ABB Robotics hosts over 1,000 at Technology Days 2014, featuring over 80 demos and seminars on latest innovations.
Event also highlighted major ABB developmental milestones since 1974, celebrating 40 years of industry leadership.
AUBURN HILLS, Mich. (March 25, 2014) - ABB Robotics hosted over 1,000 attendees at its annual Technology Days event March 13th and 14th, 2014 at its North American headquarters and training center in Auburn Hills, Michigan. The event featured 80+ product demonstrations and free technical seminars covering both general and application specific information designed to benefit both those considering an initial foray into robotic automation, and those looking to upgrade or expand their existing robotic lines.
The attendees included current and potential customers, value providers, affiliated technology equipment providers, members of the media, and for the Friday afternoon Open House, a fascinated crowd of children, friends and robot enthusiasts of all ages.
Robotic application highlighted on the demo floor and in the seminars included packaging, material handling, assembly, machine tending, welding and cutting, press automation, painting, automotive and transportation, and training and service. ABB also celebrated 40 years in the robotics industry, highlighting major technological development milestones since 1974.
Prominent features on the demo floor included the new IRB 6700, the next generation of large robots, designed for spot welding, material handling and machine tending; several sophisticated machine tending cells; and the full IRB 360 FlexPicker line, the leading Delta robot in the industry recently expanded with several higher payload models. ABB's new Integrated Vision, Integrated Force Control and advanced RobotStudio programming systems were also on display.
The ABB Dual Arm Concept Robot (DACR) made its first appearance in North America, providing a look at the current status of a robot prototype designed to meet the challenging demands of the consumer electronics industry and other smaller parts assembly applications.
About ABB
ABB (www.abb.com) is a leader in power and automation technologies that enable utility and industry customers to improve their performance while lowering environmental impact. The ABB Group of companies operates in around 100 countries and employs about 150,000 people.
About ABB Robotics
ABB Robotics (www.abb.com/robotics) is a leading supplier of industrial robots - also providing
robot software, peripheral equipment, modular manufacturing cells and service for tasks such as welding, handling, assembly, painting and finishing, picking, packing, palletizing and machine tending. Key markets include automotive, plastics, metal fabrication, foundry, electronics, machine tools, pharmaceutical and food and beverage industries. A strong solutions focus helps manufacturers improve productivity, product quality and worker safety. ABB has installed more than 200,000 robots worldwide.
Featured Product
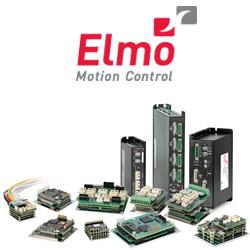