Lincoln Electric Dedicates New Automation Center of Excellence in Brazil
The new, 5,000-square-meter facility includes demonstration, integration, training and office space.
Last week, the Cleveland-based Lincoln Electric Company opened its new Automation Center of Excellence - Brazil before a large group of customers, supplier partners and employees. A welcome was extended by Reinaldo Nogueira, Mayor of the city of Indaiatuba, who stressed the importance of creating an environment for businesses to grow and in which their employees could feel comfortable making their home.
The new, 5,000-square-meter facility includes demonstration, integration, training and office space. The training lab has six robot systems, as well as a station for orbital welding process development and system instruction. There are eight additional demonstration systems for robotic and mechanized applications. Classroom instruction can hold up to 40 students in two classrooms.
The keynote presentation defining Lincoln Electric's automation strategy was delivered by George Blankenship, President of Lincoln Electric's North American operations. He stated that the Company recognizes that its customers must deliver higher productivity and improved quality to remain competitive.
"Our responsibility to our customer must be more than just a provider of product. Their expectations of us are greater today because they have escalated demands from their customer," Blankenship said. "When we can improve their welding and fabrication process, we become a partner rather than a vendor."
Lincoln Electric has strategically grown its Automation Solutions offerings over the last several years, both organically and through acquisition. Leveraging its position as "the Welding Experts," it has grown its portfolio to include pre-engineered robotic systems, CNC plasma cutting and controls, fixturing and tooling, engineered line builds, robotic integration, laser systems, weld fume control and fire prevention.
"We can say with confidence that Lincoln Electric is the only company that has the ability to deliver this complete of an automation solution to our customers," said Chris Bailey, Director of Automation - North America. "The opening of this new facility in Brazil demonstrates our ability to bring these solutions to our customers' doorstep throughout the world and where they need us."
Leonardo Sabedot, Business Manager for the ASG-Brazil group, closed out the presentation by thanking his team and partners for making the facility a world-class facility.
"We are excited by the opportunity that this facility represents, and look forward to forging strong partnerships with the many customers in the region," Sabedot said.
Lincoln Electric is the world leader in the design, development and manufacture of arc welding products, robotic arc welding systems, plasma and oxyfuel cutting equipment and has a leading global position in the brazing and soldering alloys market. Headquartered in Cleveland, Ohio, Lincoln Electric has 45 manufacturing locations, including operations and joint ventures in 19 countries and a worldwide network of distributors and sales offices covering more than 160 countries. For more information about Lincoln Electric and its products and services, visit the company's website at www.lincolnelectric.com.
Featured Product
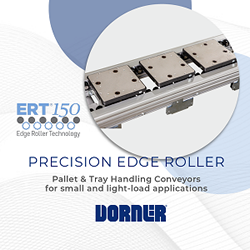
The ERT150 - Dorner's Next Evolution of Edge Roller Technology Conveyors
The next evolution in Dorner's Edge Roller Technology conveyor platform, the ERT®150, is ideal for small and light-load assembly automation, as well as medical and medical-device assembly application. The ERT platform is the only pallet conveyor of its kind available with an ISO Standard Class 4 rating for cleanroom applications. Earning the ISO Standard 14644-1 Class 4 rating means Dorner's ERT150 will conform and not contribute to the contamination of cleanrooms to those standards. As implied by its name, the ERT150 (Edge Roller Technology) uses rollers to move pallets through the conveyor smoothly with no friction (a byproduct often seen in belt-driven platforms). The conveyor's open design eliminates concerns of small parts or screws dropping into rollers and causing conveyor damage or jamming. The ERT150 is suited to operate in cleanroom environments requiring a pallet handling conveyor. It is capable of zoning for no or low-back pressure accumulation and is ideal for automation assembly applications within industries including medical devices, electronics, consumer goods among others.