Hoffmann+Krippner Shows How to Pick the Right Potentiometer Sensor for Your Application
New White Paper for Developers of Industrial Automation systems and solutions, medical equipment and devices, kitchen appliances and handheld power tools --- Potentiometers can provide highly precise sensing and measurement for linear or rotary movement
August 19, 2015 - Alpharetta, GA
Hoffmann + Krippner Inc. today posted a new white paper - How to Choose the Right Potentiometer for Reliable Position Sensing. It can be downloaded at http://www.hoffmann-krippner.com/whitepapers.html
Created to help design engineers understand how membrane potentiometer sensors work and how to pick the right type of membrane potentiometer for their project, this new Hoffmann+Krippner white paper covers the various types of potentiometers, potentiometer development history, their various components and materials, and an overview looking at the technical issues of printed potentiometers and foil (membrane)/ The paper also covers the various tech specifications of accuracy and linearity when specifying potentiometers.
"Specifying or designing a potentiometer sensors is a complex challenge for many developers, especially those now looking to create Internet connected devices and solutions," says Jens Kautzor, CEO of Hoffman + Krippner, Inc. "This new guide provides an easy to understand high level look at these technologies as well as a detailed explanation of the most important technical specifications and how to understand them."
Company Background
The Hoffmann + Krippner Group, with sales offices around the globe, specializes in input and output systems as well as sensors. Headquartered in Germany, Hoffmann + Krippner has manufactured German-engineered, high quality products for over 35 years. As the North American member of the Group, Hoffmann + Krippner, Inc. delivers these engineering, design and manufacturing services to the US and Canadian market.
Featured Product
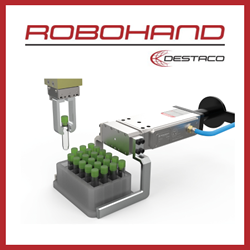
DESTACO - Revolutionizing Industrial Automation
Looking for a reliable solution to enhance your automation process? Look no further than the DESTACO Robohand Grippers. These grippers are designed for the modern world of robotics, offering unparalleled performance and precision. Whether you need to grip fragile items, irregularly shaped objects, or heavy-duty components, the DESTACO Robohand Grippers have got you covered. Their modular design allows for quick and easy customization, ensuring a perfect fit for your application.