Wynright Receives NextGen Game Changer Award For Groundbreaking Robotic Truck Unloader
Intelligent material handling systems provider recognized for its innovative approach to automating the unloading process in warehouses and distribution centers
ELK GROVE VILLAGE, Ill.--Confirming its industry-leading position as a developer of innovative solutions, Wynright Corporation, a wholly owned subsidiary of Daifuku Webb and a leading U.S.-based provider of intelligent material handling systems, has been named the winner of the NextGen Game Changer Award for its Robotic Truck Unloader (RTU).
According to Robotics Business Review, the NextGen category of the Game Changer Award is given to the company with the most revolutionary up-and-coming robotics products. The RTU was selected for this honor by a distinguished panel consisting of experts from the International Journal of Advanced Robotic Systems, the business and investment community, and editors from Robotics Business Review and Robotics Trends. The award was presented to Wynright October 23, 2013 during a banquet at the RoboBusiness event in Santa Clara, California.
"While much of the warehouse or distribution center has been automated, the last mile - the loading dock - still remains a largely manual operation in the supply chain," said Kevin Ambrose, CEO of Wynright Corporation. "Much of that has to do with the number of variables encountered when loading or unloading a truck. Most robots are designed for a single, repetitive task. Our goal was to develop a self-propelled robotic unit that could recognize variables such as size, shape and how products are stacked in a trailer or sea container, and make intelligent decisions about the best way to take them off the stack and place them on a conveyor. This award is further validation that what we're doing is both unique and valuable to our customers."
One of the keys to the success of Wynright's RTU is its innovative use of 3D vision technology - the same type used in video games such as Xbox Kinect. When the RTU approaches a wall of cartons it scans the façade in three dimensions and then uses an algorithm to determine the best way to grip and move the carton onto a conveyor, where it can be introduced into the rest of the material handling system.
Wynright designed the RTU so a single operator can manage up to three units simultaneously. The operator need only be present to get the RTU started, and to solve any problems the unit cannot solve for itself, such as handling a carton that was damaged in transit. When this occurs, the RTU alerts the operator who then returns to the dock to resolve the situation. Use of the RTU helps reduce labor costs while giving dock workers a higher-paying, more valuable skill. It also improves working conditions on the dock.
"Loading and unloading trailers and containers is uncomfortable, difficult work for human beings," Ambrose said. "Since there are no environmental controls, it can get incredibly hot during a Texas summer or incredibly cold in a Montana winter. It's also very difficult on the legs, shoulders and back. But the work still has to get done. The RTU allows enterprises to redeploy dock personnel to other, less taxing jobs, thereby creating a better, safer work environment while still ensuring a smooth flow of goods through the system."
About Wynright Corporation
Wynright Corporation, a wholly owned subsidiary of Daifuku Webb, is a leading provider of intelligent material handling systems. With more than 200 engineers in-house, the company designs, manufactures, integrates and installs a full spectrum of intralogistics solutions, offering both Wynright-branded and third-party equipment to meet client needs. These include leading-edge conveyor and sortation systems, voice- and light-directed order fulfillment equipment, a suite of warehouse controls & execution software, robotics, mezzanines, and structures, all backed by critical round-the-clock service and support.
Since its founding in 1972, Wynright has been a trusted partner to some of the world's largest and fastest-growing companies, showing them how to use their space more efficiently to deliver improved productivity, today and tomorrow.
About Daifuku Webb Holding Company
Daifuku Webb Holding Company, a subsidiary of Daifuku Co. Ltd., is a leading developer of innovative material handling technology such as Automatic Guided Vehicles (AGVs), Automated Storage and Retrieval Systems (AS/RS), conveyors, baggage handling systems, bulk handling systems, cleanroom systems and airport maintenance services. It includes Daifuku America Corporation, Jervis B. Webb Company, Elite Line Services and Logan Teleflex, Inc. Daifuku Webb specializes in the design, engineering, manufacturing, installation and service of integrated systems used in the automotive, airport, semiconductor, LCD equipment, food/beverage, bulk, warehousing and manufacturing industries. Daifuku Webb Holding Company is headquartered in Farmington Hills, Mich., with manufacturing locations throughout North America.
Featured Product
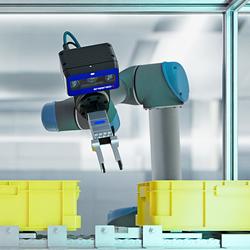
3D Vision: Ensenso B now also available as a mono version!
This compact 3D camera series combines a very short working distance, a large field of view and a high depth of field - perfect for bin picking applications. With its ability to capture multiple objects over a large area, it can help robots empty containers more efficiently. Now available from IDS Imaging Development Systems. In the color version of the Ensenso B, the stereo system is equipped with two RGB image sensors. This saves additional sensors and reduces installation space and hardware costs. Now, you can also choose your model to be equipped with two 5 MP mono sensors, achieving impressively high spatial precision. With enhanced sharpness and accuracy, you can tackle applications where absolute precision is essential. The great strength of the Ensenso B lies in the very precise detection of objects at close range. It offers a wide field of view and an impressively high depth of field. This means that the area in which an object is in focus is unusually large. At a distance of 30 centimetres between the camera and the object, the Z-accuracy is approx. 0.1 millimetres. The maximum working distance is 2 meters. This 3D camera series complies with protection class IP65/67 and is ideal for use in industrial environments.