Evana Automation helps AAM reduce capital expenditure by 50% with lean clutch assembly line
Evana introduced AAM to a less costly Lean Manufacturing approach that would use the same number of operators as the automated line, but allow the flexibility to use fewer operators for smaller volumes.
Evansville, Indiana - Evana Automation Specialists, a subsidiary of Phillips Service Industries (PSI) and leading Systems Integrator and builder of custom, automated assembly and test systems, class="text">recently delivered a lean clutch assembly line to American Axle & Manufacturing, Inc. (AAM).
AAM initially came to Evana with a concept and specification for an automated clutch assembly line that cost 50% more than they had originally budgeted. To get over this financial hurdle, Evana introduced AAM to a less costly Lean Manufacturing approach that would use the same number of operators as the automated line, but allow the flexibility to use fewer operators for smaller volumes. AAM went with Evana's Lean Manufacturing approach, which integrated automatic and semi-automatic processes to assemble high volumes of automobile clutch assemblies with best-in-class quality control technology.
"Evana Automation's use of vision guidance and robotic integration is a key competitive advantage for our customers," said Randy Wire, General Manager of Evana Automation Specialists. "We always go the extra mile to make sure our solutions offer maximum efficiency."
Evana utilizes diverse technologies to specialize in motion control, robotics integration and system architecture by linking production equipment, material handling systems, data collection, networking, as well as computer software and hardware into flexible, unified technology. Test equipment can be integrated into assembly systems, stand alone systems for automatic testing, or manual test benches. Overall, Evana's custom assembly and test solutions improve efficiency for manufacturers all over the world in industries like automotive, aerospace, defense, healthcare and alternative energy.
AAM is a world leader in the manufacture, engineering, design and validation of driveline and drivetrain systems and related components and modules, chassis systems and metal-formed products for trucks, sport utility vehicles, passenger cars and crossover utility vehicles. In addition to locations in the United States (Indiana, Michigan, New York, Ohio, and Pennsylvania), AAM also has offices or facilities in Brazil, China, Germany, India, Japan, Luxembourg, Mexico, Poland, South Korea, Sweden, Thailand and the United Kingdom. For more information, visit www.aam.com.
Featured Product
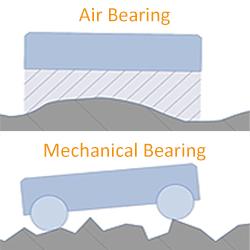
PI USA - High Precision R-Theta Stages for Semicon, Laser Processing Apps
2-axis R-Theta motion systems are better suited to spiral motion than Cartesian XY stages. R-Theta systems often find applications in precision laser / semiconductor applications due to higher throughput, precision, and smaller size. See examples and options.