The Future of Underwater Robotics
Imagine a robot that can manage aquaculture projects, repair oil pipelines, and scan the seabed - all without risking human life. Nauticus Robotics' flagship robot, Aquanaut, meets these challenges while running solely on electric power.
Multi-axis motion control drives pipe-based robots
Surveying and maintaining underground pipes can be complex and resource intensive. To streamline the process, construction and facility management teams are increasingly turning to robots that can provide inspection as well as repair.
Press Brake Robots: Transforming Sheet Metal Bending with Precision and Efficiency
Press brake robots eliminate the challenges of manual sheet metal bending, such as inconsistencies, high labor costs, and workplace hazards. By leveraging robotic arms, sensors, and advanced software, these systems significantly improve accuracy and repeatability.
Developing robotic solutions: partnering for success in micro-motion control
To turn a motion concept into reality, dedicated engineering expertise can be invaluable. Not only can motion engineering support help to improve performance and reliability, but a design partnership can also optimize commercial viability - and reduce time to market.
Integrating Servo Drives with Robotics: Key Considerations for Seamless Automation
In this article, we will explore the key considerations for integrating servo drives with robotics to achieve smoother, more effective automation systems.
Fast Hexapod Improves Aircraft Manufacturing Process
PI presented a new, high-speed hexapod at the International Aerospace Exhibition ILA Berlin in June 2024, as a partner in the LuFo VI-1: ADMAS (Advanced Machining and Sealing) research project.
What Are the Secrets to Optimizing Motion Control in Robots?
Motion control optimization is about more than ensuring a robot can move. It must also move correctly; meeting the ideal speed, power, direction, length and timing. Assurance in each of these categories is necessary because these are what separate robots from human employees
200 Times Faster Subsea Inspection
Precise motion control is helping a new subsea inspection device achieve highly accurate inspection with the fastest-yet speeds of data collection.
SUPPLIER SELECTION FOR CRITICAL MOTION CONTROL APPLICATIONS
In this article, I attempt to arm manufacturers with the questions that they need to ask to ensure that the motion control solution option chosen is right first time and up to the job. These questions should ideally focus on not just capabilities but also values.
Solving Challenges in Machine-Robot Coordination
Using a single machine controller with robot kinematic control built-in means you don't need a separate controller for the robot or series of robots. This integration also puts robot and machine functions into just one development environment.
Improving Image Stabilization with Hexapod 6-Axis Motion Simulators for More Reliable Image Capturing
Taking sharp pictures despite fast changing lighting and ambient conditions, recognizing traffic signs or road markings in driver assistance systems, or identifying dangerous situations in surveillance systems - all of this is possible today with the help of modern cameras.
MCRI Webcast Series - Robotics Roundtable
Motion Controls Robotics (MCRI) is hosting a monthly, summer webcast series in 2021. MCRI provides automation solutions for customers by designing and building turn-key end of line applications, fulfillment solutions, and general material handling automation.
Motion Control Goes Small
Machine designers are increasingly asked to build systems that take up less space, operate on less power, and run with higher performance. Thankfully motion controls are answering the call with new motors, new sensors, and new architectures.
10 Different Options For Controlling Linear Actuators
Below you will find ten different options for controlling linear actuators. This list is intended to give you an overview of what's possible for linear actuator control. It's not exhaustive, there are other options, but these are the ones that will work for most people.
Speed Reducers & Proper Shaft Alignment for Motion Control Applications
While alignment may be within acceptable tolerances during installation, deflection due to loads and thermal expansion or contraction may lead to misalignment. The use of an appropriate flexible coupler can compensate for such minor variations in alignment.
Records 1 to 15 of 56
Featured Product
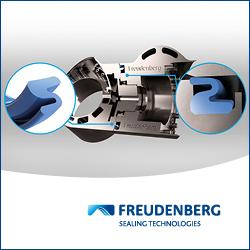
IP Seals for Robots
Freudenberg Sealing Technologies' IPRS (Ingress Protection Seals for Robots) provides reliable protection for robotic systems operating in harsh environments. Designed to prevent dust, moisture, chemicals, and wear from compromising performance, IPRS extends service life and reduces maintenance. The adaptive Z-shaped geometry ensures sealing integrity under continuous motion, making it ideal for high-speed automation and outdoor applications. Manufactured with high-performance elastomers such as Fluoroprene XP and EPDM, IPRS offers exceptional resistance to lubricants, cleaning agents, and extreme temperatures. This makes it the perfect solution for six-axis robots, SCARA robots, AMRs, AGVs, and cobots.
With its low-friction design and durable materials, IPRS enhances energy efficiency and operational reliability in industrial and autonomous robotics. Learn more about our IPRS Seals