A trend toward replacing those fixed, conveyor-based assembly lines with fleets of mobile robots holds the promise of another step change in manufacturing efficiency and new adaptability to market volatility.
Synchronized Mobile Robot Fleets Bring New Versatility and Investment Protection to Assembly Operations
Gerard Vilarrasa, Product Manager | Kivnon
When Henry Ford introduced the assembly line just over one hundred years ago it was truly a breakthrough in manufacturing efficiency, improving, for example, automotive flywheel production by about 75 percent over manual operations. Today, a trend toward replacing those fixed, conveyor-based assembly lines with fleets of mobile robots holds the promise of another step change in manufacturing efficiency and new adaptability to market volatility.
Improving transport efficiency
Mobile robots such as automated guided vehicles (AGVs) and autonomous mobile robots (AMRs) are self-driving vehicles that carry loads from one industrial operation to another. They have built-in sensor-based navigation systems that allow them to drive safely and efficiently in work areas, without risk of collision.
The first generation of mobile robots improved efficiency by automating picking, bringing parts to a conventional conveyor line, and moving finished goods from the end of the production line to the warehouse for eventual shipping. Automobile manufacturers were the first to exploit this potential, transporting components and sub-assemblies and ensuring the accuracy of parts delivery. Such automation improved productivity and ergonomics by eliminating the myriad steps pickers or operators might have had to take otherwise.
Inefficiencies of legacy conveyor systems
However, as consumers began demanding more product variability and faster delivery, fixed conveyor systems have inherent inefficiencies that make them less suitable for these emerging needs. Their permanent structures limit them to handling only a limited range of sizes, shapes, and production volumes. If anything changes in the demand or product profile, accommodation is usually costly if possible at all.
Their single-stream workflow of conveyor belts also enforces rigid assembly sequences. Even though they may work on only part of the car, appliance or whatever is on the line, line workers may have to sit idle while watching other product sections go by. If there is a delay upstream, downstream workers may have to sit idle waiting for upstream operations to complete. All of which adds delays and costs to the operation.
Improving production efficiency
Rethinking the assembly line as a configuration of distributed but integrated mobile robots changes all that, raising manufacturing efficiency, flexibility, customizability, and profitability to new heights. A new generation of intelligent mobile robots has more advanced navigation, control, and communications. Instead of delivering components to a fixed conveyor belt, synchronized fleets deliver them to workstations dedicated to specific production sequences.
Manufacturing system designers may also equip mobile robots with tools, such as robot arms that involve them in conducting the operations. Even when supporting an existing conveyor, the robots can improve efficiency by moving to the part of the line that is ready for them and integrating it later. Also improving efficiency is that robots can work 24/7, maximizing production flow. They can perform repetitive tasks, minimizing human error that can lead to defects or rework.
Flexibility supports revenue generation
In addition to the efficiency improvement, which improves profit margins by lowering production costs, synchronized mobile robot fleets help generate revenue by providing agility to meet changing market demands.
When marketplace demand shifts, as is increasingly the case in today’s volatile economies, manufacturers who cannot adapt operations to meet that demand effectively may miss significant opportunities. This is especially true for complex, non-linear assembly tasks that require frequent changes in the order of operations or multiple workflows that do not lend themselves well to conveyor-based systems. With conventional conveyor belts, switching from assembling cars to off-road vehicles, for example, could require building another assembly line, but with automated vehicles, the manufacturer might be able to do it all with software.
Mobile robot fleets also optimize space utilization; the same space can handle multiple projects.
Easy hardware customization
Not all changes can be software-configured, but hardware configuration is much easier with a mobile fleet. Users may, for example, modify the robots to accommodate different loads, parts, or tools. Doing so with conveyor belts is complicated, but mobile units typically have a flat surface onto which the user or manufacturer can bolt or otherwise swap out an infinite number of attachments.
Transitioning to a mobile robot fleet
Transitioning to a smart, flexible self-driving robot suite does not necessarily require ripping and replacing existing conveyor belts. Many users start with one or two AGVs pr AMRs, often carrying goods to or from an existing conveyor system. They then deploy more units to meet growth needs, equipping them accordingly.
Building a mobile robot brigade starts with modeling and projecting the line availability needed to amortize the investment. A realistic model is especially critical for those considering conventional conveyor belt-driven assembly operations because it will be exceedingly difficult to change once they build it.
With the mobile fleet approach, on the other hand, if the production projections plan calls for maximum utilization in five years, for example, you may be able to start with one or two units now and add on as your volume grows. If your projections caused you to purchase more AGVs than you need, you can assign the overage to another project.
How AGV fleets protect investment- Summary
Given the improvement in effectiveness, flexibility and customization mobile robots represent a more secure investment than a conveyor belt-based system for at least the following reasons.
-
Mobile robots automate repetitive tasks, reducing production costs and human error.
-
In addition to reducing costs, improved effectiveness means you can get products to the market faster.
-
The modularity of a mobile fleet enables easy scaling as demands change.
-
Mobile robots can integrate easily into full hybrid solutions involving other technology, such as stationary robots and imaging devices.
-
Manufacturers can use the same space to support many operations over time.
Conclusion
Anyone looking for an assembly line solution, especially if considering purchasing a conveyor belt, should consider the value of using mobile robots to synchronize operations at distributed workstations instead of locking them into a rigid production line sequence. Anyone who has a need for high-speed, high-volume production and is confident that that need will not change significantly over the time it takes to amortize the cost, might be okay with a conventional conveyor system. But if they have more complex operations, want to reduce production costs, and scale easily, configuring a fleet of mobile robots as an assembly operation is the best solution.
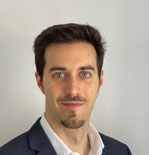
About Gerard Vilarrasa
Gerard Vilarrasa is the Product Manager at Kivnon. Electrical engineer with almost a decade of experience in the industrial sector, the majority of them in mobile robotics product development and management at Kivnon.
The content & opinions in this article are the author’s and do not necessarily represent the views of RoboticsTomorrow
Comments (0)
This post does not have any comments. Be the first to leave a comment below.
Featured Product
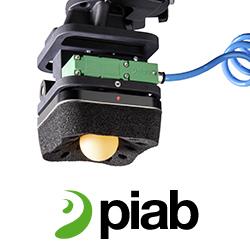