EOS North American User Day (NAUD) Highlights Industrial 3D-Printing Success Stories and is Open to All IMTS Attendees
Boeing, GE Aviation, and Honeywell Aerospace are among presenters at event
Aerospace industry titans Boeing, GE Aviation, and Honeywell Aerospace are among those documenting the strong case for end-use production with laser sintering, an industrial 3D-printing technology from EOS, the technology and market leader for design-driven solutions in Additive Manufacturing (AM).
By speaking during the North American User Day (NAUD) on September 10, 2014 they, along with other customers and partners, will chronicle their successes applying AM for product manufacturing.
The NAUD takes place during the International Manufacturing Technology Show (IMTS) held the week of September 8, 2014, at McCormick Place in Chicago, Ill. This is the first time the NAUD is being held at IMTS—and the first time the full-day event is open to all show attendees.
"IMTS is an ideal venue to demonstrate how Additive Manufacturing fits in with existing subtractive technologies as part of a process chain," says Andrew Snow, senior vice president, EOS of North America, Inc. "Historically, EOS has held the NAUD to better serve and educate our customer base. Now, opening the presentations to everyone also provides all IMTS attendees the opportunity to network with experts, industry leaders, and each other—to learn about the roadmap ahead and the success of early and current industrial 3D-printing adopters."
"Events like the NAUD are instrumental in educating manufacturers about Additive Manufacturing and helping fast-track it onto the production floor alongside traditional processes," says Ed Morris, director of America Makes, the National Additive Manufacturing Innovation Institute. "As organizations recognize the competitive advantage this technology offers—everything from optimized product designs to value optimization through streamlined supply chains and reduced inventories—we want to help them accelerate their implementation of this innovative technology."
Morris is also part of the speaker lineup at the NAUD and joins other industry pioneer presenters, including AMT-Association for Manufacturing Technology, 3D MicroPrint, Shapeways, Linear Mold & Engineering, Oxford Performance Materials, and Within Technologies.
The NAUD is being held in the West Hall in room W-181 Ground Level of McCormick Place. In addition to the presentations, the user day will include a cocktail reception and an anniversary toast in celebration of EOS 25th year in business. For more information about the NAUD and to register, visit http://www.imts.com/education/conference_EOS.html.
During IMTS, EOS will also demonstrate one of their latest direct metal laser-sintering (DMLS™) systems, the EOS M 290, in the North Hall, booth N-7061. The M 290 processes a variety of metals including titanium, cobalt chrome, stainless steel, aluminum, and nickel alloys.
About EOS
Founded in 1989, EOS is the technology and market leader for design-driven, integrated e-Manufacturing solutions in Additive Manufacturing (AM), an industrial 3D-printing process. EOS offers a modular solution portfolio including systems, software, materials as well as services including specific application consulting. As an industrial manufacturing process, it allows the fast and flexible production of high-end parts based on 3D CAD data at a repeatable industry level of quality. As a disruptive technology, it paves the way for a paradigm shift in product design and manufacturing. It accelerates product development, offers freedom of design, optimizes part structures, and enables lattice structures as well as functional integration. As such, it creates significant competitive advantages for its customers. For more information please visit www.eos.info.
Featured Product
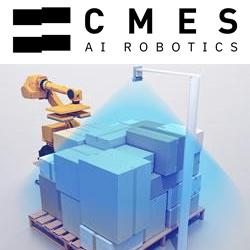
CMES - AI-Powered 3D Robot Vision
Powered by AI, CMES Robotics enables 3D vision for factory robots. CMES AI vision software enables robots to recognize unstructured, flexible, or deformed objects, pick them up, and loading and unloading. CMES Vision software has been deployed worldwide for random palletization and depalletization along with void filling applications. CMES Robotics automates your warehouse, logistics, and supply chain. For more information, please visit: cmesrobotics.com or email info@cmesrobotics.com.