RMT Robotics Celebrates Seven Years of ADAM Mobile Robot Success in Tire Handling
Building on RMT's gantry-based automated storage and retrieval system for the tire industry, ADAM provides a flexible robotic solution for press delivery without the expense and disruption of conventional GT storage and press delivery systems.
Grimsby, Ontario, Canada (July 24, 2012) - RMT Robotics® (www.rmtrobotics.com), a Cimcorp Oy company and the manufacturer and integrator of the ADAM autonomous mobile robot (AMR) (www.adamrobot.com), is pleased to celebrate seven years of ADAM's proven industry success as a tire handling solution. Since July of 2005, ADAM has maximized the efficiency of green tire (GT) transport from component handling to tire build machine (TBM) collection to press delivery.
ADAM promotes lean manufacturing efficiency in tire manufacturing facilities by automating component handling and orchestrating work-in-process (WIP) logistics, delivering what is needed in the exact time and quantity required. Building on RMT's gantry-based automated storage and retrieval system for the tire industry, ADAM provides a flexible robotic solution for press delivery without the expense and disruption of conventional GT storage and press delivery systems.
ADAM delivers seamless, intelligent and efficient transportation of green tires through:
· Compact design - ADAM can position itself beneath the press load arm.
· Lean manufacturing - Reduced quantities of WIP at TBM eliminates clutter and improves efficiency.
· Flexibility and modularity - No external guide path network or sensors necessary, ADAM requires few modifications to infrastructure or operations.
· Adaptability - ADAM is capable of delivering both passenger and truck tires and accommodates multi-style presses.
"Since 2005, ADAM has been attracting interest around the world as a state-of-the-art robotic green tire handling solution capable of reducing operating costs and improving overall plant productivity," said Don Heelis, global sales manager - tire systems, RMT Robotics. "ADAM's flexibility and modularity as well as lean manufacturing capabilities make it the ideal solution for complex tire manufacturing environments."
About RMT Robotics
RMT Robotics (www.rmtrobotics.com), a Cimcorp Oy Company, is a global company that manufactures and integrates turnkey robotic gantry-based order fulfillment and tire handling solutions designed to reduce operating costs and streamline operations.
To extend the flexibility of robotics beyond a fixed workspace, RMT Robotics also manufactures and integrates ADAM™, the category-defining autonomous mobile robot. The ADAM system redefines the purpose and function of industrial AGVs by performing intelligent robotic transport of materials in complex, random origin to random destination industrial environments.
Since 1981, RMT Robotics has been recognized around the globe as an innovator in robotics materials handling. RMT helps our customers compete in an increasingly aggressive and price-sensitive global marketplace by providing best-in-class robotic handling solutions.
Featured Product
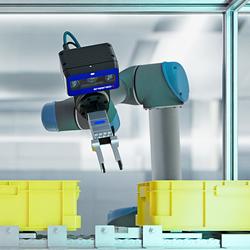