ABB RobotStudio Picking PowerPac simplifies the design and programming of complex robotic pick-and-pack systems
The new software improves the performance of robotic picking lines by identifying potential risks and optimizing cell designs with accurate 3D simulations
AUBURN HILLS, Mich. (April 28, 2014) - ABB Robotics has introduced the Robot Studio Picking PowerPac, which combines two prominent ABB software technologies - RobotStudio and PickMaster 3 - into a single bundle, greatly simplifying both the design and programming of complex robotic picking-and-packing systems.
The RobotStudio Picking PowerPac boosts the performance of picking lines, allowing systems to be optimized in the 3D virtual world before being built in the real world, with the risks in designing picking lines - such as the variations in the product inflow - thoroughly tested and refined before costly mistakes are made on the production line. The software allows for the improvement of existing lines configured using PickMaster 3 by recording current product flow with cameras and then feeding them into the Picking PowerPac for validation and optimization.
"As a company we put a lot of effort into creating solutions that are truly innovative and address real needs among our customers," says ABB Product Manager Klas Bengtsson. "With the Picking PowerPac, we have combined the precision, power and reliability found in all ABB Robotics software with the ease-of-use and simulation capabilities of RobotStudio."
The Picking PowerPac software bundle allows users to configure the product conveyors, pick and place locations, gripper functionality, definition of each product to be handled, and configuration of all products and components included in the picking system. Once the cell configuration is complete, the new software provides a fully functional picking cell simulation with accurate robot performance information. The complete RobotStudio model is then ready to be transferred directly to the robot controller for cell operation.
"The Picking PowerPac allows systems integrators and end users alike the ability to easily design and develop picking simulations that will eventually run in the real world. All of the system adjustments in PickMaster 3 are available in this add-in, to accurately optimize single and multiple robot picking simulations," adds Rick Tallian, ABB packaging products and applications manager.
The new software will be especially effective in programming the high speed picking and packing IRB 360 FlexPicker robot, the most widely used Delta robot in the industry. The IRB 360 family now includes variants with payloads of 1 kg, 3 kg, 6 kg and 8 kg and reaches of 800 mm, 1130 mm and 1600 mm.
Visit www.abb.com/robotics for further information.
Featured Product
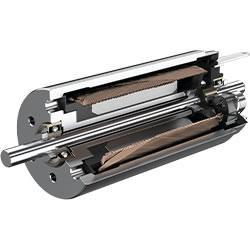
FAULHABER MICROMO - Game changer in logistics
Faster, more efficient, more sustainable - due to global competition in industry combined with booming online trade, transport structures in intralogistics are facing new challenges. The industries' answer: Automation. From storage to shipping, key work steps are being taken over by intelligent logistics robots, such as automatic storage and retrieval machines and driverless transport systems. To work efficiently and reliably around the clock, these robots need flexible and particularly compact drive solutions.