Metcam Adopts New Technologies; Expands Production Capacity; Resulting in Record Sales Growth
Metcam, a fabricator of sheet metal components and assemblies for OEMs, today announced it has completed implementation of a number of improvements, from plant configuration changes and floor space expansion to installation of more than $2 million in new equipment. These enhancements, accompanied by continued diversification of its customer base and expansion of customer relationships, enabled Metcam to achieve record sales in 2012.
April 30, 2013
Metcam, a fabricator of sheet metal components and assemblies for OEMs, today announced it has completed implementation of a number of improvements, from plant configuration changes and floor space expansion to installation of more than $2 million in new equipment. These enhancements, accompanied by continued diversification of its customer base and expansion of customer relationships, enabled Metcam to achieve record sales in 2012.
"As a fabricator dedicated to lean processes, Metcam is constantly redesigning its shop floor and production lines for process automation and optimal output," said Metcam President Bruce Hagenau. "A few years ago, we increased production space with new plant configurations, and that space was immediately consumed by new orders. In the past year, we have expanded our capacity yet again-and added new staff and a new enterprise resource planning system-to keep pace with continued, escalating demand for our components and assemblies."
Specific improvements Metcam has implemented include:
New Robotic Press Break: Metcam's new robotic press brake simultaneously uses two robots. One robot positions blanks for forming and unloads formed parts, while the other robot forms the part in combination with the press brake.
Automated Hager Press: One of Metcam's new Hager presses enables personnel to auto-select up to four different types of hardware. The press provides a view of the part and shows the operator which hole will have hardware pressed into it on the next stroke. If tooling is different from one piece of hardware to the next, the tooling is automatically changed as well, further streamlining the hardware-insertion process.
New Aluminum Robotic Welder: In addition its robotic steel-welding capabilities, Metcam can now robotically weld aluminum as well.
New Paint Line: Metcam has added a second paint line, which uses state-of-the art lean-painting technologies, such as a modular fiberglass wash system (95' long) and two powder booths with paint reclamation capabilities.
New Turret Punch: Metcam has added a seventh operational turret punch.
"While many of our improvements help to increase automation, Metcam has also added staff this year," said Hagenau. "That is a testament to our growth and expanding customer base, which includes a new OEM and an expanded relationship with one of the world's largest producers of office components."
About Metcam
Metcam is a fabricator of precision sheet metal components and assemblies for original equipment manufacturers (OEMs) representing a wide variety of industries including telecommunications, electronics and HVAC. Metcam's advanced metalworking capabilities include laser cutting, punching, forming, hardware insertion, welding (including robotics), powder painting, silkscreen and parts assembly. Metcam also assists clients with product design and manufacturability to reduce their total cost of production. Metcam's award-winning service, combined with an aggressive focus on quality, environmental management and lean manufacturing, simplifies the outsourcing decision for firms worldwide.
For more information, visit http://www.metcam.com.
Featured Product
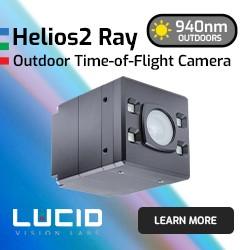
Helios™2 Ray Time-of-Flight Camera Designed for Unmatched Performance in Outdoor Lighting Conditions
The Helios2 Ray camera is powered by Sony's DepthSense IMX556PLR ToF image sensor and is specifically engineered for exceptional performance in challenging outdoor lighting environments. Equipped with 940nm VCSEL laser diodes, the Helios2 Ray generates real-time 3D point clouds, even in direct sunlight, making it suitable for a wide range of outdoor applications. The Helios2 Ray offers the same IP67 and Factory Tough™ design as the standard Helios2 camera featuring a 640 x 480 depth resolution at distances of up to 8.3 meters and a frame rate of 30 fps.