HHI Develops New Robotic Welding Process for Building Offshore Facilities
Hyundai Heavy Industries Co., Ltd. (HHI), the worlds biggest shipbuilder and a leading offshore facilities contractor, announced today that it developed a new automatic welding process for building offshore facilities.
The new hot-wire TIG (Tungsten Inert Gas) robot welding process combines conventional hot-wire TIG welding with the 6-axis robot which HHI independently developed. The robot is six times faster than manual welding as it can continuously supply more welding wires. Also, it features a remote control system to enhance work efficiency.
HHI will apply this automatic welding to special pipes, made of duplex and super duplex stainless steel, to build offshore facilities such as FPSOs and offshore platforms under construction at its offshore yard from this month.
Featured Product
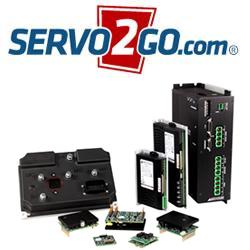
High Performance Servo Drives for localized and distributed control applications from Servo2Go.com
Engineered to drive brushless and brush servomotors in torque, velocity or position mode, Servo2Go.com offers a broad selection of servo drives in a wide range of input voltages and output power levels.