Davron Indexing Conveyor Oven Halves Time Needed for Preheating Cycle
Davron Technologies, Inc. announces the design and manufacturing of the DTI-1138, an indexing conveyor oven that uses both electricity and natural gas to preheat automotive carpet and pads.
Chattanooga, Tennessee July 09, 2014
Davron Technologies, Inc. designed and manufactured the DTI-1138, an indexing conveyor oven that uses both electricity and natural gas to preheat carpet and pads for a Tier 1 automotive supplier. Prior to commissioning the DTI-1138, the customer preheated carpet and pads in two separate ovens. The DTI-1138 indexing conveyor oven enables Davrons customer to preheat carpet and pad simultaneously in the same oven so that a complete vehicle set can be preheated in as little as 30 seconds — a 100 percent increase over the previous process.
The DTI-1138 includes two individual heated chambers. The upper chamber features a flat wire belt conveying system with a decline conveyor. This chamber is heated by a natural gas burner and preheats pads via forced air convection. The lower chamber has an automated shuttle table that conveys carpet blanks into the heated chamber and utilizes infrared panels arranged in individual zones of control to allow for variation of heating across the entire surface of the carpet. After a pad is loaded onto the upper conveying system, the pad is indexed one position into the heated chamber. At the same time, on the exit end of the system, a carpet blank is loaded onto the shuttle table and is conveyed into the heated chamber in the lower tier of the oven. Once preheated, the carpet and pad each index one more position, exiting the oven simultaneously. They are then matched together to form a preheated vehicle set ready to be press formed as a single unit.
The upper convection chamber of the DTI-1138 indexing conveyor oven can operate between 300ᴼ and 450ᴼF, while the lower infrared chamber can operate between 200ᴼ and 800ᴼF. Product can be placed onto the conveying systems and shuttled with an automated pick-and-place system or loaded manually by operators. The DTI-1138 features PLC control and all motion functions are controlled by servo for accuracy and speed.
The usable dimensions of both heated chambers are 173" wide x 80" long. The interior of the oven is made out of 16-gauge aluminized steel backed by six inches of eight-pound density mineral wool insulation. The exterior is constructed of 16-gauge carbon steel backed by a structural steel frame and finished with high- temperature paint. The lower chamber features a removable drawer that houses the infrared panels. This drawer slides out of the oven to allow access to the IR panels for maintenance. The upper chamber includes two access doors on each side to provide access for maintenance and ensure compliance with NFPA requirements.
Davron designed the DTI-1138 indexing conveyor oven based on two criteria provided by the customer: the target production rate per hour and the temperature required to preheat. Once the indexing conveyor oven was manufactured, Davron did acceptance testing and training with the customer at Davron headquarters in Chattanooga, Tenn., prior to shipment. Davron then went on site to install the oven at the customers facility.
Visit http://www.davrontech.com for more information about Davrons indexing conveyor oven capabilities. Or, if youd like to discuss your own industrial oven project, please call Davrons Vice President, Jimmy Evans, at (888) 263-2673, or fill out our Contact form online.
About Davron Technologies, Inc.
Davron Technologies, Inc. custom fabricates industrial ovens, providing turnkey design and system integration services to develop thermal processing solutions. Davron is a total industrial oven manufacturer, creating custom industrial ovens and precision process equipment for every industry that requires thermal processing. Each Davron industrial oven is custom built according to customers unique specifications. As the Provider of Industrial Oven Solutions, Davron offers one of the largest selections of in-house and on-site industrial oven services in the world.
Featured Product
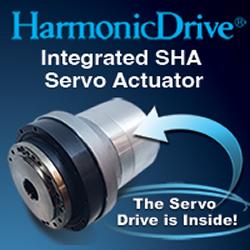
Harmonic Drive - Coming Soon! Integrated Actuators with EtherCAT®!
The IDT Series is a family of compact actuators with an integrated servo drive with
CANopen® and, coming soon, EtherCAT® . With high torque, exceptional
accuracy and repeatability, these actuators eliminate the need for an external drive and
greatly simplify cabling.