Producing the world’s most advanced air defense missile requires technological innovation, especially when annual production is set to increase to 500 by 2024.
Aerobotix Develops All-In-One System for Defense Manufacturer with ATI End-Effectors
Case Study from | ATI Industrial Automation
Producing the world’s most advanced air defense missile requires technological innovation, especially when annual production is set to increase to 500 by 2024. And like any other defense product developed, missiles undergo rigorous inspection processes before deployment. So how will one of the United State’s largest defense contractors meet demand? Using robots.
Aerobotix (ABX) harnesses their expertise in aerospace manufacturing and deep knowledge of robotics to develop robust, innovative manufacturing and refurbishing solutions for their customers. Using large FANUC robots and end-effector technology from ATI Industrial Automation, Aerobotix created a fully automated system that measures the coating thickness on these highly accurate interceptor missiles. The robotic system utilizes three unique end-of-arm tooling (EOAT) systems to complete inspection on the missile, made possible with ATI’s Robotic Tool Changers and Tool Stands.
The hardware and equipment for the inspection process are quite different from the supplies needed for painting and sanding; however, ABX was able to integrate all three inspection operations into one process with custom-configured QC-210 Heavy Duty Tool Changers from ATI. The configuration includes ATI Utility Modules that pass utilities such as pneumatic air for compliance tools, electrical signals, and a Gigabit Ethernet for network communications through the tool changer directly to the EOAT.
ATI’s applications team worked closely with Aerobotix to design a tool changing system to integrate with their specially engineered end-effectors and evolve with customer needs. ATI’s Tool Changer products increase productivity and flexibility, and with ATI’s Utility Modules, can be configured for any application. This makes it easy for ATI customers to implement tool changing in a vast range of application environments.
ABX and ATI develop robust and innovative solutions that help customers embrace the ever changing and highly competitive manufacturing market. The multi-tasking solution Aerobotix developed allows their customer to recognize returns on their robot at a much higher rate. Because they can exchange tools and connect utilities automatically, the customer is able to deploy a variety of robotic processes in one cycle. The design keeps utilization high while realizing a more efficient process with higher quality outputs.
When the customer needs a change, as they always do, customers can seamlessly reconfigure and reprogram their system to accommodate new operations on various parts. With reliable equipment and comprehensive support from ABX and ATI, customers can stay flexible, responsive, and confident. ATI and Aerobotix help customers tackle the challenges they face today and keep an eye on the future with solutions that are simple and smart with room for growth.
About Aerobotix
Headquartered in Huntsville, Alabama, Aerobotix is an innovative leader in robotic solutions for the aerospace and defense industries. The company specializes in the creation of cutting-edge automated robotic measuring solutions for high-value, high-precision components, aircraft, and vehicles. Aerobotix has more than 130+ robotic systems installed in the U.S. and abroad, providing exceptional results and savings for our clients.
The content & opinions in this article are the author’s and do not necessarily represent the views of RoboticsTomorrow
Comments (0)
This post does not have any comments. Be the first to leave a comment below.
Featured Product
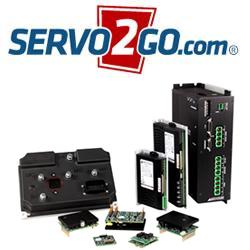