Microscan Launches Verification Monitoring Interface (VMI) to Grade Barcodes and Monitor Trends in Quality in Real Time
Microscan, a global technology leader in barcode, machine vision, and lighting solutions, announces the availability of the Verification Monitoring Interface (VMI), a new software solution specially engineered for monitoring the quality of barcodes as they are produced on parts, labels, and packaging.
RENTON, WA, September 11, 2014 - Microscan, a global technology leader in barcode, machine vision, and lighting solutions, announces the availability of the Verification Monitoring Interface (VMI), a new software solution specially engineered for monitoring the quality of barcodes as they are produced on parts, labels, and packaging.
Unreadable barcodes can lead to costly scrap, downtime, and errors in the supply chain and at the point of sale. This is why more and more retailers are issuing mandates to their suppliers regarding minimum barcode quality, which leaves suppliers facing possible fines for unreadable codes and disqualification for non-compliance. Microscan has developed easy-to-use verification solutions to meet the need for inline (directly after products are marked) and offline verification to ISO and AIM barcode quality standards, even in high-speed applications, to help manufacturers meet customer demands and ensure efficiency throughout the supply chain. These solutions are tailored to meet ISO and AIM requirements and combine Microscan machine vision technology, including Vision HAWK smart camera models, NERLITE® industrial lighting, and AutoVISION® Machine Vision Software.
The new VMI software plug-in provides a custom Runtime window in AutoVISION Machine Vision Software for visualizing the results of ISO barcode quality verification as well as fluctuations in barcode quality over time. As VMI operates on the production line, manufacturers can use this live data about their barcodes to set alarms or trigger actions based on low barcode quality, which may indicate degradation of the printing or marking system such as jammed print heads, low ink, and more. By implementing barcode verification as a preventative measure, and with VMI running in real time as products are marked and labeled, poor and unreadable codes are prevented from entering the supply chain. Thanks to the solution, manufacturers can greatly improve product quality, operational efficiency, reduce scrap and unplanned downtime, and avoid costly fines associated with poor or non-compliant barcodes.
For more information on Microscan's new Verification Monitoring Interface (VMI) and AutoVISION Machine Vision Software, visit www.microscan.com.
About Microscan
Microscan is a global leader in technology for precision data acquisition and control solutions serving a wide range of automation and OEM applications. Founded in 1982, Microscan has a strong history of technology innovation that includes the invention of the first laser diode barcode scanner and the 2D symbology, Data Matrix. Today, Microscan remains a technology leader in automatic identification and machine vision with extensive solutions for ID tracking, traceability and inspection ranging from basic barcode reading up to complex machine vision inspection, identification, and measurement.
As an ISO 9001:2008 certified company recognized for quality leadership in the U.S., Microscan is known and trusted by customers worldwide as a provider of quality, high precision products. Microscan is a Spectris company.
Microscan Contact
Corporate Headquarters, U.S.
Shaina Warner, Marketing Specialist
+1-425-203-4963; swarner@microscan.com
European Headquarters, The Netherlands
Mrs. Kirsi Rolf, Marketing Manager EMEA
+31 6 100 74598; KRolf@microscan.com
Featured Product
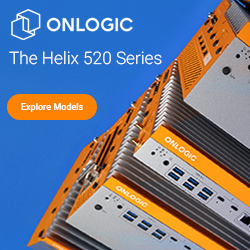