Dynamic Tooling one of OCTOPUZ's versatile features
OCTOPUZ not only makes the complex simple, but it can also help your company save time and improve safety through Dynamic Model Simulation. Also known as Dynamic Tooling, it is an OCTOPUZ feature that shows how objects can change when they're physically pushed during a robotic automation process.
OCTOPUZ not only makes the complex simple, but it can also help your company save time and improve safety through Dynamic Model Simulation. See it in action on the 'OCTOPUZrobotics' YouTube page!
Also known as Dynamic Tooling, this OCTOPUZ feature uses simulation to show how objects can change when theyre physically pushed during an automation process. Its ideal for anyone using compliance tooling or in situations where pushing on a part causes a change in tooling shape. By allowing the tooling to maintain the correct shape at different points, OCTOPUZ offers greater accuracy in collision detection during the simulation.
Dynamic Tooling can also measure, record and then show how far the tool has compressed, which allows the force on the part to be calculated. This can be useful, and sometimes necessary, for advanced applications. Once set up, the Dynamic Tooling feature is completely automatic.
Not commonly available in automation software, Dynamic Tooling is ideal for applications that involve grinding, sanding, buffing or polishing. Using OCTOPUZs Dynamic Tooling feature can lead to increased productivity since less time is spent checking for collisions. Theres also the benefit of greater safety by using simulation to check for potential collisions before creating code.
OCTOPUZ is a revolutionary software tool that combines the offline programming of robots with manufacturing process simulation. It provides a mainstream, versatile, powerful and effective solution for all of your robotic challenges. Dynamic Tooling is just one of several benefits offered by OCTOPUZ. The ability to program multiple robots, application versatility, complex kinematics systems and a versatile CAM interface make the software ideal for path-sensitive robot applications.
To learn more about OCTOPUZ and Dynamic Tooling, or to arrange for a personalized demonstration, call 1-800-529-5517, visit www.OCTOPUZ.com or email info@octopuz.com
About OCTOPUZ
OCTOPUZ is an intelligent offline robot programming and simulation software ideal for any path-sensitive application. Created by In-House Solutions, the company took a revolutionary approach by combining the offline programming of robots with a manufacturing process simulation. Today, OCTOPUZ provides a mainstream, versatile, powerful and effective solution for any robotic challenge.
About In-House Solutions
More than 27 years ago, In-House Solutions began reselling and developing powerful software tools accessible to small- and medium-sized manufacturers. Today, the company provides CAD/CAM, DNC, PCMM and OCTOPUZ robotic programming software solutions to organizations of all sizes. The In-House Solutions team of experts, with offices in the U.S., Canada and Germany, are dedicated to selling, supporting, developing and implementing a full spectrum of software tools, particularly those specializing in NC programming and optimization, shop floor DNC communications and offline programming of industrial robots. In-House Solutions is the Canadian Mastercam distributor, and OCTOPUZ completes the companys software solutions for manufacturing.
Featured Product
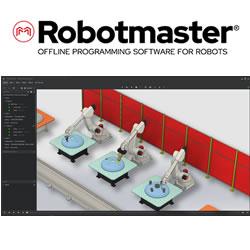
Robotmaster® 2024
Program multi-robot cells and automatically solve robotic errors with ease. Hypertherm Associates announces a new version to its robotic programming software. Robotmaster 2024 addresses key market trends including the support for programming multiple robots in a single work cell and the demand for automatic trajectory optimization and robotic error correction.