Zimmer Group brings low-price gripper to the market
The pioneer in grippers is now offering its customers a pneumatic parallel gripper in the form of the GPP1000 series.
Zimmer Group has further expanded its product range to include cost-effective yet robust automation components. The pioneer in grippers is now offering its customers a pneumatic parallel gripper in the form of the GPP1000 series. This gripper makes profitable production possible thanks to its remarkably low price, which is a dream come true for many customers.
The new gripper series GPP1000s unbeatably affordable price not only makes exceptionally cost-effective production a reality but also offers 100N gripping force in three different strokes (4 mm, 8 mm, 16 mm) per gripper jaw. This single-acting gripper is supplied for use as an external gripper, for pressure-free opening using reset spring. A few simple manual adjustments are all that is needed to convert this gripper so that its jaws are closed when not under pressure. This means the gripper can also be used as an internal gripper.
Each gripper has two grooves for holding the magnetic field sensors used to sense the gripper's position. The grippers are supplied with a glasfiber reinforced gripper jaw set and the material required to attach them. However, customer-specific gripper jaws can be installed at any time.
To make it easier for its customers to select the best product, Zimmer Group has divided its product portfolio into application profiles. The GPP1000 belongs to the AP1 base class, whose products are designed to handle all the essential tasks with a special emphasis on cost-effectiveness.
Despite its very reasonable price, the GPP1000 offers the same tried-and-tested quality you expect from all Zimmer Group products. With the ability to run for up to 2 million cycles without maintenance, it meets all the requirements for reliable, cost-effective production!
Featured Product
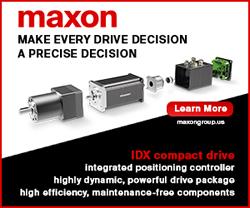
The maxon IDX Compact Drive with Integrated Positioning Controller
The compact brushless EC-i motor combined with an EPOS4 positioning controller delivers a highly dynamic, powerful drive package with field-oriented control (FOC), high efficiency, and maintenance-free components in a high-quality industrial housing. The maxon IDX drives are suitable for use across the entire speed range (from standstill to maximum speed) and have an extremely high overload capability. Together with a positioning controller, the integrated sensor (single turn) enables absolute positioning.