking, snack food, pharmaceutical, pet food, packaging and other industries that require wipe-down and occasional washdown cleanings of the conveyor. The new conveyor comes in straight belt, as well as modular belt straight and curve models. Belted LPZ, modular belt LPZ and positive drive models will be available in the coming months.
The AquaGard 7350 V2 is the safest, most advanced modular curve chain conveyor in the industry today. The modular belt curve conveyor has no openings greater than the international standard of 4mm, even within the curves, which increases safety by eliminating pinch points for operators. Added safety measures are also achieved by covering the upper and lower chain edges, and fully containing the drive system, which reduces catenary belt sag and conveyor noise.
Space reduction is another improvement on the AquaGard 7350 V2. The modular belt conveyor system is designed to maximize available plant space by keeping the footprint as compact as possible. Infeed and outfeed sections are a compact 18", further saving valuable floor space.
For more information on Dorners new AquaGard 7350 V2 sanitary conveyor platform, visit www.dornerconveyors.com.
Connect with Dorner on Facebook at www.facebook.com/dornerconveyors
Follow Dorner on Twitter at www.twitter.com/dornerconveyors
Subscribe to Dorner on YouTube at https://www.youtube.com/user/DornerConveyors
Follow Dorner on LinkedIn at www.linkedin.com/company/dorner-mfg-corp
###
Hartland, Wisconsin-based Dorner is a world leader in the design, manufacture and distribution of high-quality conveyors and related equipment. Since 1966, companies from around the world have turned to Dorner conveyors for greatly improved efficiency and productivity. For more information about products or company news, visit Dorners Web site at www.dornerconveyors.com or call 1-800-397-8664.
Featured Product
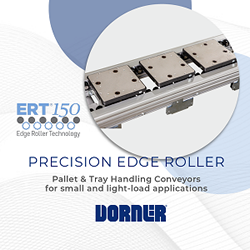
The ERT150 - Dorner's Next Evolution of Edge Roller Technology Conveyors
The next evolution in Dorner's Edge Roller Technology conveyor platform, the ERT®150, is ideal for small and light-load assembly automation, as well as medical and medical-device assembly application. The ERT platform is the only pallet conveyor of its kind available with an ISO Standard Class 4 rating for cleanroom applications. Earning the ISO Standard 14644-1 Class 4 rating means Dorner's ERT150 will conform and not contribute to the contamination of cleanrooms to those standards. As implied by its name, the ERT150 (Edge Roller Technology) uses rollers to move pallets through the conveyor smoothly with no friction (a byproduct often seen in belt-driven platforms). The conveyor's open design eliminates concerns of small parts or screws dropping into rollers and causing conveyor damage or jamming. The ERT150 is suited to operate in cleanroom environments requiring a pallet handling conveyor. It is capable of zoning for no or low-back pressure accumulation and is ideal for automation assembly applications within industries including medical devices, electronics, consumer goods among others.