Locus Robotics Picks Record-Breaking 13 Million Units for Retail and Logistics Partners During November 2019 Holiday Period
LEADING WAREHOUSE ROBOTICS COMPANY ACHIEVES DAILY PEAK OF 1 MILLION UNITS DURING CYBER WEEK
Locus Robotics (www.locusrobotics.com), the market leader in autonomous mobile robots (AMR) for fulfillment warehouses, today announced record-breaking productivity numbers achieved in November 2019, delivering more than 13 million units picked on behalf of global retail and third party logistics customers during the critical holiday season. This is a 400% increase in units picked over last year.
"2019 has been a year of significant transformation and growth for Locus and our customers. We saw an incredible uptick in demand for our scalable, flexible, multi-robot solution," said Rick Faulk, CEO of Locus Robotics. "We've recently launched many new customer deployments in the U.S. and EU markets. Locus helped businesses break productivity records they couldn't have imagined possible even a year ago. This performance is an amazing testament to the value of our solution and underscores the scalability of the Locus solution to help our global customers meet seasonal demand."
The Company's Robots-as-a-Service (RaaS) model enables Locus to seamlessly scale their customers' robot populations at existing sites to support the expected rapid growth in volume during the critical holiday season. Many customers scaled up earlier this season compared to last year, adding to their fleets before the coming rush. Because of these efforts, Locus robots enabled customers to easily manage the steadily growing volume throughout the month, peaking at 1 million daily units during Cyber Week.
A record 189.6 million U.S. consumers shopped from Thanksgiving Day through Cyber Monday this year, an increase of 14 percent over 2018's 165.8 million, according to National Retail Federation and Prosper Insights & Analytics. Locus's collaborative robots drive productivity to ensure that brands are able to keep up with consumer demand and meet fulfillment goals during the busiest shopping days of the year, despite the widespread scarcity of warehouse labor and massive influx in order volumes during holiday months. Customers including DHL, GEODIS, Port Logistics, Verst Logistics, SANDOW, Marley Lilly, and Radial are achieving 200-300 percent improvements in productivity deploying the Locus solution.
ABOUT LOCUS ROBOTICS
Locus Robotics' revolutionary, multi-bot solution incorporates powerful and intelligent autonomous mobile robots that operate collaboratively with human workers to dramatically improve piece-handling productivity 2X-3X, with less labor compared to traditional picking systems. This award-winning solution helps retailers, 3PLs, and specialty warehouses efficiently meet and exceed the increasingly complex and demanding requirements of fulfillment environments, easily integrating into existing warehouse infrastructures without disrupting workflows, instantly transforming productivity without transforming the warehouse. For more information, visit www.locusrobotics.com.
Featured Product
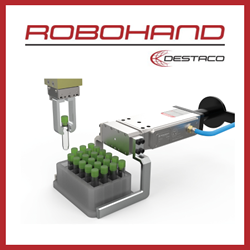
DESTACO - Revolutionizing Industrial Automation
Looking for a reliable solution to enhance your automation process? Look no further than the DESTACO Robohand Grippers. These grippers are designed for the modern world of robotics, offering unparalleled performance and precision. Whether you need to grip fragile items, irregularly shaped objects, or heavy-duty components, the DESTACO Robohand Grippers have got you covered. Their modular design allows for quick and easy customization, ensuring a perfect fit for your application.