ATI Developing Force/Torque Sensing Technology for NASA
New Engineering to Improve ATI's Products in Extreme Environments
ATI Industrial Automation was recently selected by NASA to develop Multi-Axis Force/Torque Sensing Technology that can be used in space exploration, like the Mars 2018 Mission. Currently under development, this new technology will enable fabrication of a Force/Torque Sensor for the Mars rover's robotic arm. Sensor feedback would allow the arm to guide its coring tool into rocks and then safely place the rock samples in the rover's canisters. There are a number of potential NASA applications for this new Sensor, providing valuable force feedback to a teleoperated robotic arm on the International Space Station or for providing loading feedback for limbs in a humanoid robot application.
The technology being developed will improve ATI's products for use in extreme environments. This includes industrial applications with extreme heat, cold, high acceleration, ultra-high vacuum, vibration, and magnetism. ATI's work in welding, food handling, and foundries will be enhanced with the technology developed for NASA. "This project for NASA will give us the technology to stay on the cutting edge," said Robert Little, COO, ATI Industrial Automation.
ATI's Force/Torque Sensor System measures six components of force and torque (Fx, Fy, Fz, Tx, Ty, Tz) and features a compact design, hardened stainless steel construction, high-speed output, overload protection, span temperature compensation options, and high signal-to-noise ratio. ATI offers a wide range of custom and standard sensor models from 17 mm to 330 mm and include environmental protection (IP) on most models. With over 20 years of robotic end-effector innovation, ATI's engineering department, the largest of its kind for a robotic tooling company, is focused on developing cost-effective, state-of-the-art products and solutions.
About ATI Industrial Automation:
ATI Industrial Automation is the leading engineering-based world developer of robotic accessories and robot arm tooling, including Automatic Tool Changers, Multi-Axis Force/Torque Sensing Systems, Utility Couplers, Robotic Deburring Tools, Robotic Collision Sensors, Rotary Joints, and Compliance Devices. Our robot end-effector products are found in thousands of successful applications around the world.
Featured Product
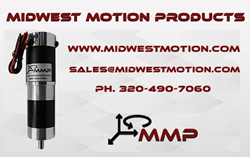