Shimpo Drives announces its new STH servo-driven rotary actuator
Shimpo Drives announces its new STH servo-driven rotary actuator. The STH is a mid-performance rotary actuator that sets a new price/performance point in rotary positioning.
Shimpo Drives announces its new STH servo-driven rotary actuator. The STH is a mid-performance rotary actuator that sets a new price/performance point in rotary positioning.
A Shimpo Able servo reducer is the interface between the servo motor and STH output actuator. The Able gearbox features simple mounting of nearly any small to medium servo motor and gives the complete STH package net ratios ranging from 12:1 through 324:1.
STH's very large crossed roller output bearing allows for impressive thrust loads and tilting moments. A generous hollow through-bore allows wiring or tubing to be passed through to effectors, fillers, or other active machinery.
Features include:
• 85 mm pass-through hole allows use of air lines or wiring
• Input is compatible with most servo motor brands
• Available ratios range from 12:1 through 324:1
• Shipped from stock
For more information on the STH Rotary Stage series from Shimpo, click on the link below:
https://www.servo2go.com/product.php?ID=105503&cat=
For more information, please contact:
Editorial Contact:
Warren Osak
sales@servo2go.com
Toll Free Phone: 877-378-0240
Toll Free Fax: 877-378-0249
www.servo2go.com
Tags: Shimpo, Shimpo Drives, Rotary Stage, Rotary Table, Servo2Go
Featured Product
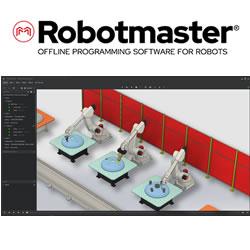
Robotmaster® 2024
Program multi-robot cells and automatically solve robotic errors with ease. Hypertherm Associates announces a new version to its robotic programming software. Robotmaster 2024 addresses key market trends including the support for programming multiple robots in a single work cell and the demand for automatic trajectory optimization and robotic error correction.