ATI Develops Micro Robotic Tool Changer
QC-001 Provides Flexibility To Extremely Light Payload Robots
ATI Industrial Automation has developed a new Robotic Tool Changer for extremely light payloads. The QC-001 model Tool Changer features an extremely compact and lightweight design for high-speed \"spider\" or delta robots. This new Tool Changer enhances the flexibility of these robots by enabling them to switch end-effectors automatically. Multiple assembly, dispensing, sorting, and material handling operations can be performed by one robot, greatly increasing productivity, while reducing downtime for change-overs. The QC-001 Tool Changer also features integrated pneumatic ports and electrical connections.
Product Features and Options:
Payload: 2.2 lb (1 kg).
Weight (when coupled): 0.12 lb (0.055 kg).
Stack Height (when coupled): 0.67 in (16.9 mm).
Electrical Pass-throughs: 8-pins @ 3 Amp/50VAC.
Pneumatic Pass-through Ports (qty): (4) M5.
ATI offers a wide selection of Tool Changer models to cover a variety of applications. Key features include: Excellent repeatability, high rigidity, and a lightweight and compact design. With over 20 years of robotic end-effector innovation, ATI's engineering department, the largest of its kind for a robotic tooling company, is focused on developing cost-effective, state-of-the-art products and solutions.
Featured Product
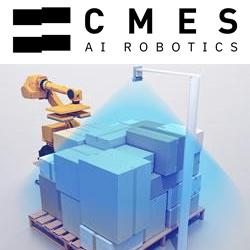