Robot-manufactured cells for the photovoltaic industry
The demands placed on automated handling in solar cell production push conventional solutions to their limits.
During the manufacture of solar cells, wafers go through a variety of wet chemical processes. The handling of these thin silicon wafers before and after the wet bench is done by robots. Here, the requirements are clearly defined: the shortest cycle times with the lowest rate of breakages for this valuable throughput - a balancing act that can only really be achieved using automation at the very highest level.
The demands placed on automated handling in solar cell production push conventional solutions to their limits. Modern systems, which are primarily used in the Far East, are expected to achieve an output of 3,000 wafers an hour. At the same time, the ultra-thin silicon wafers must be handled with the utmost care, as each seemingly insignificant disruption in the motion sequences of the robots inevitably leads to breakages. This is not only expensive for the systems operator; it can also have unpleasant repercussions for the systems manufacturer who is normally expected to guarantee a breakage rate of less than 0.1 percent.
Amberg-based systems integrator baumann nevertheless specializes in automated solutions for photovoltaics, offering standardized modules for loading and unloading the so-called wet benches. And systems 'Made in Germany' are in great demand in the Far East where business in loading and unloading modules is booming. The reason for this is their impressive performance, which sets new standards in the decisive factors of cycle time, breakage rate and reliability. Core of these systems is the high speed SCARA made by Stäubli. The latest loading modules use the new Stäubli TS60 SCARAs for the first time.
baumann modules are designed for handling two different sizes of mono-crystalline and poly-crystalline wafers. The dimension of the wafer can be either 125 x 125 millimeters or 156 x 156 millimeters. Changing from one size to another takes a maximum of ten minutes, thanks to sophisticated hardware and software solutions.
High-speed SCARAs replace Delta kinematics
The wafers arrive at the loading modules via a single-track conveyor belt. Here, robots take the ultra-thin wafers and place them in precisely defined positions on the five roller tracks of the wet bench. In order to achieve the necessary cycle time - the system is designed for a maximum output of up to 3,000 wafers per hour - baumann favors an unconventional solution. The Amberg automation specialists deliberately chose not to use Delta robots for this application but to work with two very fast Stäubli TS60 SCARA robots.
Jörg Weigert, Project Manager at baumann, sums up why they are using SCARAs: "We are absolutely convinced by the performance of the Stäubli SCARAs. The robots are fast, precise and extremely reliable, even when they are in constant use over a multi-year period. The SCARAs from Stäubli are simply unbeatable, particularly with regard to what really matters in these applications, namely robustness and reliability with minimum maintenance requirements."
Jörg Weigert sees a further plus point for using SCARAs in their simple integration into the slender baumann modules. Because of the associated high levels of torque, Delta kinematics would require the module to be constructed on a disproportionately larger scale. This would run contrary to the baumann philosophy, which is to design systems to
be as compact and reliable as possible.
In addition, this application necessitates the use of two robots - regardless of whether Delta or SCARA kinematics apply - because of the conditions on the wet bench. The distances between the conveyor belt and the five roller tracks of the wet bench are simply too great to be serviced by one robot.
By using two robots per module, the lower initial cost for the SCARA represents a significant advantage. baumann also uses robots from Stäubli for the unloading module on the opposite side of the wet bench in order to guarantee absolute consistency throughout the automated process.
Perfect synchronization
At baumann, they are particularly proud of the perfect synchronization between the two robots and the speed of the conveyor belt. After all, the SCARAs take turns to pick up from the same point on the conveyor line. They have been programmed in such a way as to make collisions impossible. Additional collision protection is not necessary. At the same time, the two robots must be perfectly synchronized with the speed of the conveyor belt. "Programming these tasks required considerable expertise on the part of our specialists. They found the multitude of options provided by the Stäubli CS8C controller and conveyor tracking very helpful."
Precise alignment of the micron-thin silicon wafers is essential when these are placed on one of the five tracks of the wet bench. The two TS60s use their vacuum grippers to alternately pick up wafers from the single-track feed conveyor at incredibly high speeds. Immediately before this, an image processing camera positioned above the feeder belt captures the exact position where the wafers are arriving, and transmits the coordinates within a few milliseconds to the robot controller. The robots are then charged with the job of accurately depositing their valuable load at an exact position on one of the five wet bench tracks.
The handling processes are steady and smooth, despite the high speeds involved.
Refined programming together with specially developed grip technology ensures that the breakage rate is often significantly lower than the manufacturer's guaranteed rate. "We know from our customers that the systems often work for several days at a time without a single wafer being broken," says Weigert.
The systems run 24 hours a day, seven days a week. "Under these conditions, we have to guarantee an overall availability of 97 percent. This means that, for these modules, we have to use only the very best components that are available on the market. One such component is the Stäubli robot. Its performance and extremely long maintenance intervals has played a significant part in shaping the reputation of our modular cells," says a delighted Jörg Weigert.
About Stäubli: Textile Machinery, Connectors and Robotics
Stäubli is a mechatronics solution provider with three dedicated divisions: textile machinery, connectors and robotics. With a workforce of 4000, Stäubli has a presence in 25 countries and agents in 50 countries around the world.
Featured Product
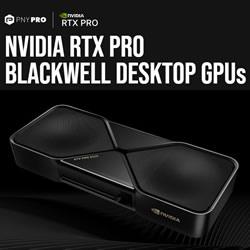
NVIDIA RTX PRO™ BLACKWELL DESKTOP GPUs
NVIDIA RTX PRO™ - Built for Professionals - NVIDIA RTX PRO Blackwell Desktop GPUs feature the latest breakthroughs in AI, ray tracing, and neural rendering technology to power the most innovative workflows in design, engineering, and beyond.