Advanced Motion Controls announces the release of EtherCAT Servo Drives and New 'DxM' (Demultiplexed Motion) Technology
These products not only provide precise motion but also at reduced cost when applied in a multiple networked axes system.
OEM's are continually challenged to provide motion control precision at lowest possible cost. Precision has been given a boost with the advent of EtherCAT®, an open Ethernet-based network standard setting new heights for real-time performance and topology flexibility, and has been the fastest growing area in motion control technology.
As part of our highly successful Z-Drives platform of plug-in servo drives, ADVANCED Motion Controls is proud to formally release powerful DZE & DZS series of servo drives for EtherCAT enabled control networks but with package size that can easily fit in the palm of your hand. These products not only provide precise motion but also at reduced cost when applied in a multiple networked axes system.
ADVANCED Motion Controls has also created exclusive 'DxM' - Demultiplexed Motion technology allowing connectivity of up to 3 DZS drives (sub-nodes) to a single DZE (node) on an EtherCAT® network for up to 4 axes of servo motion. Removing the cost of additional EtherCAT® nodes greatly reduces overall system cost. 'DxM' technology handles all sub-node activity easily through one node, making master tasks much simpler in multi-axis systems.
Also introduced are new DPE series of EtherCAT enabled servo drives as part of the panel mount DigiFlex® Performance™ platform. Both DPE's and DZE's can be used as stand-alone EtherCAT® slave nodes in single-axis setups or as part of a larger, multiple axes EtherCAT network. The DZS's must be used as sub-nodes in a 'DxM' configuration with a DZE node.
More information on the EtherCAT Servo Amplifiers from Advanced Motion Controls can be viewed at-
http://www.servo2go.com/search.php?search=ethercat&D=PROD
Featured Product
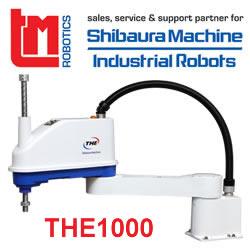
TM Robotics - Shibaura Machine THE SCARA range
The THE range from Shibaura Machine is an extensive line up of SCARA robots. Available in four arm lengths THE400 (400mm), THE600 (600mm) and the most recent THE800 (800mm) and THE1000 (1000mm), this range is suitable for assembly, handling, inspection and pick and place processes in varied industrial applications. The THE1000 boasts a 20kg payload capacity and an impressive 0.44 second cycle time, providing high speeds for processes with large components. In fact, the range has been recognised for as the price-to-performance leader compared to other SCARA models in its price range due to its impressive speed versus payload capacity.