Stäubli Robotics Announces the Robot Industry's most comprehensive Load Balancing Software Package
Perfect solution to sorting, and pattern making, with variable infeed and the requirement for a stable out flow for post processes
Stäubli introduces the partnership with a leader in Load Sharing Software to release the Robot Industry's most comprehensive Load Balancing Software Package. This package is available on all Stäubli Robots but is Stäubli Robotics Announces the Robot Industry's most comprehensive Load Balancing Software Packageparticularly well suited to the TP80 Fast Picker line. This is the perfect solution to sorting, and pattern making, with variable infeed and the requirement for a stable out flow for post processes.
Features Include:
*Parallel Flow, Counter Flow, and Mono Flow conditions are easily handled
*100% matching for all pick and place locations
*Full traceability of each part along the entire process
*Ensures 100% full output regardless of infeed flow variation by reacting to each pick and place incidence intelligently- Not a Gatekeeper.
*Performs Centralized Line Control without a PLC
*Controls infeed speed automatically
*Controls Out Flow speed automatically
*Controls all robot speeds
*Collision Avoidance via Robot Axis Controls
*No need to program specific conditions for individual robots on the line.
The first 60 - 70% of Load Balancing conditions are relatively easy with existing software options, but Stäubli has exceed expectations in offering this totally comprehensive solution.
About Stäubli:
Stäubli is a mechatronics solutions provider with three dedicated divisions: Textile Machinery, Connectors and Robotics. With a workforce of 4000, Stäubli has a presence in 25 countries and agents in 50 countries around the world
Featured Product
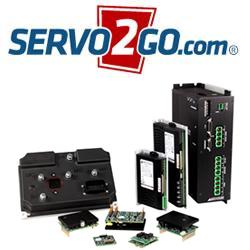