With all the benefits offered by robots, the biggest barrier is the complexity of programming. More specifically, the expertise required to effectively program a robot can take years.
Taking a CAD/CAM approach to Offline Robotic Programming
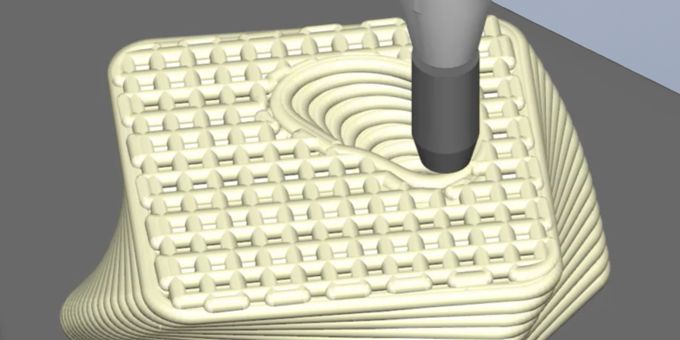
Q&A with Garen Cakmak | Robotmaster
Tell us about yourself and your role with Robotmaster.
My name is Garen Cakmak, and I'm the Senior Director for Hypertherm’s robotic software team. Our team develops Robotmaster, an offline robot programming software.
How can a company or manufacturer benefit by integrating robots into its processes?
Robots offer many benefits to companies such as increased productivity, competitive advantage, cover the lack of skilled labor, safety, consistency, job creation, etc.
Let us take safety for instance; no one wants to be working in an unsafe environment with hazardous materials, dangerous fumes, and very high temperatures. These types of environments are perfect for robots rather than humans, who will be thankful that some of these risks have been removed.
In another example, it's no secret that the skilled labor shortage impacts manufacturing all over the world. This shortage of is also a reality facing manufacturers for the foreseeable future. This is where integrating a robot not only can help fill the gap, but also allow companies to increase productivity and grow their business.
What are the biggest challenges faced when it comes to integrating and working with robots?
Robots are known for production/repetitive work, and programming robots for a low volume production run is challenging. The time it takes to program a robot is time-consuming. If the robot is programmed on the manufacturing floor it requires costly downtime. Sometimes, programming a task proves to be impossible due to the complexity of the process attempting to be automated.
With all the benefits offered by robots, the biggest barrier is the complexity of programming. More specifically, the expertise required to effectively program a robot can take years. Most manufacturers cannot justify this type of learning curve nor the cost in time and money to be able to cross this barrier. Even with the explosive number of robots in manufacturing in recent years, we continue to see companies that have robots sitting idle in their facilities mainly due to this programming challenge.
Tell us about Robotmaster and how it helps people overcome these challenges?
Robotmaster is an offline robot programming software that allows task experts to program their robot quickly and easily from simple to complex tasks while maximizing the robot's capabilities.
So, how does this work and how does it help with the challenges of programming?
Let's say, you’re a manufacturer and you’re an expert at what you do. We call this a task expert. You want to be able to use a robot, but you are not an expert in robotics, nor do you have the time nor the money to become one. The novel approach of Robotmaster is that the software manages not some but all of the unique robotic programming challenges and allows anyone - even those without robotic expertise, to program a task within minutes. In most cases, within a couple of clicks.
Another unique aspect of Robotmaster is that the software in addition to considering some of the common robotic errors, it takes int account every aspect of the challenging job of programming a robot and delivering it to the end user with a completely error free robot program.
It’s the simplicity of this extremely complex task of programming a robot that sets Robotmaster apart.
Where are you seeing the biggest demand for your products currently?
The biggest demand we are seeing is in the lack of skilled manual labor for tasks that cannot be done by mechanized equipment or is not cost effective.
How have you seen the pandemic change manufacturing and what are your thoughts on business and manufacturing going forward?
The pandemic has opened peoples' eyes to the importance of automation.
Before, one of the biggest advantages of using a robot was to be globally competitive, and with the pandemic, this trend has accelerated.
Another change we have seen is that companies are starting to take steps into reshoring. For reshoring to be successful, robotic automation plays a critical part in this process. Robotics was once considered a threat to employment; however, the pandemic has shifted this thinking to robotics being an essential part of boosting the re-shoring of manufacturing.
Why do you feel robotic offline programming is the future of the manufacturing industry?
The hardware side of robots has grown in capability by great leaps and bounds technologically, and the latest innovations were around collaborative robots and enhanced robot accuracy. Armed with this great technology, it helps with the challenges to automate the hardware side of your task. The hardware is only one part of the equation, now it's about getting the software right.
For the manufacturing industry to fully adopt robotics and benefit from all its advantages, they need to look into robotic offline programming the same way the machine tool industry adopted CAD/CAM software. Today, the companies that fully take advantage of their CNC machine tool are the ones who have adopted CAD/CAM software.
It is important for manufacturers to understand that not all offline programming software are equal. For instance, the basic ones are no different than teach pendant programming – done behind a computer. It still requires all the robotic expertise but offers the advantage of being in front of a computer rather than on the manufacturing floor. Others offer partial solutions to get you further along the journey. However, what sets Robotmaster apart is that it offers a complete solution to the task expert and/or robot programmer to quickly and easily program the robot and fully maximize capabilities of the robotic cell, taking a CAD/CAM approach to offline robotic programming.
The content & opinions in this article are the author’s and do not necessarily represent the views of RoboticsTomorrow
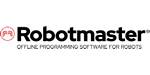
Robotmaster
Robotmaster, a Hypertherm Associates brand, is an offline, is an offline robot programming software that helps manufacturers maximize their robot's productivity with easy and efficient robot programming for a variety of applications such as cutting, trimming, milling, welding, spraying, polishing, sanding, grinding, deburring, and more. Robotmaster uses integrated CAD/CAM functionality to make robotic programming easy and intuitive for everyone, even first-time users.
Other Articles
Have You Looked at Automating Fabrication Tasks in the Past? Why Didn’t You?
Trane® Saves Over 80 Hours of Robot Programming Time
3 Benefits of Working With a Robotic Integrator
More about Robotmaster
Comments (0)
This post does not have any comments. Be the first to leave a comment below.
Featured Product
