A smooth production process is critical for a company’s success. The constantly growing demands of the market and increasing cost pressure require innovative solutions to optimize production. This is where transfer systems come into play.
Enhancing Production Efficiency Through Intelligent Transfer Systems
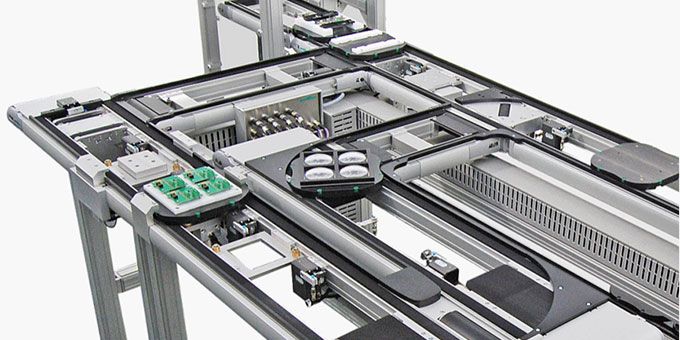
Article from | Montech Conveyors
Transfer systems are mechanical devices used to move materials, components, and workpieces from one station to another in a production process. They can be linear or circular, are available in a variety of design sand integrate well with conveyors, robot arms, automation elements, etc. A key difference from conventional belt conveyors is that transfer systems often have a high level of intelligence that allows them to operate autonomously and communicate with other production units.
Intelligent control and automation
A major advantage of transfer systems is their intelligent control and automation. By using sensors and modern technology, they can efficiently monitor and control the flow of materials. This enables rapid adaptation to changes in production, it minimizes downtime and helps avoid bottlenecks. In addition, these systems can capture real-time data, providing valuable insight into the production process and a foundation for continuous improvement.
Flexibility and adaptability
The requirements of modern production processes change frequently. In this context, transfer systems demonstrate their flexibility and adaptability. They allow different production lines to be redesigned with minimal effort, so that companies can respond quickly to new market developments or customer-specific requests. The integration of artificial intelligence and machine learning into transfer systems even enables them to learn and optimize new processes independently.
Time and cost efficiency
Transfer systems contribute significantly to time and cost efficiency in production. Their fast, precise, and reliable handling of materials and workpieces reduces throughput time, resulting in increased productivity. Automating transport and handling tasks also reduces the need for manual work, minimizing potential sources of error, and personnel costs.
Improved occupational safety
Occupational safety also plays a central role in modern production. Transfer systems relieve employees of dangerous and repetitive tasks by handling the transport of heavy or hazardous materials. This significantly reduces the risk of accidents and injuries in the workplace.
Multi-functional transfer systems for efficient production and precise assembly
With the LTE and LT40, Montech offers multi-functional transfer systems. By enabling the feeding, unloading, buffering, separating, and positioning of workpieces and workpiece carriers in an optimal way, they ensure smooth and efficient production processes in a wide range of industrial applications. Thanks to the modular toolbox system for framing and conveyor technology, companies can design their production processes efficiently, while the globally proven solutions and extensive range of accessories allow versatile adaptation to individual requirements. With our transfer systems, companies can increase productivity, reduce costs, and improve the quality of their production.
The content & opinions in this article are the author’s and do not necessarily represent the views of RoboticsTomorrow
Comments (0)
This post does not have any comments. Be the first to leave a comment below.
Featured Product
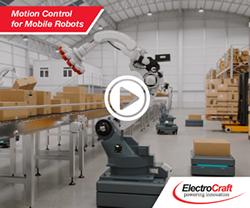