The Amazon Robotics Challenge. And, the winner is...
Of 25 teams from around the world, the winner of the Amazon Robotic Bin-Picking Challenge is the Technische Universität Berlin using Barrett's WAM robotic arm.
Seattle, WA, USA - The Amazon Picking Challenge is the centerpiece of the record-attendance IEEE Conference on Robotics & Automation in Seattle this year. There are 28 teams here from around the globe who have brought their hardware and software to the competition. Entries include robotic arms from ABB, Fanuc, Rethink Robotics, Universal Robots, and Yaskawa-Motoman. The competition just finished, and the scores are in... Technische Universität Berlin's Robotics and Biology Laboratory using Barrett's WAM arm in 1st place at 148 points followed, in 2nd place with 88 points, by the Massachusetts Institute of Technology using an ABB arm and a gripper with creative finger geometries. The 3rd place finisher came in at 35 points.
Prof. Oliver Brock of TU-Berlin remarks: "This has been a fantastic team effort. Every single member of our team contributed with enthusiasm and ingenuity, enabling us to produce a compelling showcase for mobile manipulation as a winning approach to industrial manipulation." Speaking to media, Townsend adds: "We are grateful that TU-Berlin won this competition, and of course especially grateful that they chose to use the WAM arm. The WAM's dexterity is world-class, the long-and-slender links allow the robot to reach easily in and around tight workspaces, and the WAM's famed backdrivability enables deft interactions with the environment. While it's a powerful combination of capabilities, the great creativity and dedication of the students and staff under Oliver's leadership has been essential, and it has been an absolute pleasure supporting them."
About Barrett Technology, Inc.
Barrett is the technology leader in high-performance robotic arms and hands for emerging applications requiring superior versatility. Barrett has pioneered advanced motor controls, for example its Puck, to enable the best force-controlled performance available; and its gearless transmissions are in a league of their own. To leverage these capabilities, its control architecture is totally open source with an active user community rapidly adding to a growing code base.
Featured Product
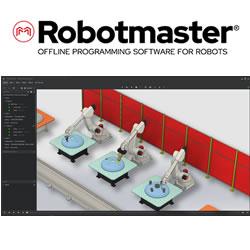