G10 Photoelectric Sensor Can Be Mounted and Aligned in Seconds
The G10 is a cost-effective sensor that can be mounted and aligned in less than 10 seconds, drastically reducing commissioning and installation time.
SICK, one of the worlds leading manufacturers of sensors, safety systems, machine vision, encoders and automatic identification solutions for factory and logistics automation, today announced the launch of the G10 photoelectric sensor with Q-Lock mounting. The G10 is a cost-effective sensor that can be mounted and aligned in less than 10 seconds, drastically reducing commissioning and installation time.
The G10 incorporates precise PinPoint LED technology to ensure simple alignment and reliable object detection at sensing distances up to 1,200 mm with background suppression. Since no reflector is required, installation time is reduced. An easy-to-use potentiometer and bright 360° indicator LEDs ensure easy adjustment and status monitoring. In addition, universal DC and AC/DC power supplies provide even greater application flexibility.
The G10 is a complete product family that features a wide range of cables, reflectors and mounting accessories. It provides reliable detection regardless of dust, dirt, humidity and extreme temperatures, making it ideal for a variety of logistics and machine building applications.
About SICK
SICK is one of the worlds leading manufacturers of sensors, safety systems, machine vision, encoders and automatic identification products for industrial applications. With more than 1000 patents, SICK continues to lead the industry in new product innovations. The diversity of its product line allows SICK to offer solutions at every phase of production in the logistics, automotive, packaging, electronics, food and beverage, and material handling markets. SICK AG was founded in 1946 and has operations or representation in 65 countries worldwide.
Featured Product
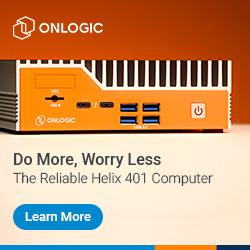
OnLogic Helix 511 Fanless Intel 12th Gen Edge Computer
OnLogic's Helix 511 Fanless Edge computer delivers ultra-reliable, fanless computing using Intel® 12th Generation performance hybrid processing. The Helix 511 is a versatile fanless computer capable of powering solutions including advanced automation, light detection and ranging (LiDAR), access control & building automation, or virtually any other IoT or edge gateway functionality needed, with support for 4 simultaneous serial connections. The system is able to reliably operate in temperatures ranging from 0 to 50°C, can accept power input ranging from 12 to 24 Volts, and is Wall, VESA and DIN rail mountable.