ADVANCED Motion Controls announces expanded micro Z-Drive capabilities
Available immediately are the AZBH10A4 and AZBD10A4 micro-sized analog plug-in brushless servo drives. These new models add Hall Velocity mode and Duty Cycle mode capabilities to the µZ series. Pronounced ‘micro-Z' these plug-in drives are the smallest off-the-shelf servo drives from ADVANCED Motion Controls and are designed for embedded applications in a wide range of industries including: Robotics, Lab Automation, Homeland Security/Military, Electric Mobility, Medical and Packaging. These micro sized servo drives are designed to drive brushless and brushed DC motors at a high switching frequency. To increase system reliability and to reduce cabling costs, the drives are designed for direct integration into your PCB. Weighing in at just 9 grams, these drives output 10A peak and 5A continuous and operate with a bus voltage range of 10-36VDC.
Available immediately are the AZBH10A4 and AZBD10A4 micro-sized analog plug-in brushless servo drives. These new models add Hall Velocity mode and Duty Cycle mode capabilities to the µZ series. Pronounced ‘micro-Z these plug-in drives are the smallest off-the-shelf servo drives from ADVANCED Motion Controls and are designed for embedded applications in a wide range of industries including: Robotics, Lab Automation, Homeland Security/Military, Electric Mobility, Medical and Packaging.
Designed without the need for a heatsink, the µZs are true featherweights with a high power to weight ratio. They are fully protected against over-voltage, under-voltage, over-current, over-heating, and short-circuits. Depending on the model, the drives interface with digital controllers that have analog ±10V or PWM/Direction commands. These servo drives require only a single unregulated isolated DC power supply, and are fully RoHS (Reduction of Hazardous Substances) compliant.
The AZBH10A4 with Hall Velocity mode uses the motor's commutation sensors for velocity feedback. This cost-effective control scheme is suited for medium to high speed applications where it provides excellent velocity control performance. Hall Velocity mode is ideal for velocity controlled conveyors, pumps, fans, and anywhere velocity control is needed.
The AZBD10A4 with Duty Cycle mode estimates velocity based on the PWM duty cycle to provide a limited level of velocity control without the need for a velocity feedback device such as an encoder. This control scheme is used in simple applications where velocity feedback is not available and precise velocity control is not necessary such as in some drive wheel applications, fans, pumps and lifts.
Both models each have a loop gain potentiometer used to tune the responsiveness, and an offset potentiometer to correct for any imbalances. Onboard jumpers control the inhibit logic, commutation phasing and feedback polarity.
These new models add to our existing line of current mode micro-sized servo drives. A current mode servo drive paired with a digital motion controller and high resolution feedback is an excellent solution for precise motion control applications such as voice coil control, instrumentation, positioning and more.
Features
• Designed for direct board-to-board integration.
• No heatsink and no need for additional heatsinking results in the smallest installed volume
• Feather weight, 9 grams
• Dimensions (in) 1.50 x 1.50 x 0.29
• Dimensions (mm) 38.1 x 38.1 x 7.34
• Large operational temperature range, 0-85C
• Compatible with low inductance motors
• AZBH10A4 Hall Velocity mode
• AZBD10A4 Duty Cycle mode
• Smallest form factor of any off-the-shelf servo drive from ADVANCED Motion Controls
• 40 kHz switching frequency
Projected Industries & Applications:
Robotics, Lab Automation, Homeland Security/Military, Electric Mobility, Medical, Packaging and all Embedded Systems
Featured Product
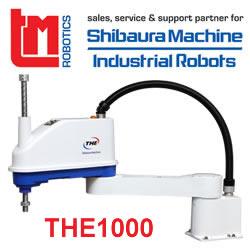