Michigan Manufacturing Success Story
EMP Utilizes ATI Tool Changers in Product Changeover Tooling
Engineered Machined Products (EMP), based in Escanaba Michigan, is a leading producer of machined components and energy saving systems. Like most manufacturers, EMP felt the difficult blows of the recession in 2009. Even after implementing robots and automation, EMP faced an onslaught of competition from low-cost labor markets. Brian Larche, EMP owner, and his manufacturing team in Escanaba were able to adapt the company's CNC and automation equipment to meet new customer needs. This proved to be the key in turning things around.
To facilitate these new customers, EMP required a robotic system utilizing five different robotic end-of-arm (EOA) tools to work with many different products and loading orientations. The robotic work cell needed to be changeover-friendly on the CNC side and be capable of fully automatic tool changes. Each EOA tool weighed approximately 350lbs, requiring an extremely accurate placement of the part, and had to work 24 hours a day in a challenging environment. Previous successes with ATI Industrial Automation products lead EMP to choose ATI's QC-110 Robotic Tool Changer for their automated changeover process. ATI Robotic Tool Changers have proven instrumental in the work cell's success, enabling quick, automatic, and safe exchange of changeover tooling. This allowed EMP to add new product families to their shop and helped them provide customers with the highest quality product at competitive pricing.
Successful manufacturing has many challenges. Utilizing ATI Robotic Tool Changers can greatly improve the flexibility and productivity of automated work cells. ATI Industrial Automation offers a wide variety of Tool Changer models and can design custom units engineered to your specific needs. ATI Robotic Tool Changers have proven themselves valuable at companies like EMP. Come see how ATI products can help your business succeed.
Featured Product
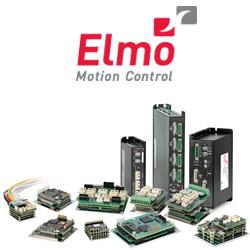