The robots require minimal training to operate, while reducing production costs and improving productivity. They are flexible to deploy on open beds, hoop houses and greenhouses with any type of plant on all common ground surfaces including ground cloth, poly, and gravel.
Contributed by | Harvest Automation
Loma Vista Nursery
Can a focused nursery operation catering to landscapers reap the benefits of Harvest Automation’s robots? The answer is a resounding “Yes”. When people typically think of the nurseries that capitalize on automation of the sort that Harvest Automation provides, images of large industrial scale operations selling plants to big box storesimmediately come to mind. Loma Vista Nursery in Ottawa Kansas proves that you don’t need unlimited resources to take advantage of the efficiencies that robotic automation can deliver.
Loma Vista Nursery produces high quality container and field grown plants for retailers, wholesale distributors, and landscapers across the Midwest. They currently grow over 650 varieties of shade and ornamental trees, shrubs, perennials, and ornamental grasses.
Founded in 1991 by Mark Clear, Loma Vista Nursery is family owned and operated. With a 310 acre container production nursery located in Ottawa, Kansas, just 40 minutes south of Kansas City, Loma Vista Nursery caters to landscapers with a full service Landscape Distribution Center in Olathe, Kansas, to meet their local customer's needs.
Does an investment in robots make sense if you are a nursery that does less than $10M in annual revenue? Ben Cecil, Loma Vista’s Production Manager, and Jonathan McCombie, Head Grower, certainly thought so. After viewing an in-person demo and doing research of their own, they decided to take the plunge. Loma Vista’s robots arrived in April 2013 at the height ofthe busy spring season. The robots require minimal training to operate, while reducing production costs and improving productivity. They are flexible to deploy on open beds, hoop houses and greenhouses with any type of plant on all common ground surfaces including ground cloth, poly, and gravel. The robots provide consistent spacing accuracy no matter how long the day is, without breaks, allowing growers to get quality work done whenever they need it.
Harvest Automation HV-100 robots were the key that unlocked production efficiencies for Loma Vista. But the team still had to determine the best way to get plants from the potting line to the fields and in position for the robots to space.
One asset that they had at their disposal was a number of drop trailers. Drop trailers can be loaded with plants from the potting line, driven to a field where a skilled operator can deposit the pots with reasonable precision. The bed of the trailer can be tilted down to the ground, and as the tractor that pulls it moves away a moveable bar that is controlled by the driver of the tractor pushes pots out the back of the trailer. A skilled operator can manage this with a one or two helpers on the field, placing pots with precision and without damaging delicate new plants or beds that would require costly and time consuming repair work.
Figure 1: Drop Trailer in Action
The team loaded the trailers with 144 5-gallon containers and set 7 loads down at 20’ intervals on their 150’ long x 18.5’ wide gravel beds. 5-gallon containers are large and often over 20 pounds; people may quickly tire of moving these containers, but Harvest Automation robots handle this load efficiently and without hesitation. The simplicity of setup and ease of use of the HV-100 allowed a single supervisorto easily manage the robots on his own after a brief training session. Ben and Jonathan configured the robots to space these loads on an 18.5’ bed with a 20” x 20” hex spacing.
After only a few practice runs, the Loma Vista team quickly got into a groove and from then on the system worked wonderfully. In under threemonths’ time the HV-100s have spaced over 100,000 plants. "Only weeks after bringing in the HV-100s, the robots increased productivity prompted us to reconfigure our standard method of plant movement and gain greater efficiency overall," said Jonathan. "As a result the robots played a crucial role towards achieving our spacing needs at the appropriate time." Proof positive that robotic automation can be successfully applied to any type of operation. Nursery and Greenhouse operations of all shapes and sizes can benefit from the production efficiencies that Harvest Automation robots deliver.
Figure 2: HV-100 Robots Hard at Work
For more information about LomaVista Nursery please visit http://www.lomavistanursery.com/.
For more information about Harvest Automation and the HV-100 please visit http://www.harvestai.com.
The content & opinions in this article are the author’s and do not necessarily represent the views of RoboticsTomorrow
Comments (0)
This post does not have any comments. Be the first to leave a comment below.
Featured Product
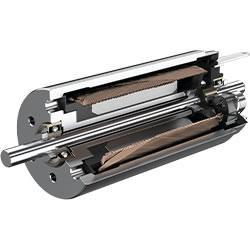