Automation platform CPX from Festo helps achieve goal of integrated industry
An important milestone on the road towards Integrated Industry is the concept of integrated automation from Festo.
"Integrated Industry - NEXT STEPS" is the main theme of the Hanover Fair 2014. Automation is getting ever closer to the objective of workpieces that control their own production. An important milestone on the road towards Integrated Industry is the concept of integrated automation from Festo - based on the automation platform CPX. This is now available with important additions which facilitate networked communication and even more flexibility.
How does automation technology support the goal of a "smart factory", one which is networked and integrated? Step by step, the machines, plant, workpieces and components in production processes are moving ever closer to a future in which they will be able to exchange data and messages in real time. Previous rigid central factory control systems are giving way to decentralised intelligence.
Automation platform CPX
Integrated Industry is characterised by the networking-together of the components within a production system, a continuous exchange of data, the combination of the evaluation of various sensor signals and a facility for the detection of complex events and independent local decision-making and control. The concept of integrated automation based on the automation platform CPX incorporates some trailblazing ideas.
This electrical terminal for valve terminals already offers more than just a means of linking the field and master control levels. It has diagnostic capabilities and can provide condition monitoring functions. Its individual modules already make it possible to integrate the control of pneumatic cylinders via the modular valve terminals MPA and VTSA together with motion controllers for electric drives. The CPX concept also includes safety functions.
This makes it possible to access diagnostic information, locate faults quickly and replace modules. Examples of the integration of functions include IT services such as web servers, a front end controller for decentralised local control, an end-position controller and a proportional valve or pressure sensor for detecting internal valve terminal pressures or external signals.
Full fieldbus flexibility
Already today CPX can integrate all commonly-used bus systems and Industrial Ethernet protocols. Pointing the way to the future is, for example, the Sercos III fieldbus node (CPX-FB39), which is available right now. According to a recent study, the proportion of Ethernet-based fieldbus systems in which Sercos III is used is set to more than double. Sercos III is perceived as a system which is not dominated by a single supplier. What is more, it is able as standard to handle motion control and I/O control functions via the same bus.
Further proof of the flexibility of the automation platform CPX: the new fieldbus node CPX-FB40 expands the CPX fieldbus portfolio by adding the Industrial Ethernet protocol "Powerlink". This offers a direct valve terminal interface for Powerlink systems. The CPX concept from Festo is thus shown once again to be an automation platform which is independent of any particular fieldbus system.
Data transparency
With the counter and measuring module CPX-2ZE2DA, also available with the high protection class IP65, the automation platform CPX ensures greater transparency for the data from a machine or plant. Its functions are extensive: pulse counters for one-off, periodic and infinite counter and facilities for speed measurement, frequency measurement, period duration measurement, positioning (incremental and absolute encoders) and the control of simple 24V DC motors are integrated economically and conveniently into a single module.
Used, for example, with a rotary indexing table with various pick & place stations, the counter and measuring module is able to detect positions, position the gripper arm, measure the speed of a feed unit or measure the angle during the positioning of a workpiece. This is achieved with the aid of rotary encoders which convert mechanical movements into electrical signals. Incremental signal generators produce pulses, which can be counted in order to measure speed, length or position. In absolute signal generators, each position corresponds to a defined code pattern, which means that the actual position can be detected even after a power failure as soon as power is restored. The CPX counter and measuring module interprets the electrical signals and processes these further.
Clear and simple
This means that CPX is well-equipped for the future. Instead of innumerable bus systems, there will in the future be only one world-wide standardised Internet protocol, running on a real-time-capable WLAN or Ethernet.
This trend towards simplicity is based on the same philosophy as the new adaptive and intelligent installation platforms. Until now, if there was some change to the product, parts of the production installation needed to be modified. The new highly adaptive installations, however, will adapt automatically to future product modifications. There will be no need for discussions about machine setting times in the factory of the future. The automation platform CPX from Festo with its modularity is already making life simpler for users today.
How does automation technology support the goal of a "smart factory", one which is networked and integrated? Step by step, the machines, plant, workpieces and components in production processes are moving ever closer to a future in which they will be able to exchange data and messages in real time. Previous rigid central factory control systems are giving way to decentralised intelligence.
Automation platform CPX
Integrated Industry is characterised by the networking-together of the components within a production system, a continuous exchange of data, the combination of the evaluation of various sensor signals and a facility for the detection of complex events and independent local decision-making and control. The concept of integrated automation based on the automation platform CPX incorporates some trailblazing ideas.
This electrical terminal for valve terminals already offers more than just a means of linking the field and master control levels. It has diagnostic capabilities and can provide condition monitoring functions. Its individual modules already make it possible to integrate the control of pneumatic cylinders via the modular valve terminals MPA and VTSA together with motion controllers for electric drives. The CPX concept also includes safety functions.
This makes it possible to access diagnostic information, locate faults quickly and replace modules. Examples of the integration of functions include IT services such as web servers, a front end controller for decentralised local control, an end-position controller and a proportional valve or pressure sensor for detecting internal valve terminal pressures or external signals.
Full fieldbus flexibility
Already today CPX can integrate all commonly-used bus systems and Industrial Ethernet protocols. Pointing the way to the future is, for example, the Sercos III fieldbus node (CPX-FB39), which is available right now. According to a recent study, the proportion of Ethernet-based fieldbus systems in which Sercos III is used is set to more than double. Sercos III is perceived as a system which is not dominated by a single supplier. What is more, it is able as standard to handle motion control and I/O control functions via the same bus.
Further proof of the flexibility of the automation platform CPX: the new fieldbus node CPX-FB40 expands the CPX fieldbus portfolio by adding the Industrial Ethernet protocol "Powerlink". This offers a direct valve terminal interface for Powerlink systems. The CPX concept from Festo is thus shown once again to be an automation platform which is independent of any particular fieldbus system.
Data transparency
With the counter and measuring module CPX-2ZE2DA, also available with the high protection class IP65, the automation platform CPX ensures greater transparency for the data from a machine or plant. Its functions are extensive: pulse counters for one-off, periodic and infinite counter and facilities for speed measurement, frequency measurement, period duration measurement, positioning (incremental and absolute encoders) and the control of simple 24V DC motors are integrated economically and conveniently into a single module.
Used, for example, with a rotary indexing table with various pick & place stations, the counter and measuring module is able to detect positions, position the gripper arm, measure the speed of a feed unit or measure the angle during the positioning of a workpiece. This is achieved with the aid of rotary encoders which convert mechanical movements into electrical signals. Incremental signal generators produce pulses, which can be counted in order to measure speed, length or position. In absolute signal generators, each position corresponds to a defined code pattern, which means that the actual position can be detected even after a power failure as soon as power is restored. The CPX counter and measuring module interprets the electrical signals and processes these further.
Clear and simple
This means that CPX is well-equipped for the future. Instead of innumerable bus systems, there will in the future be only one world-wide standardised Internet protocol, running on a real-time-capable WLAN or Ethernet.
This trend towards simplicity is based on the same philosophy as the new adaptive and intelligent installation platforms. Until now, if there was some change to the product, parts of the production installation needed to be modified. The new highly adaptive installations, however, will adapt automatically to future product modifications. There will be no need for discussions about machine setting times in the factory of the future. The automation platform CPX from Festo with its modularity is already making life simpler for users today.
Featured Product
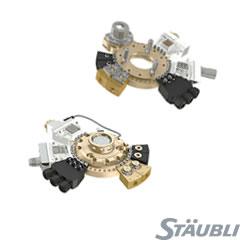