Kurion's Innovative Robotics Technology is Tapped to Address Critical Reactor Repair Issues at Fukushima Daiichi Nuclear Power Plant
Project Follows Kurions Successful Deployment of a Robotic System to Inspect Reactor Containment Damage
Irvine, Calif., Westminster, Colo. - Jan. 14, 2014: Kurion, Inc., an innovator in nuclear and hazardous waste management, announced it was awarded a contract to develop an advanced robotic arm to repair reactor primary containment leaks within the damaged Fukushima Daiichi Nuclear Power Plant. Through a contract with Japanese industry leader IHI Corporation, Kurion will begin producing the robotic system, the Fukushima Repair Manipulator (FRM), for a targeted deployment of mid-2016 within the Unit 2 Reactor.
"Kurion is honored to be selected yet again to assist with the ongoing recovery efforts at the Fukushima Daiichi Nuclear Power Plant," said John Raymont, Kurion founder and president. "For the past three years, Kurion has applied our innovative technologies throughout the plant to purify hazardous water and identify repair needs. Now, the adoption of Kurions Fukushima Repair Manipulator marks another critical step in accelerating the ongoing cleanup of the plant."
The Fukushima Repair Manipulator represents the second phase of the reactor primary containment leak discovery and repair efforts. This summer Kurion assisted in the first phase with the development and delivery of the Fukushima Inspection Manipulator (FIM), a robotic system tasked with searching for the causes of the leaks.
The Fukushima Inspection Manipulator deployed three remotely operated vehicles (ROVs) to identify cracks in the primary containment vessel, vent tubes and torus located in the reactor building. The first inspection was completed ahead of schedule and produced the necessary information to move forward with the second phase of the repair efforts. The FIM is inspecting an additional seven locations in the reactor building and is scheduled to complete this task in March 2015. The information gathered will be used to refine the FRM design requirements and identify the full scope of repair activities.
The primary objective of the Fukushima Repair Manipulator will be to plug leaks caused by the devastating tsunami that damaged the Fukushima Daiichi Nuclear Power Plant in March 2011. Using cutting-edge robotics technology, the system will grant plant workers unprecedented access to the reactor to open holes, clear debris and obstacles, and plug cracks in the reactors vent tubes and torus - all from the safety of the remote operating station. Kurions sophisticated system will include a robotic arm outfitted with advanced cutting, water-jet and grouting tools; and will feature new automatic control sequences to guide these complex tasks.
"Access to radioactive and hazardous environments is a crucial piece of the waste management puzzle," said Kurion CEO Bill Gallo. "Each project is unique, posing an engineering challenge that demands a custom robotics systems that can complete tasks where humans cant operate. In addition to robotic-centric projects, such as the remote systems developed for the Fukushima Daiichi Nuclear Power Plant, robotics systems also play a critical support role for Kurions vitrification technologies, where remote operations are required."
Once the leaks are patched by the Fukushima Repair Manipulator, plant workers are expected to finally have the opportunity to remove the damaged fuel and debris from the reactor, drastically decreasing the output of contaminated water that is currently used to cool the core.
Featured Product
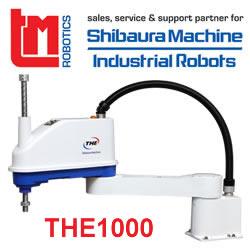