KUKA ROBOTS WELD RELIABLY IN MINI ROBOTIC CELL
A mini robotic cell developed by integrator Paul von der Bank GmbH is in operation at Brüninghaus & Drissner in Hilden. In the confined space of this "Welding To Go" (WTG) 1200 cell, a KUKA KR 6 R 700 sixx robot from the AGILUS series reliably performs welding tasks.
A mini robotic cell developed by integrator Paul von der Bank GmbH is in operation at Brüninghaus & Drissner in Hilden. In the confined space of this "Welding To Go" (WTG) 1200 cell, a KUKA KR 6 R 700 sixx robot from the AGILUS series reliably performs welding tasks.
KUKA KR AGILUS ROBOT FOR PARTICULARLY HIGH WORKING SPEEDS
"With the same dimensions as a Euro pallet - 1200x800 mm - the WTG 1200 is the smallest robotic cell on the market for arc welding," explains Cornelia Hornemann, responsible for product launch, project management and production planning at Paul von der Bank. Furthermore, depending on the specific requirements of the customer, the optimum small robot from the KR AGILUS series can be flexibly operated in the cell. The robots of the KR AGILUS series are systematically designed for particularly high working speeds. The KR 6 R700 sixx integrated into the mini robotic cell at Brüninghaus & Drissner, for example, has a maximum payload capacity of 6 kg and a reach of approximately 706 mm. The sliding doors of the WTG 1200 can optionally be opened either automatically or manually before a worker loads the workpieces into the welding fixture. Once the door has closed, the robot starts its welding tasks.
KUKA KR 6 R700 SIXX SMALL ROBOT ACHIEVES ALMOST 50% BOOST IN PRODUCTIVITY
"At our plant, the WTG 1200 works reliably in 3-shift operation," explains Markus Nickolai, Head of Production at Brüninghaus & Drissner. With great success: the mini robotic cell has resulted in significant productivity gains of up to 50 percent, as the operator is now able to prepare the next workpieces while automatic production is in progress. That is not all, however: thanks to the repeatability of the small robot, the quality of the weld seams has also improved noticeably. It is therefore no surprise that Paul von der Bank GmbH is already working on the next mini-cell generation with KUKA robots for its customers. The WTG 1500 will then have an external axis for turning the welding fixture.
Featured Product
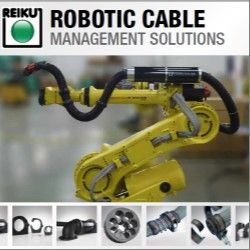
REIKU's Cable Saver™ - The Most Versatile Modular Robotic Cable Management Solution
REIKU's Cable Saver™ Solution eliminates downtime, loss of revenue, expensive cable and hose replacement costs, maintenance labor costs. It's available in three sizes 36, 52 and 70 mm.
All of the robots cables and hoses are protected when routed through the Cable Saver™ corrugated tubing.The Cable Saver™ uses a spring retraction system housed inside the Energy Tube™ to keep this service loop out of harms way in safe location at the rear of the Robot when not required. The Cable Saver™ is a COMPLETE solution for any make or model of robot. It installs quickly-on either side of the robot and has been tested to resist over 15 million repetitive cycles.
REIKU is committed to providing the most modular, effective options for ensuring your robotic components operate without downtime due to cable management.
www.CableSaver.com